-
- News
- Books
Featured Books
- pcb007 Magazine
Latest Issues
Current IssueInventing the Future with SEL
Two years after launching its state-of-the-art PCB facility, SEL shares lessons in vision, execution, and innovation, plus insights from industry icons and technology leaders shaping the future of PCB fabrication.
Sales: From Pitch to PO
From the first cold call to finally receiving that first purchase order, the July PCB007 Magazine breaks down some critical parts of the sales stack. To up your sales game, read on!
The Hole Truth: Via Integrity in an HDI World
From the drilled hole to registration across multiple sequential lamination cycles, to the quality of your copper plating, via reliability in an HDI world is becoming an ever-greater challenge. This month we look at “The Hole Truth,” from creating the “perfect” via to how you can assure via quality and reliability, the first time, every time.
- Articles
- Columns
- Links
- Media kit
||| MENU - pcb007 Magazine
Aurora Circuits on Ultra-Heavy Copper PCBs
August 3, 2020 | Dan Beaulieu, D.B. Management GroupEstimated reading time: 3 minutes
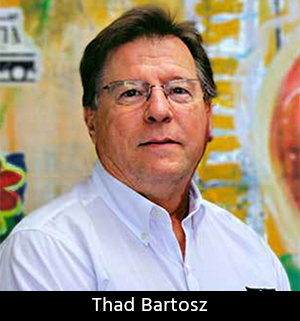
It’s always fun to talk with a company that can do something different—in this case, ultra-heavy copper PCBs, meaning over 20-ounce copper. Wanting to know more about this, I talked to Aurora Circuits Director of Business Development Thad Bartosz, who is one of our industry experts when it comes to ultra-heavy copper technology.
Dan Beaulieu: Thad, it’s good talking to you today. Let’s start with the basics. What is heavy copper?
Thad Bartosz: Heavy copper used to be defined as 4–5 ounce, but we do that for a snack. Aurora is capable of fabricating SS, NPTH, PTH, and multilayer types with up to 20-oz copper layers.
Beaulieu: What defines ultra-heavy copper?
Bartosz: Ounces of copper have been defined in ounces per square foot of area on the process panel. The thickness of the copper foil is based on 0.0014” per oz. Copper weights of 4–5 ounces are made with electrodeposited copper (ED), and ultra-heavy copper sheets are made with rolled annealed (RA) copper that must be treated to laminate to dielectrics used in fabrication.
Beaulieu: How many ounces of copper can you do at Aurora?
Bartosz: We have delivered PCBs with etched copper up to 20 ounces and would work with customers that may require any copper thickness.
Beaulieu: Why doesn’t every shop build this technology?
Bartosz: You need to have the proper equipment and process capabilities—some of these are customer or Aurora proprietary—so that you can fabricate a usable product that meets customer requirements.
Beaulieu: How did you get involved with this technology?
Bartosz: We have been building ultra-heavy copper products since 2003 when a customer asked if we could do this as they were having issues with their current source.
Beaulieu: What special equipment and processes do you have that allow you to build ultra-heavy copper boards?
Bartosz: As I mentioned earlier, these are processes that have been developed over years of sampling and production processing. We start with a sample run to establish a feasible process and then scale up for production. Etching is normally a big factor as well as machining, so you acquire equipment to properly process the PCB to make an acceptable finished product.
Beaulieu: What technology requires ultra-heavy copper?
Bartosz: Circuit boards that need high current or thermal dissipation like solar and wind power collection, aerospace/military, telecommunications, and automotive applications.
Beaulieu: What kind of end-products need it?
Bartosz: Some products include automotive junction boxes, battery management systems, and high-power circuits that have MOSFETs, IGBTs, and other high-current components, running hundreds of amps through the circuitry. For those who may not know, MOSFETs and IGBTs are a couple of power devices/components that can handle high-voltage and high-current needs. You will find them on inverters, converters, and power supplies.
Beaulieu: How do you think it will be used in the future?
Bartosz: Currently, designs have been made for power distribution, power collection, battery-powered transportation, and LED lighting. Future use will depend on new applications needed in the marketplace. You also need a supplier that changes with the market to meet these specialized needs. It will definitely be used more in the future.
Beaulieu: Is this kind of technology being designed right now?
Bartosz: Yes, it is still used in the automotive and power markets, such as new EV and autonomous vehicles where battery technology has higher current requirements and power-generation systems, solar, wind, or conventional types as their technology changes.
Beaulieu: How many ultra-heavy copper boards have you built?
Bartosz: Aurora has shipped over five million boards of single-sided, PTH, and multilayer designs over the last 10 years. Many of these were for junction boxes or battery systems in automobiles. For a few years, we shipped over 400,000 6/6 copper PCBs to China. We have processed over 800 tons (based on oz/sq ft) and over 1.7 million square feet without any EPA violations.
Beaulieu: Before we end, tell us a little bit about Aurora Circuits.
Bartosz: We have over 60 years of experience in printed circuit fabrication, providing advanced thermal management and interconnect technology solutions for PCB designs and specialty products. Product specialty areas include polymer thick-film (PTF) resistors, metal-clad materials for LED lighting and other markets, durable plating for contact areas, and, of course, ultra-heavy copper. We partner with companies to help them to maximize profitability and production sustainability.
Beaulieu: Thank you, Thad.
Bartosz: No problem, Dan.
Read more about Aurora Circuits and ultra-heavy copper PCBs here.
Testimonial
"Advertising in PCB007 Magazine has been a great way to showcase our bare board testers to the right audience. The I-Connect007 team makes the process smooth and professional. We’re proud to be featured in such a trusted publication."
Klaus Koziol - atgSuggested Items
How Good Design Enables Sustainable PCBs
08/21/2025 | Gerry Partida, Summit InterconnectSustainability has become a key focus for PCB companies seeking to reduce waste, conserve energy, and optimize resources. While many discussions on sustainability center around materials or energy-efficient processes, PCB design is an often overlooked factor that lies at the heart of manufacturing. Good design practices, especially those based on established IPC standards, play a central role in enabling sustainable PCB production. By ensuring designs are manufacturable and reliable, engineers can significantly reduce the environmental impact of their products.
50% Copper Tariffs, 100% Chip Uncertainty, and a Truce
08/19/2025 | Andy Shaughnessy, I-Connect007If you’re like me, tariffs were not on your radar screen until a few months ago, but now political rhetoric has turned to presidential action. Tariffs are front-page news with major developments coming directly from the Oval Office. These are not typical times. President Donald Trump campaigned on tariff reform, and he’s now busy revamping America’s tariff policy.
Global PCB Connections: Understanding the General Fabrication Process—A Designer’s Hidden Advantage
08/14/2025 | Markus Voeltz -- Column: Global PCB ConnectionsDesigners don’t need to become fabricators, but understanding the basics of PCB fabrication can save you time, money, and frustration. The more you understand what’s happening on the shop floor, the better you’ll be able to prevent downstream issues. As you move into more advanced designs like HDI, flex circuits, stacked vias, and embedded components, this foundational knowledge becomes even more critical. Remember: the fabricator is your partner.
MKS’ Atotech to Participate in IPCA Electronics Expo 2025
08/11/2025 | AtotechMKS Inc., a global provider of enabling technologies that transform our world, announced that its strategic brands ESI® (laser systems) and Atotech® (process chemicals, equipment, software, and services) will showcase their latest range of leading manufacturing solutions for printed circuit board (PCB) and package substrate manufacturing at the upcoming 17th IPCA Show to be held at Pragati Maidan, New Delhi from August 21-23, 2025.
MKS Showcases Next-generation PCB Manufacturing Solutions at the Thailand Electronics Circuit Asia 2025
08/06/2025 | MKS Instruments, Inc.MKS Inc, a global provider of enabling technologies that transform our world, today announced its participation in Thailand Electronics Circuit Asia 2025 (THECA 2025), taking place August 20–22 at BITEC in Bangkok.