-
-
News
News Highlights
- Books
Featured Books
- pcb007 Magazine
Latest Issues
Current IssueThe Hole Truth: Via Integrity in an HDI World
From the drilled hole to registration across multiple sequential lamination cycles, to the quality of your copper plating, via reliability in an HDI world is becoming an ever-greater challenge. This month we look at “The Hole Truth,” from creating the “perfect” via to how you can assure via quality and reliability, the first time, every time.
In Pursuit of Perfection: Defect Reduction
For bare PCB board fabrication, defect reduction is a critical aspect of a company's bottom line profitability. In this issue, we examine how imaging, etching, and plating processes can provide information and insight into reducing defects and increasing yields.
Voices of the Industry
We take the pulse of the PCB industry by sharing insights from leading fabricators and suppliers in this month's issue. We've gathered their thoughts on the new U.S. administration, spending, the war in Ukraine, and their most pressing needs. It’s an eye-opening and enlightening look behind the curtain.
- Articles
- Columns
- Links
- Media kit
||| MENU - pcb007 Magazine
Chapter 2 Excerpt from the Book ‘Thermal Management: A Fabricator's Perspective’
December 21, 2020 | Anaya Vardya, American Standard CircuitsEstimated reading time: 1 minute
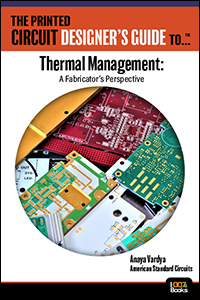
Chapter 2: IMPCBs or MCPCBs
Insulated metal PCBs (IMPCB) or metal-clad PCBs (MCPCB) are a thermal management design that utilizes a layer of solid metal to dissipate the heat generated by the various components on the PCBs. When metal is attached to a PCB, the bonding material can either be thermally conductive but electrically isolative (IMPCBs or MCPCBs), or in the case of RF/microwave circuits, the bonding material may be both electrically and thermally conductive. The reason that RF designers usually have the bonding material thermally and electrically conductive is that they are using this not only as a heat sink but also as part of the ground layer. The design considerations are quite different for these different applications.
This chapter will focus on the IMPCB design considerations, and Chapter 4 will focus on RF thermal management. We will focus on things designers should be discussing with their PCB supplier to ensure manufacturability and a successful product launch. Since the choices, options, and decisions can be extremely complicated, it is critical to engage early and collaborate with the PCB fabricator about the specific design to ensure the most cost-effective solution.
Some of the more common applications of IMPCBs include:
- Power Conversion: Thermal-clad offers a variety of thermal performances, is compatible with mechanical fasteners, and is highly reliable
- LEDs: Using thermal-clad PCBs ensures the lowest possible operating temperatures and maximum brightness, color, and life
- Photovoltaic Energy: Renewable energy to power telecommunications, military camps, residential and commercial structures, and battery charging stations
- Motor Drives: Thermal-clad dielectric choices provide the electrical isolation needed to meet operating parameters and safety agency test requirements
- Solid-State Relays: Thermal-clad offers a very thermally efficient and mechanically robust substrate
- Automotive: The automotive industry uses thermal-clad boards, as they need long term reliability under high operating temperatures coupled with their requirement of effective space utilization
To download The Printed Circuit Designer’s Guide to…Thermal Management: A Fabricator’s Perspective, click here. You can also view other titles in our full library. Check out other books from American Standard Circuits, including The Printed Circuit Designer’s Guide to… Fundamentals of RF/Microwave PCBs and Flex and Rigid-Flex Fundamentals.
Suggested Items
DownStream Acquisition Fits Siemens’ ‘Left-Shift’ Model
06/26/2025 | Andy Shaughnessy, I-Connect007I recently spoke to DownStream Technologies founder Joe Clark about the company’s acquisition by Siemens. We were later joined by A.J. Incorvaia, Siemens’ senior VP of electronic board systems. Joe discussed how he, Rick Almeida, and Ken Tepper launched the company in the months after 9/11 and how the acquisition came about. A.J. provides some background on the acquisition and explains why the companies’ tools are complementary.
Elementary Mr. Watson: Retro Routers vs. Modern Boards—The Silent Struggle on Your Screen
06/26/2025 | John Watson -- Column: Elementary, Mr. WatsonThere's a story about a young woman preparing a holiday ham. Before putting it in the pan, she cuts off the ends. When asked why, she shrugs and says, "That's how my mom always did it." She asks her mother, who gives the same answer. Eventually, the question reaches Grandma, who laughs and says, "Oh, I only cut the ends off because my pan was too small." This story is a powerful analogy for how many PCB designers approach routing today.
Connect the Dots: The Future of PCB Design and Manufacturing
07/02/2025 | Matt Stevenson -- Column: Connect the DotsFor some time, I have been discussing the increasing complexity of PCBs and how designers can address the constantly evolving design requirements associated with them. My book, "The Printed Circuit Designer’s Guide to… Designing for Reality," details best practices for creating manufacturable boards in a modern production environment.
Siemens Turbocharges Semiconductor and PCB Design Portfolio with Generative and Agentic AI
06/24/2025 | SiemensAt the 2025 Design Automation Conference, Siemens Digital Industries Software today unveiled its AI-enhanced toolset for the EDA design flow.
Cadence AI Autorouter May Transform the Landscape
06/19/2025 | Andy Shaughnessy, Design007 MagazinePatrick Davis, product management director with Cadence Design Systems, discusses advancements in autorouting technology, including AI. He emphasizes a holistic approach that enhances placement and power distribution before routing. He points out that younger engineers seem more likely to embrace autorouting, while the veteran designers are still wary of giving up too much control. Will AI help autorouters finally gain industry-wide acceptance?