-
-
News
News Highlights
- Books
Featured Books
- pcb007 Magazine
Latest Issues
Current IssueThe Hole Truth: Via Integrity in an HDI World
From the drilled hole to registration across multiple sequential lamination cycles, to the quality of your copper plating, via reliability in an HDI world is becoming an ever-greater challenge. This month we look at “The Hole Truth,” from creating the “perfect” via to how you can assure via quality and reliability, the first time, every time.
In Pursuit of Perfection: Defect Reduction
For bare PCB board fabrication, defect reduction is a critical aspect of a company's bottom line profitability. In this issue, we examine how imaging, etching, and plating processes can provide information and insight into reducing defects and increasing yields.
Voices of the Industry
We take the pulse of the PCB industry by sharing insights from leading fabricators and suppliers in this month's issue. We've gathered their thoughts on the new U.S. administration, spending, the war in Ukraine, and their most pressing needs. It’s an eye-opening and enlightening look behind the curtain.
- Articles
- Columns
- Links
- Media kit
||| MENU - pcb007 Magazine
Finding Process Improvement Opportunities in Training
February 25, 2021 | Nolan Johnson, PCB007Estimated reading time: 3 minutes
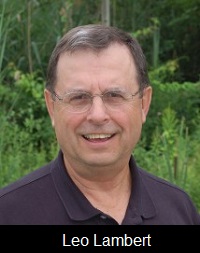
Nolan Johnson speaks with Leo Lambert of EPTAC about training the next generation out of high school and vocational schools, and how his company continues to improve processes, grow and adapt to changing requirements while fulfilling its mission to deliver technical certification training.
Nolan Johnson: Leo, what’s happening in the training space lately? Have our recent pandemic-driven restrictions changed how you deliver your product? Have your instructors found success in this environment?
Leo Lambert: They must all have the same interpretations from our end, so to speak. But to get our teachers involved in the new technologies, most of that happens in conversations with our customers. What’s going on? Well, the technology itself from assembling components on printed circuit boards and soldering those components in place is one thing, but the technology has improved relative to density of the product, such as—cellphones, for example, and all that is packed into that product. Then of course, there’s the technology of the components themselves.
We did an SMTA tour at one of the major military contractors in the area. Their boards were very low technology, but the technology of their product was based in their componentry. So, while this customer may not need new technology for board circuit design and assembly, we still try to bring them up to date, relative to the new processes being used in fabricating boards, new soldering technologies, and new metals to replace the high temp alloys with the new lower temperature ones that are starting to come out.
There are a lot of new soldering irons today that are much better than the previous ones, so we cover the use of those new tools. We’ve changed all our soldering irons, simply because it shows the students what they can do with the new equipment, and specifically since the components are getting smaller. Additionally, there’s a lot of new information that comes from the component manufacturers as to how to secure their componentry on printed circuit boards. They don’t want soldering irons at very high temperatures touching those components because they’re going to crack.
The intent is to be able to teach the new technology to the students. Initially we taught through-hole and hand-soldering techniques. We still teach those processes for through-hole technology, but since then, the component sizes have shrunk down to the size of a speck of pepper. The methodology of assembling those, and the specific paste required, has changed. We need to have conversations with the component and the material suppliers as to how to apply and use their materials. Our knowledge is developed with two conversations, one being with the clients who are in the training room and the process developments they’re doing. Secondly, it’s with the people making the material—paste and solder manufacturers like Indium, AIM and Alpha—and finding out what they’re doing, because they must be developing new products for the new technologies in process.
The other conversation is in the relationships from the cleanliness programs. There are a lot of issues going on with cleanliness. Historically these processes used solvents for cleaning printed circuit boards, and when aqueous cleaning came into vogue it created an entirely new process with new materials. The question then was, how are those materials going to be used and processed so they don’t harm the product or harm the individuals who are using them? That’s how we developed our knowledge of the new technologies that are evolving. As trainers we don’t get too involved with the electronic functionality portion of the circuits, but rather the assembly of those electronic circuits.
Johnson: What I’m hearing is that, while the basic skill set that you teach might be the same, it is also at the same time more complex because of so many factors. You have to be concerned with more things. I mean, back in the Dark Ages, it was through-hole, one kind of board, and one solder, and there was plenty of room to do that and if you didn’t learn how to solder, well, you were good enough. That’s not true anymore.
Lambert: Correct. One of the things that happened is the laminate materials changed. Today there are many microwave products being developed, and we need to know how to handle those versus the traditional FR-4 materials, and so on. We have to learn how to handle those new laminates, and then know how to teach that to the students.
To read this entire interview, which appeared in the January 2021 issue of PCB007 Magazine, click here.
Suggested Items
Driving Innovation: Direct Imaging vs. Conventional Exposure
07/01/2025 | Simon Khesin -- Column: Driving InnovationMy first camera used Kodak film. I even experimented with developing photos in the bathroom, though I usually dropped the film off at a Kodak center and received the prints two weeks later, only to discover that some images were out of focus or poorly framed. Today, every smartphone contains a high-quality camera capable of producing stunning images instantly.
Hands-On Demos Now Available for Apollo Seiko’s EF and AF Selective Soldering Lines
06/30/2025 | Apollo SeikoApollo Seiko, a leading innovator in soldering technology, is excited to spotlight its expanded lineup of EF and AF Series Selective Soldering Systems, now available for live demonstrations in its newly dedicated demo room.
Indium Corporation Expert to Present on Automotive and Industrial Solder Bonding Solutions at Global Electronics Association Workshop
06/26/2025 | IndiumIndium Corporation Principal Engineer, Advanced Materials, Andy Mackie, Ph.D., MSc, will deliver a technical presentation on innovative solder bonding solutions for automotive and industrial applications at the Global Electronics A
Fresh PCB Concepts: Assembly Challenges with Micro Components and Standard Solder Mask Practices
06/26/2025 | Team NCAB -- Column: Fresh PCB ConceptsMicro components have redefined what is possible in PCB design. With package sizes like 01005 and 0201 becoming more common in high-density layouts, designers are now expected to pack more performance into smaller spaces than ever before. While these advancements support miniaturization and functionality, they introduce new assembly challenges, particularly with traditional solder mask and legend application processes.
Knocking Down the Bone Pile: Tin Whisker Mitigation in Aerospace Applications, Part 3
06/25/2025 | Nash Bell -- Column: Knocking Down the Bone PileTin whiskers are slender, hair-like metallic growths that can develop on the surface of tin-plated electronic components. Typically measuring a few micrometers in diameter and growing several millimeters in length, they form through an electrochemical process influenced by environmental factors such as temperature variations, mechanical or compressive stress, and the aging of solder alloys.