ICT Webinar: Novel Materials and Methods for Printed Circuit Fabrication
March 2, 2021 | Pete Starkey, I-Connect007Estimated reading time: 4 minutes
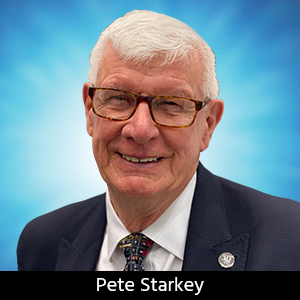
For the first time since its foundation in 1974, the Institute of Circuit Technology had no alternative than to conduct its Annual General Meeting online. The event, which took place on February 25, 2021, was remarkably well-attended, and was followed, as is traditional, by a technical seminar. The seminar became a webinar focused on novel materials and methods for printed circuit fabrication and moderated by ICT Chair Emma Hudson.
Tom Eldridge, CHASM Advanced Materials
The first presentation came from Tom Eldridge, business development manager with CHASM Advanced Materials, who gave an update on innovative transparent PCB materials for new markets. He commented that although indium tin oxide was established as the industry standard transparent conductor, dominating both glass and flexible market segments, its flexibility was limited, as was its transparency on plastic films, and it was not stretchable or formable. He listed as alternatives materials based on poly(3,4-ethylenedioxythiophene) (PEDOT), carbon nano-tubes, silver nano-wires, metal mesh, and carbon nano-tube hybrids. A proprietary hybrid of silver nano-wires and carbon nano-tubes was claimed to have better flexibility and formability than indium tin oxide, and to be more cost-effectively patterned. He showed examples of transparent flexible circuits patterned with this material.
Fabrication and processing were straightforward, with minimal capital investment since most PCB shops already had the required equipment. The hybrid material was a combination of ink and film. It acted as a pattern mask and, being a functional part of the end product, remained in place without stripping. CHASM’s lab facility consisted basically of a screen printing press, a convection oven and a conveyorised etching machine. Transparent film, supplied pre-coated with silver nano-wires, was screen printed with carbon nano-tube ink, then dried and etched in ferric nitrate or ferric/cupric chloride to leave the required conductive pattern. Applications included transparent heaters, transparent antennas, transparent lighting films and transparent touch sensors. Eldridge gave a video demonstration of a side-by-side comparison of conventional UHF flex antennas versus transparent examples produced with the new hybrid material, illustrating that equivalent signal strength and quality were consistently maintained.
Dr. Tom Jones, University of Dundee
Spinach might be perceived as an unlikely accelerator for electroless copper plating, but was the subject of the next presentation—a nature-inspired project to examine ways of reducing the toxicity of electronic fabrication processes. Dr. Tom Jones from the University of Dundee discussed the development of an innovative photo-catalyst for selective plating on polyimide-based substrates for micro-patterning circuitry.
Silver nanoparticles had been considered as a lower-cost alternative to colloidal palladium for catalysing electroless copper deposition, and these nanoparticles could be generated by photo-reduction of silver salts in solution. Research had indicated that the photosynthetic capability of chloroplasts present in spinach could significantly accelerate the photo-reduction reaction and yield a more effective catalyst for electroless deposition. Selective LED exposure of a surface pre-treated with ionic silver and sensitised with an alcoholic extract of spinach offered a photo-imaging process for creating circuit patterns in catalytic silver nanoparticles that could be subsequently built up with electroless copper. Dr Jones showed examples of patterns on polyimide substrates. A study of the mechanism of the photo-reduction reaction, using pure chlorophyll in place of spinach extract, gave anomalous results—the spectral peaks did not match. Further investigation revealed that potassium chloride was present in the spinach extract, and this was in fact the active ingredient rather than the chloroplasts themselves. X-ray diffraction analysis indicated the presence of silver chloride in the spinach-activated ionic silver surface coating, which was a reaction product of ionic silver with potassium chloride that had originated from the spinach. Jones pointed out that silver chloride was a typical light-sensitive constituent of traditional photographic film, and this explained its contribution to the photo-sensitisation process.
Dr. Sofya Danilova, Coventry University
Selective metallisation of textiles using a magnetic field was the theme of a research project at Coventry University, presented by Dr. Sofya Danilova. The objective was to find a lower-cost shorter-process-route alternative to lithography, avoiding hazardous chemistry and wastage of materials. It was proposed to use a magnetic template to define a circuit pattern in a catalytic material, and then build it up using electroless deposition. Traditional catalysts based on colloidal palladium or colloidal copper were not magnetic, so an alternative was required. A colloidal composite of metallic silver as the active component and iron oxide as the magnetic component was found to be effective. Magnetic deposition conditions had been optimised and Dr. Danilova showed examples of electroless copper plated onto thin FR4 material, areas of which had been activated using this catalyst.
Dr. Danilova demonstrated the use of templates, designed using software to simulate magnetic field distribution, and showed scanning electron micrographs of 500 micron lines produced in electroless copper. Woven polyester fabrics had been selectively metallised using the magnetic technique, although the pre-treatment of the textile had been shown to be an important consideration, as had the stirring method--magnetic stirrers were not recommended! The research had successfully demonstrated proof of concept, and future work would be directed at reliability testing of metallised textiles and investigating the properties of metallised textiles with high surface area.
Emma Hudson brought the proceedings to a close, thanking the contributors and all who had attended, and especially ICT technical director Bill Wilkie for his expert organisation of the event. She was optimistic that the Institute could soon return to its live seminar programme.
Suggested Items
RF PCB Design Tips and Tricks
05/08/2025 | Cherie Litson, EPTAC MIT CID/CID+There are many great books, videos, and information online about designing PCBs for RF circuits. A few of my favorite RF sources are Hans Rosenberg, Stephen Chavez, and Rick Hartley, but there are many more. These PCB design engineers have a very good perspective on what it takes to take an RF design from schematic concept to PCB layout.
Trouble in Your Tank: Causes of Plating Voids, Pre-electroless Copper
05/09/2025 | Michael Carano -- Column: Trouble in Your TankIn the business of printed circuit fabrication, yield-reducing and costly defects can easily catch even the most seasoned engineers and production personnel off guard. In this month’s column, I’ll investigate copper plating voids with their genesis in the pre-plating process steps.
Elephantech: For a Greener Tomorrow
04/16/2025 | Marcy LaRont, PCB007 MagazineNobuhiko Okamoto is the global sales and marketing manager for Elephantech Inc., a Japanese startup with a vision to make electronics more sustainable. The company is developing a metal inkjet technology that can print directly on the substrate and then give it a copper thickness by plating. In this interview, he discusses this novel technology's environmental advantages, as well as its potential benefits for the PCB manufacturing and semiconductor packaging segments.
Trouble in Your Tank: Organic Addition Agents in Electrolytic Copper Plating
04/15/2025 | Michael Carano -- Column: Trouble in Your TankThere are numerous factors at play in the science of electroplating or, as most often called, electrolytic plating. One critical element is the use of organic addition agents and their role in copper plating. The function and use of these chemical compounds will be explored in more detail.
IDTechEx Highlights Recyclable Materials for PCBs
04/10/2025 | IDTechExConventional printed circuit board (PCB) manufacturing is wasteful, harmful to the environment and energy intensive. This can be mitigated by the implementation of new recyclable materials and technologies, which have the potential to revolutionize electronics manufacturing.