With Flex, Sometimes You Gotta Break the Rules
April 5, 2021 | Tony Plemel, Flexible Circuit TechnologiesEstimated reading time: 2 minutes
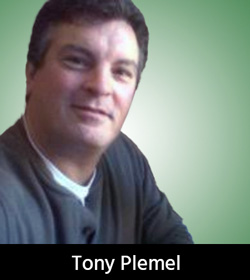
Sometimes in life, we need to break the rules. For example, in junior high I had a curfew but to have my first kiss, I had to break curfew. I got grounded, but it was worth it!
My last article was about reasons to follow IPC design and inspection rules. This time, we are discussing instances where, due to complex requirements, customers are not always able to follow the rules. I will also discuss some design options that will hopefully keep you from “getting grounded.”
Here are a few examples of when a customer would need to stretch the rules and supersede IPC-2223 and IPC-6013.
1. Insufficient real estate for IPC-suggested blind or buried via hole sizes.
2. Limited space requires bending a flexible circuit tighter than the IPC-2223 bend rules.
3. Insufficient real estate requires placing vias closer to the transition rigid-to-flex areas on a rigid-flex circuit.
4. Requiring tighter than normal tolerances.
Now, let’s go through these in greater detail.
1. Smaller than IPC-suggested blind or buried vias. As packages get smaller and real estate is at a premium, customers sometimes go smaller than the recommended ratio of 1:1 for blind or buried vias. Due to reliability concerns, the smallest recommended microvia is 100 µm (0.004”). If the design will not support 100 µm vias, it may be acceptable to drop to 75 µm if the 1:1 aspect ratio is strictly followed. So, the 75 µm via hole can only go 75 µm deep, or less. Be sure your flex supplier runs thermal shock testing on all plated vias and through-holes (especially blind vias under 100 µm) to ensure that they are reliable.
2. Bending a flexible circuit tighter than the IPC-2223 bend rules. A recent customer had a situation where a flex arm on a 2-layer flex circuit did not have room for a radius of 10:1 as recommended by IPC-2223. The circuit had to bend back 180 degrees upon itself. We recommended a forming fixture to create a repeatable bend. Within this fixture, a clamp was placed to ensure that once a droplet of super glue was added, the circuit bend was stabilized. This allowed a repeatable and reliable 2:1 bend ratio. It is critical on a reduced bend ratio application that once the circuit is formed, it is immediately constrained and not allowed to relax. Once all devices were in place and a few bends were made and glued, cross-sections were taken to ensure there was no cracking or elongation of the traces, or delamination in the coverlay. Since then, hundreds of thousands of circuits have been deployed in the field with zero quality issues. When the available room and the install scenario were considered, the solution we came up with was a success.
To read this entire article, which appeared in the March 2021 issue of Design007 Magazine, click here.
Suggested Items
The Global Electronics Association Releases IPC-8911: First-Ever Conductive Yarn Standard for E-Textile Application
07/02/2025 | Global Electronics AssociationThe Global Electronics Association announces the release of IPC-8911, Requirements for Conductive Yarns for E-Textiles Applications. This first-of-its-kind global standard establishes a clear framework for classifying, designating, and qualifying conductive yarns—helping to address longstanding challenges in supply chain communication, product testing, and material selection within the growing e-textiles industry.
IPC-CFX, 2.0: How to Use the QPL Effectively
07/02/2025 | Chris Jorgensen, Global Electronics AssociationIn part one of this series, we discussed the new features in CFX Version 2.0 and their implications for improved inter-machine communication. But what about bringing this new functionality to the shop floor? The IPC-CFX-2591 QPL is a powerful technical resource for manufacturers seeking CFX-enabled equipment. The Qualified Product List (QPL) helps streamline equipment selection by listing models verified for CFX compliance through a robust third-party virtual qualification process.
Advancing Aerospace Excellence: Emerald’s Medford Team Earns Space Addendum Certification
06/30/2025 | Emerald TechnologiesWe’re thrilled to announce a major achievement from our Medford, Oregon facility. Andy Abrigo has officially earned her credentials as a Certified IPC Trainer (CIT) under the IPC J-STD-001 Space Addendum, the leading industry standard for space and military-grade electronics manufacturing.
Magnalytix and Foresite to Host Technical Webinar on SIR Testing and Functional Reliability
06/26/2025 | MAGNALYTIXMagnalytix, in collaboration with Foresite Inc., is pleased to announce an upcoming one-hour Webinar Workshop titled “Comparing SIR IPC B-52 to Umpire 41 Functional & SIR Test Method.” This session will be held on July 24, 2025, and is open to professionals in electronics manufacturing, reliability engineering, and process development seeking insights into new testing standards for climatic reliability.
IPC Rebrands as Global Electronics Association: Interview With Dr. John W. Mitchell
06/22/2025 | Marcy LaRont, I-Connect007Today, following a major announcement, IPC is embracing the rapid advancement of technology with a bold decision to change its name to the Global Electronics Association. This name more accurately reflects the full breadth of its work and the modern realities of electronics manufacturing. In this exclusive interview, Global Electronics Association President and CEO Dr. John W. Mitchell shares the story behind the rebrand: Why now, what it means for the industry, and how it aligns with the organization’s mission.