-
- News
- Books
Featured Books
- pcb007 Magazine
Latest Issues
Current IssueInventing the Future with SEL
Two years after launching its state-of-the-art PCB facility, SEL shares lessons in vision, execution, and innovation, plus insights from industry icons and technology leaders shaping the future of PCB fabrication.
Sales: From Pitch to PO
From the first cold call to finally receiving that first purchase order, the July PCB007 Magazine breaks down some critical parts of the sales stack. To up your sales game, read on!
The Hole Truth: Via Integrity in an HDI World
From the drilled hole to registration across multiple sequential lamination cycles, to the quality of your copper plating, via reliability in an HDI world is becoming an ever-greater challenge. This month we look at “The Hole Truth,” from creating the “perfect” via to how you can assure via quality and reliability, the first time, every time.
- Articles
- Columns
- Links
- Media kit
||| MENU - pcb007 Magazine
Flex DFM: When All Things Must Be Considered
September 7, 2021 | Chris Clark, Flexible Circuit TechnologiesEstimated reading time: 3 minutes
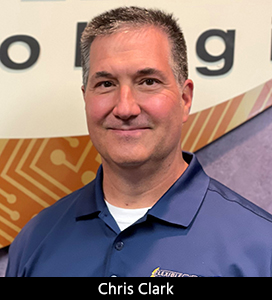
Engineers can’t possibly think of everything, every time.
One of the worst examples of an engineering failure is the Tacoma Narrows Bridge in Washington state that collapsed in 1940. The bridge was not engineered to withstand the environmental factors placed upon it by wind and weather.
I realize comparing a flex circuit to the Tacoma Narrows Bridge is a stretch (no pun intended), but the point is that no one wants to see a project fail after they’ve poured their heart and soul into it.
One of the best ways to avoid flex failures is by communicating with your flex fabricator early and often. Here are a couple key reasons why involving your flex and rigid-flex supplier early in the design of your product will help you save time and money—and produce a more reliable flex circuit.
Product Cost
Many things can impact the final cost of the product. Choosing suppliers with significant experience and knowledge that they are willing to share will, without a doubt, help control your costs in the long run. These industry experts will pose the dreaded “Yeah, but” questions that can keep your project on track. For example, “We certainly can build your circuit exactly as you have designed it. However, the small tail you have extending from the main body of your circuit is costing you lots of money.”
There are some instances in which shrinking something by only a quarter of an inch can greatly impact panel density, thereby lowering your production costs. Without knowledge of your supplier’s processing needs, you have no way of knowing if the dimensions of your part are an efficient use of the material. Many things factor into this including panel size, tooling holes, fiducials, and coupon requirements. In some instances, having your designs reviewed by an engineer with both circuit design and manufacturing experience may save you more than 25% in long term costs.
Another example is in yields. While it may be possible to build the circuit as you have it designed, a supplier with strong design for manufacturing (DFM) experience should be able to point out minor design changes that will increase yields measurably. For example, while a circuit may be able to be etched out of one-ounce foil, it may come at a reduced yield when compared to half-ounce foil. An experienced engineer should be able and willing to suggest materials based on the electrical and mechanical needs of your application. They should balance these requirements against manufacturability, allowing them to recommend materials that will be the most cost effective.
Time to Market
Let’s face it, time is money. Say you are working for a medical device company on a new project. You are well-versed in circuit design, so you decide not to engage with a circuit supplier offering DFM analysis. Instead, you think it will save time to work directly with a quick-turn house. After several weeks you receive the product and install it in your device. The product meets your needs both mechanically and electrically. You think, “Great, this is working exactly as planned.” Now it’s time for another round of parts so you go back to the same quick-turn shop and order a couple dozen more. The product is delivered, and it performs wonderfully. Teams are working in parallel on the qualification process. What the supplier didn’t tell you is that your circuit design and your drawing are in conflict. To achieve the impedance you are requiring, they use different materials than what you had specified. The issue wasn’t uncovered until a first article was performed on the low-rate production parts. Now the drawing and design must go through an ECO process that will take weeks. On top of that, the qualification process must start over, and you need to order more parts to perform FAI. Now the program has your team under the magnifying glass. All of this could have been prevented by taking a little bit of up-front time and working with a supplier that is willing to perform due diligence at the design review stage.
To read this entire article, which appeared in the August 2021 issue of PCB007 Magazine, click here.