Designing Through Supply Chain Pain
September 13, 2022 | Chris Young, Young Engineering ServicesEstimated reading time: 2 minutes
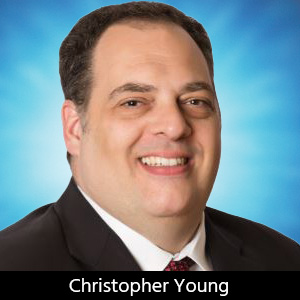
Engineers are accustomed to the demanding challenges of designing for miniaturization, cost reduction, cross platform compatibility, and harsh environments. What has proven to be the most painful experience of my career (and for many of my colleagues) is the sheer lack of components from which to build our designs. Development cycles—commercial, industrial, medical, avionics—have been severely impacted, from large enterprise corporations to small design/integration companies. Even as consultants, we have had a rough time. The good news is that design engineers tend to be tenacious in nature and this aids in finding ways to manage/mitigate difficult problems.
Awareness of the situation is the first step to understanding the underlying problems faced by today’s design engineers industry wide. Here are a few of the situations I have faced in the last year alone.
Long Lead Times
I experienced a product launch failure due to component unavailability. The client had a great idea, practical experience with the market, and identified a need which is not currently being served. What was needed was a compact, robust design that would fit the application—my bread and butter. I could not bring this product to fruition because of the lack of simple microcontrollers and peripheral devices. I was upfront with the customer that component availability was an issue and we needed to procure prototype and initial production materials early on, with the expectation that not all purchases may not be used in the design.
Several months into the development, I was notified that my orders were not only delayed but cancelled. Lead times for components previously on order now extended anywhere from 50 to 100 weeks, well beyond the needed date. PCBs already in hand, I then proceeded to delay/cancel my assembly orders and inform the customer that I could not produce a prototype, let alone a production-ready device to meet their launch window; the current status is in limbo.
Cost Increases
Massive product component cost increases due to the use of brokers to procure components have been a standard process of late as well. I have designs in production that doubled or tripled in cost due to a few hard-to-find ICs that were once considered plain, run-of-the-mill components. I typically avoid using brokers due to the increased level of scrutiny (cost) needed to ensure the components are indeed authentic, not reused/reclaimed parts, and undamaged. Typically, I would initiate a redesign to mitigate the unavailable component(s). In today’s barren component landscape, redesign has become second place to using a broker because of the risk of not being able to procure the replacement components.
Board Respins
The increased number of board respins I have performed lately has been troublesome and expensive. I have not been able to produce a design within the last year without having to perform a respin based on component unavailability. I now commonly hear from customers and colleagues that non-recurring engineering (NRE) cost is becoming more like recurring engineering (RE) cost. The sheer number of delivery cancellations and delays has caused me and many others to respin PCBs before they even hit the assembly line. In an attempt to stay positive, I will jokingly say, “These respins spin me right ‘round, like a record, right ‘round, ‘round, ‘round.”
To read this entire article, which appeared in the September 2022 issue of Design007 Magazine, click here.
Suggested Items
DownStream Acquisition Fits Siemens’ ‘Left-Shift’ Model
06/26/2025 | Andy Shaughnessy, I-Connect007I recently spoke to DownStream Technologies founder Joe Clark about the company’s acquisition by Siemens. We were later joined by A.J. Incorvaia, Siemens’ senior VP of electronic board systems. Joe discussed how he, Rick Almeida, and Ken Tepper launched the company in the months after 9/11 and how the acquisition came about. A.J. provides some background on the acquisition and explains why the companies’ tools are complementary.
Elementary Mr. Watson: Retro Routers vs. Modern Boards—The Silent Struggle on Your Screen
06/26/2025 | John Watson -- Column: Elementary, Mr. WatsonThere's a story about a young woman preparing a holiday ham. Before putting it in the pan, she cuts off the ends. When asked why, she shrugs and says, "That's how my mom always did it." She asks her mother, who gives the same answer. Eventually, the question reaches Grandma, who laughs and says, "Oh, I only cut the ends off because my pan was too small." This story is a powerful analogy for how many PCB designers approach routing today.
Connect the Dots: The Future of PCB Design and Manufacturing
07/02/2025 | Matt Stevenson -- Column: Connect the DotsFor some time, I have been discussing the increasing complexity of PCBs and how designers can address the constantly evolving design requirements associated with them. My book, "The Printed Circuit Designer’s Guide to… Designing for Reality," details best practices for creating manufacturable boards in a modern production environment.
Siemens Turbocharges Semiconductor and PCB Design Portfolio with Generative and Agentic AI
06/24/2025 | SiemensAt the 2025 Design Automation Conference, Siemens Digital Industries Software today unveiled its AI-enhanced toolset for the EDA design flow.
Cadence AI Autorouter May Transform the Landscape
06/19/2025 | Andy Shaughnessy, Design007 MagazinePatrick Davis, product management director with Cadence Design Systems, discusses advancements in autorouting technology, including AI. He emphasizes a holistic approach that enhances placement and power distribution before routing. He points out that younger engineers seem more likely to embrace autorouting, while the veteran designers are still wary of giving up too much control. Will AI help autorouters finally gain industry-wide acceptance?