-
- News
- Books
Featured Books
- pcb007 Magazine
Latest Issues
Current IssueInventing the Future with SEL
Two years after launching its state-of-the-art PCB facility, SEL shares lessons in vision, execution, and innovation, plus insights from industry icons and technology leaders shaping the future of PCB fabrication.
Sales: From Pitch to PO
From the first cold call to finally receiving that first purchase order, the July PCB007 Magazine breaks down some critical parts of the sales stack. To up your sales game, read on!
The Hole Truth: Via Integrity in an HDI World
From the drilled hole to registration across multiple sequential lamination cycles, to the quality of your copper plating, via reliability in an HDI world is becoming an ever-greater challenge. This month we look at “The Hole Truth,” from creating the “perfect” via to how you can assure via quality and reliability, the first time, every time.
- Articles
- Columns
- Links
- Media kit
||| MENU - pcb007 Magazine
Estimated reading time: 4 minutes
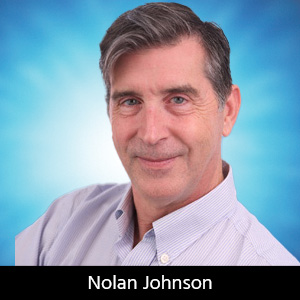
Nolan’s Notes: New Era Manufacturing
In a 2010 New York Times article titled “Failing Like a Buggy Whip Maker? Better Check Your Simile,” writer Randall Stross confronts the buggy whip analogy and unintentionally offers some perspective on our industry.
Stross tells of Daniel M.G. Raff, an associate professor at the Wharton School of the University of Pennsylvania, who once said the buggy whip analogy is “an obscurity sitting on an anachronism.” He says the buggy whip market was a fringe player in the overall carriage business to begin with as the bulk of the business centered on iron and wood fabrication.
So, where do we get this buggy whip trope? Turns out it originated with Theodore Levitt, a Harvard professor writing for the Harvard Business Review in 1960. In his article titled “Marketing Myopia,” Levitt posits that buggy whip manufacturers should have seen themselves as being in the personal transportation business rather than the buggy whip business, and that this change in thinking would have allowed them to survive. Stross says that Levitt blamed the buggy whip industry for having a lack of imagination.
In an interview with Thomas A. Kinney, an assistant professor at Bluefield College and researcher on the carriage industry, Stross learned there were 13,000 businesses in the carriage sector in 1890. Kinney told him, “The people who made the most successful transition were not the carriage makers, or the accessories makers (such as buggy whips) but the carriage parts makers.” Need an example? Timken Company, a manufacturer of roller bearings, originally made carriage bearings, hopped over to the car trade, and thrived in the automotive era.
While the carriage makers tried—with limited success—to transition into automobile manufacturing, the buggy whips simply “had no automotive analog,” Stross wrote.
He concluded, “When it came to adapting to the automotive era, businesses like axle and carriage lamp makers had the opportunity and succeeded. A similar mix of success and failure is unfolding today. Most camera makers, for example, have successfully switched to digital technology—no small feat. Those that don’t make it to the other side in the digital transition could reasonably be compared to carriage makers and carriage parts makers. But the buggy whip makers never had a fighting chance.”
This bit of history seems quite appropriate for our discussion this month. I’ve certainly heard the buggy whip analogy used to describe what’s happening in the U.S. PCB fabrication industry. However, it’s inaccurate. I believe it’s more about the thinking of the speaker than the PCB fabrication industry itself.
For example, PCB fabrication is thriving on a global scale. Innovations are occurring regularly, mostly in Asia. It’s not that the world has moved beyond needing printed circuits; the world is simply evolving its wants and needs from a circuit board fabricator. It makes sense that those who are leaning on the buggy whip analogy may have given up on the industry. Truth be told, however, we’re more like the carriage parts manufacturers than like the buggy whip makers.
Those companies who seize the opportunity to shift their skill set and expertise into the next new thing will survive and thrive.
What about upgrading a brownfield facility? At first blush, this thought would suggest a heavy concentration on the manufacturing floor details. Maybe a heavy dose of new capital equipment and line design topics. Well, not so much actually.In our September 2022 issue of PCB007 Magazine, the expert interview with Alex Stepinski makes the case for a specific set of duties by a chief technology officer (CTO), someone who is focused on more than technical details. The CTO’s role is to integrate sales demand, technical capabilities, and finance into a business case for advancing capabilities that follow the market. Don’t have a CTO? Someone on your staff likely is already fulfilling the role. However, are they doing everything they can to be successful? Alex’s important discussion will help draw the parallels between PCB fabrication and the coach parts industry even clearer: It’s the CTO who charts the course in this evolution.
To better understand what’s needed in upgrading our brownfield facilities, Michael Carano, part of the IPC Thought Leaders Program, shares insights on the industry and why upgrading capabilities are essential, while Dana Korf discusses developments in materials that will influence manufacturing processes.
I also want to draw your attention to some of our columnists: John Mitchell, president and CEO of IPC, sends a dispatch from India, and newcomers Paige Fiet and Christopher Bonsell share critical insights on both the big picture and improving your process.
I would especially like to mention our interview with Gerry Partida regarding his recent research on stacked microvia behavior and his further insight after presenting at IPC APEX EXPO 2022. He’s preparing a new paper for publication in 2023 on his findings and gives us a peek. Complementing this interview are Happy Holden’s column on Nano-Cu paste for microvias, and Michael Carano’s long-running column, where this month he discusses plating distribution and throwing power.
All these topics touch on the evolution of your existing facility into a new-era manufacturer of the kinds of components that customers are (or soon will be) demanding. We’re not an industry of on-the-fringe buggy whip makers; we’re central to the electronics industry. We’re more like the metalworkers who shifted from carriages to cars—and thrived.
This column originally appeared in the September 2022 issue of PCB007 Magazine.
More Columns from Nolan's Notes
Nolan’s Notes: The Interconnectedness of a Global Supply ChainNolan’s Notes: Finding Your Sweet Spot
Nolan’s Notes: Moving Forward With Confidence
Nolan's Notes: The Next Killer App in Component Manufacturing
Nolan’s Notes: Looking Deep Into the Future With X-ray
Nolan’s Notes: Your Golden Ticket
Nolan's Notes: Find the Help You Need—Accessing Technical Resources
Nolan’s Notes: Emerging Trends in 2025