-
-
News
News Highlights
- Books
Featured Books
- pcb007 Magazine
Latest Issues
Current IssueThe Hole Truth: Via Integrity in an HDI World
From the drilled hole to registration across multiple sequential lamination cycles, to the quality of your copper plating, via reliability in an HDI world is becoming an ever-greater challenge. This month we look at “The Hole Truth,” from creating the “perfect” via to how you can assure via quality and reliability, the first time, every time.
In Pursuit of Perfection: Defect Reduction
For bare PCB board fabrication, defect reduction is a critical aspect of a company's bottom line profitability. In this issue, we examine how imaging, etching, and plating processes can provide information and insight into reducing defects and increasing yields.
Voices of the Industry
We take the pulse of the PCB industry by sharing insights from leading fabricators and suppliers in this month's issue. We've gathered their thoughts on the new U.S. administration, spending, the war in Ukraine, and their most pressing needs. It’s an eye-opening and enlightening look behind the curtain.
- Articles
- Columns
- Links
- Media kit
||| MENU - pcb007 Magazine
A Focus on Process Control, Part 1
September 27, 2022 | I-Connect007 Editorial TeamEstimated reading time: 7 minutes
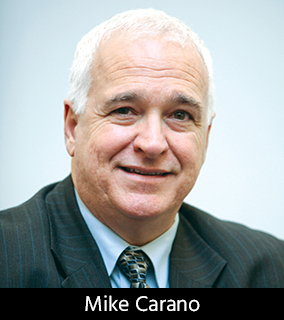
Michael Carano is a noted subject matter expert with respect to process control, electroplating and metallization technology, surface finishing, and reliability. So, it was only natural that we sat down to talk about mechanizing an existing facility given today’s fickle environment. Will any of the CHIPS funding trickle down to bare board fabrication? What process can be adjusted on the factory floor? The focus needs to be more than just on manufacturing and getting work out the door, he says, but also process control.
Nolan Johnson: You have a wide-ranging view of the current market, and how fabricators should approach advancing their capabilities. Walk us through your IPC Thought Leaders Program paper.
Michael Carano: To start, everyone is talking about the $52 billion CHIPS Act, but our folks in the PCB industry say, “Hey, that’s great, but chips don’t float. Where are the chips going to go?” Unless we build out PCB capacity as well, the chips will “float back” over the ocean into an OSAT or something like that. There’s no IC substrate capability here with any volume.
In my paper, I was asking about what it would take to double the capacity of existing fabrication by upgrading the equipment. It would be about $10 to $12 million per fabricator, with maybe 100 fabricators altogether—about $1.2 billion. Now if you include brick and mortar, then I would double that number to about $3.5 billion, then double again to a $7 billion market over a couple of years by making this investment, whether it comes from government, in-kind states, or whatever.
Upgrading of the opportunities would include horizontal equipment, new plating technologies, reliability, testing internally, materials handling, via formation, laser drilling, and more. I looked at all new equipment, state-of-the-art flying probe testing. That’s all included.
Now, if you just started with the greenfield, that might be more like a $25 to $40 million investment. But take our key five or six fabricators out there—such as TTM, Summit, APCT, FTG, Calumet—that have several fabrication sites under their ownership. They have quality people and engineering. If the DoD really wants to have some safety and security, then we need some help. There’s a way to do it that doesn’t even put a dent into that $52 billion.
Johnson: For the CHIPS Act, it’s about 2% of the funding.
Carano: Exactly. Let’s use that to get into the technology and what it will take to make this work. Our fabricators are capable and stable. They’re well managed, but in making that investment, they need some help to minimize or de-risk some of the investment they would have to make. I know they could do it and do it well.
The chemical processes keep evolving, materials keep getting better. When some say, “Look at what’s going on in Asia, the chemistry works so well.” Wait a minute, it’s the same chemistry, so it’s nothing secret; 90% of the chemistry in the world and materials were developed by U.S.-based companies. They may have facilities all over the world, but that technology is there. When someone tells me the plating technology doesn’t exist here, that’s not true.
Digital Factory
Barry Matties: Where does the digital factory come into your thinking for bare board fabricators? There seems to be a lot of reluctance, a “we’re small and that doesn’t work for us” mentality.
Carano: You hear about CFX and the Factory of the Future. The assembly companies see the machines, the need for them to be interconnected, how the data is transferred, basic monitoring, and even if there’s a glitch, how it can be repaired quickly.
Then there’s blockchain. What will that do for me? This is a big part of the security of any transaction, software development, or factory operation. They don’t see the connection, or the cost seems to be a concern. Furthermore, why aren’t we investing in more semi-additive or additive processing? Often the fabricator doesn’t see that CFX, digital factory, as a big move for them and as something that will enhance their position in this industry.
Johnson: Fabricators are having a hard time staffing the floor for their old processes.
Carano: Workforce development is extremely difficult across the board. I’m traveling here in California and help wanted signs are out all over in manufacturing places, not just in the circuit board industry. We’re not looking necessarily for PhDs or electrical engineers with master’s degrees. We’re trying to attract those who can do the job, want to be part of the CAD/CAM or drill operator teams; someone who can handle the chemistry and run the lines.
IPC is working very hard on workforce development by reaching out to students at the college and high school levels, getting them excited about electronics and what it can do. IPC has done a great job. We need more of that. Maybe all the fabricators and assemblers in California can combine efforts to share a common message, such as, “Here’s what this industry can really do, it’s a great career for you. You can advance. It’s exciting. What we do makes things that change and improve people’s lives.”
Rebuilding Margins
Matties: We’re already on thin margins and that’s a barrier for capital investment. How do we help those margins?
Carano: As we know, there was a shift to offshore technology about 20 years ago and it hasn’t really come back. Most don’t realize that almost $20 billion of the circuit board value that gets reported, though, is in things like iPads, mobile phones, smartphones, and other things that we wouldn’t make here anyway.
We’ve never really made cellphone boards here. However, this has evolved electronics overall. There’s a melding between semiconductor and circuit boards, a convergence in the United States and Canada. There are opportunities for focusing on higher margin processes because those are protected. We wouldn’t want those over in another country; we want them here. That’s the military, aerospace, medical, automotive, and internet infrastructure that can be done here. But I’ll ask fabricators, “What’s the issue for you?” They say it’s not so much about margins, but about yields. If they had higher yields, they would make more money. The problem is, though, how do you improve yields from 90 to 95%? That could be significant.
Much of it relates to workforce development, training, certification, equipment, instrumentation, and so forth. I’ve seen several fabricators that haven’t made upgrades in their equipment, some of them for many years, and you can’t go from 3-mil lines and spaces to 1- mil lines and spaces with an entry you had 20 years ago—it’s just not going to help you. If the investment can enhance the yields, then we have the opportunity to do more. But the other thing is that with the approximately 180 fabricator buildings in the country, maybe 90 of those have fewer than 50 employees.
If a large OEM walks in and says, “I like your work and what you do here. I need 10,000 pieces a week,” how will you help them? It will take up all your capacity. Your space is limited. That’s why, in my Thought Leaders paper, I suggested that doubling capacity would include hiring more workers. That can help us bring the industry back to what we had several years ago.
Let’s face it, the technology is much further advanced today than it was 15 or 20 years ago when the market started moving to Asia. The good news is we have this opportunity to stake out our position. We don’t have to want everything, but it can be IC substrates, high-end aerospace, defense, medical, safety, and security, that’s a big deal. Cybersecurity is at the forefront, and you have all these opportunities that would be protected-type industries. If you get the automotive companies behind it, along with the various software companies for security and then of course the military aerospace, we have an opportunity to rebuild this business here in North America.
Matties: Regarding yields, though, isn’t it the management’s discipline to process control that we already have? If we already have well-managed companies, but our processes are out of control, maybe there’s a lot of improvement for management discipline.
Carano: Oh, obviously. There are investments. One of the things I’ve shown folks over the years is I can completely automate the controls of a process, several lines, for less than $50,000. That includes controllers, online controllers, online monitoring, something as simple as a conductivity probe to measure the conductivity of the water when the rinsing is poor, and we got ionic contamination. Those little probes cost about $180. You carry them in your pocket, like a pen. You just check them. I don’t see a lot of that. The focus needs to be more than just on manufacturing and getting work out the door, but also process control.
I can’t tell you how many times I went to a facility, walked over to the electroless copper line, and then looked at the electroless copper controller. “Oh, that’s a nice controller, but it’s not hooked up or not running properly and it hasn’t been calibrated lately. Why do you have it if you’re not going to use it?” That’s where variation takes place, and when there’s variation, there’s a problem.
This conversation originally appeared in the September 2022 issue of PCB007 Magazine.
Suggested Items
The Evolution of Picosecond Laser Drilling
06/19/2025 | Marcy LaRont, PCB007 MagazineIs it hard to imagine a single laser pulse reduced not only from nanoseconds to picoseconds in its pulse duration, but even to femtoseconds? Well, buckle up because it seems we are there. In this interview, Dr. Stefan Rung, technical director of laser machines at Schmoll Maschinen GmbH, traces the technology trajectory of the laser drill from the CO2 laser to cutting-edge picosecond and hybrid laser drilling systems, highlighting the benefits and limitations of each method, and demonstrating how laser innovations are shaping the future of PCB fabrication.
Day 2: More Cutting-edge Insights at the EIPC Summer Conference
06/18/2025 | Pete Starkey, I-Connect007The European Institute for the PCB Community (EIPC) summer conference took place this year in Edinburgh, Scotland, June 3-4. This is the third of three articles on the conference. The other two cover Day 1’s sessions and the opening keynote speech. Below is a recap of the second day’s sessions.
Day 1: Cutting Edge Insights at the EIPC Summer Conference
06/17/2025 | Pete Starkey, I-Connect007The European Institute for the PCB Community (EIPC) Summer Conference took place this year in Edinburgh, Scotland, June 3-4. This is the second of three articles on the conference. The other two cover the keynote speeches and Day 2 of the technical conference. Below is a recap of the first day’s sessions.
Preventing Surface Prep Defects and Ensuring Reliability
06/10/2025 | Marcy LaRont, PCB007 MagazineIn printed circuit board (PCB) fabrication, surface preparation is a critical process that ensures strong adhesion, reliable plating, and long-term product performance. Without proper surface treatment, manufacturers may encounter defects such as delamination, poor solder mask adhesion, and plating failures. This article examines key surface preparation techniques, common defects resulting from improper processes, and real-world case studies that illustrate best practices.
RF PCB Design Tips and Tricks
05/08/2025 | Cherie Litson, EPTAC MIT CID/CID+There are many great books, videos, and information online about designing PCBs for RF circuits. A few of my favorite RF sources are Hans Rosenberg, Stephen Chavez, and Rick Hartley, but there are many more. These PCB design engineers have a very good perspective on what it takes to take an RF design from schematic concept to PCB layout.