-
- News
- Books
Featured Books
- pcb007 Magazine
Latest Issues
Current IssueInventing the Future with SEL
Two years after launching its state-of-the-art PCB facility, SEL shares lessons in vision, execution, and innovation, plus insights from industry icons and technology leaders shaping the future of PCB fabrication.
Sales: From Pitch to PO
From the first cold call to finally receiving that first purchase order, the July PCB007 Magazine breaks down some critical parts of the sales stack. To up your sales game, read on!
The Hole Truth: Via Integrity in an HDI World
From the drilled hole to registration across multiple sequential lamination cycles, to the quality of your copper plating, via reliability in an HDI world is becoming an ever-greater challenge. This month we look at “The Hole Truth,” from creating the “perfect” via to how you can assure via quality and reliability, the first time, every time.
- Articles
- Columns
- Links
- Media kit
||| MENU - pcb007 Magazine
Estimated reading time: 4 minutes
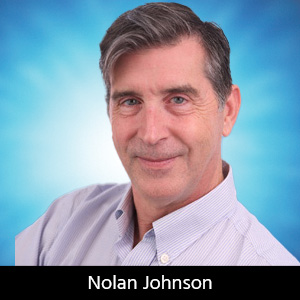
Nolan’s Notes: The Registration Sweet Spot
Registration is underrated and underappreciated. You can try to argue with me about this, but after diving into the current state of registration, I'm convinced. For example:
- 30 years ago, the state-of-the-art for integrated circuit geometries was in the low-double and high-single digits of microns, single-sided, on a consistently planar and highly polished crystalline substrate. Almost without exception, the entire integrated circuit was built on top of the substrate.
- Today, the bleeding edge of traditional PCB fabrication can reach into the 20-micron range, possibly multilayer, often still on epoxy-and-fiber substrate into which holes are drilled and metal plated; and it’s expected that features across multiple layers will match up across the entire stackup.
That’s asking a lot.
I am reminded of a scene in “From the Earth to The Moon” (Kinda want to get the boxed set, but is that still a thing?), an HBO series about the NASA space program of the 1960s. One particular episode opens with an aerospace engineer giving a presentation, standing next to an overhead projector. It went something like this:
“How hard is it to get a spaceship to the moon? Pretty hard. The ballistics are very complex; everything is moving. It’s like trying to throw a rock over a house, and hitting another rock you can’t see while it’s flying through the air. Oh, one more thing: You’re riding a bicycle.”
This engineer’s example certainly was evocative of that challenge. Every little detail needs to be right down the middle of its own “sweet spot” to accomplish the task; there is very little tolerance. Every single piece of that very complex process—launch, orbit, escaping orbit to go translunar, course corrections along the way, and braking exactly right to enter lunar orbit—needs very precise actions with an individual sweet spot. An error in the middle will only compound its way through the rest of the process.
In IC fabrication, in crystalline silicon, the IC engineers have the luxury of a remarkably stable foundation upon which to build in a highly regulated environment. Study the challenges in obtaining consistent, high-quality printed circuit registrations at today’s geometries, and it does start to feel like a moonshot. When the coefficient of thermal expansion in your substrate can be larger than the features you are fabricating, getting all of them to line up across multiple layers is an exercise in multiple moving targets. In the flex world, there may be fewer layers, but that doesn’t make it easier; some of the flex substrates are like plating on a sandwich bag. I digress (but only a little).
What’s key here is ensuring proper registration from layer to layer across the entire printed circuit board. It’s a holistic process requiring anticipation, prediction, precise attention at each step, and detailed data tracking and monitoring, because a slight error up front will only snowball as the process continues.
In this issue of PCB007 Magazine, we talk with some industry experts on getting it right with registration, with an overarching theme on how to keep all your steps in their respective sweet spots. Alex Stepinski shares his from-the-field lessons on how to design fabrication processes for improved registration, and some of his signature “hacks.” Happy Holden returns to the value of coupons, and XACTPCB’s Andrew Kelley discusses the use of planning software tools to anticipate misregistration and compensate. We also visit with Aidan Salvi at Amitron, a PCB fabricator committed to improving registration—to the tune of 60+ pieces of new equipment and development of a Factory 5.0 model.
Also in this issue, we bring you columns from Preeya Kuray, who interviews U.S. Rep. Blake Moore; Paige Fiet discussing technical terminology for newcomers; Henry Crandall continuing his look at wearable medical devices; Mike Konrad showcasing the innovative engineering programs at Dartmouth; and a PCBAA member profile on Hari Pillai.
By the time you finish this issue, you will likely notice that registration and process data are interrelated. Registration can only be as precise as your processes and the data you use to monitor those processes. Sensors, data warehousing, data analysis, and data-driven process control are central to improving registration. Just like the moonshot, precision is required at each step, even while all the components might be in motion.
I’d also like to welcome Marcy LaRont, who joins I-Connect007 as Managing Editor for PCB007 Magazine. If you’ve worked with Marcy in the past, you’ll be just as excited as we are to bring her expertise and professional experience to our editorial team.
This column originally appears in the November 2023 of PCB007 Magazine.
More Columns from Nolan's Notes
Nolan’s Notes: The Interconnectedness of a Global Supply ChainNolan’s Notes: Finding Your Sweet Spot
Nolan’s Notes: Moving Forward With Confidence
Nolan's Notes: The Next Killer App in Component Manufacturing
Nolan’s Notes: Looking Deep Into the Future With X-ray
Nolan’s Notes: Your Golden Ticket
Nolan's Notes: Find the Help You Need—Accessing Technical Resources
Nolan’s Notes: Emerging Trends in 2025