MHI Contributes to Successful Acquisition of First Observation Images by JAXA's "XRISM" X-ray Imaging and Spectroscopy Mission Satellite
February 9, 2024 | ACN NewswireEstimated reading time: 1 minute
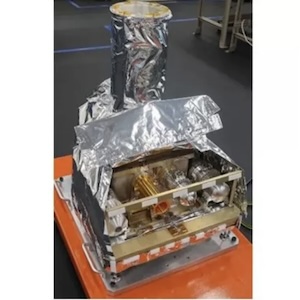
Mitsubishi Heavy Industries, Ltd. (MHI) made significant technological contributions to the first imagery acquisition conducted by the X-ray Imaging and Spectroscopy Mission (XRISM) Satellite announced by the Japan Aerospace Exploration Agency (JAXA) on January 5. MHI technology supported the data acquisition of the distribution and chemical composition of high-temperature plasma weaving through the galaxies by the XRISM satellite's onboard soft X-ray imager (Xtend) and soft X-ray spectrometer (Resolve). XRISM has been developed by JAXA.
XRISM's mission is to document, in unprecedented detail, the formation of stars, galaxies and galaxy clusters. MHI, which serves as manufacturer of the mission instruments, is responsible for designing and manufacturing Xtend's X-ray charge coupled devices (CCD) detector and the data processors for Xtend and Resolve. XRISM, together with JAXA's "Smart Lander for Investigating Moon" (SLIM), was launched from the Tanegashima Space Center in Kagoshima Prefecture on MHI's H-IIA Launch Vehicle No. 47 (H-IIA F47) on September 7, 2023.
Thanks to high-precision placement and assembly of the detector's four CCDs, Xtend's X-ray CCD camera array captured a wide viewing coverage in just a single observation. Previously, this would have required multiple X-ray observations. The mission data processors employed on both Xtend and Resolve are "SOI-SOC2" satellite-mounted microprocessor units (MPUs) jointly developed by JAXA and MHI. They provide outstanding reliability under space-unique environments through high radiation resistance capability while ensuring high-speed data processing.
MHI, with its rich experience and accumulated technological knowledge in developing sensors and electronic instrumentation for numerous scientific satellites, continues to make valuable contributions to diverse cosmic fields.
Suggested Items
RTX's Raytheon Awarded $646M Hardware Production and Sustainment Contract for SPY-6 Family of Radars
06/10/2025 | RTXRaytheon, an RTX business, was awarded a $646 million contract to continue producing AN/SPY-6(V) radars for the U.S. Navy. This is the fourth option exercised from the March 2022 hardware, production and sustainment contract that is valued up to $3 billion over five years.
Breaking Silos with Intelligence: Connectivity of Component-level Data Across the SMT Line
06/09/2025 | Dr. Eyal Weiss, CybordAs the complexity and demands of electronics manufacturing continue to rise, the smart factory is no longer a distant vision; it has become a necessity. While machine connectivity and line-level data integration have gained traction in recent years, one of the most overlooked opportunities lies in the component itself. Specifically, in the data captured just milliseconds before a component is placed onto the PCB, which often goes unexamined and is permanently lost once reflow begins.
RTX's Raytheon Awarded $536 Million US Navy Contract for SPY-6 Family of Radars
06/05/2025 | Raytheon CompanyRaytheon, an RTX business, has been awarded a $536 million contract from the U.S. Navy for the SPY-6 family of radars. The contract is a follow-on to the previously awarded Integration and Production Support contract and includes upgrading Flight IIA destroyers with the SPY-6(V)4 variant.
Driving Innovation: Traceability in PCB Production
05/29/2025 | Kurt Palmer -- Column: Driving InnovationTraceability across the entire printed circuit board production process is an increasingly important topic among established manufacturers and companies considering new PCB facilities. The reasons are apparent: Automatic loading of part programs, connection with MES systems and collection of production data, and compliance with Industry 4.0 requirements
Creative Electron Strengthens Leadership Team with Strategic Appointments in Marketing and SMT Business Unit
05/08/2025 | Creative ElectronCreative Electron, the largest U.S. manufacturer of X-ray inspection systems for the electronics industry, is proud to announce the addition of two seasoned leaders to its executive team: Wagner Lima as Marketing Director and Giancarlo De La Garza as SMT Business Unit Director.