-
- News
- Books
Featured Books
- pcb007 Magazine
Latest Issues
Current IssueInventing the Future with SEL
Two years after launching its state-of-the-art PCB facility, SEL shares lessons in vision, execution, and innovation, plus insights from industry icons and technology leaders shaping the future of PCB fabrication.
Sales: From Pitch to PO
From the first cold call to finally receiving that first purchase order, the July PCB007 Magazine breaks down some critical parts of the sales stack. To up your sales game, read on!
The Hole Truth: Via Integrity in an HDI World
From the drilled hole to registration across multiple sequential lamination cycles, to the quality of your copper plating, via reliability in an HDI world is becoming an ever-greater challenge. This month we look at “The Hole Truth,” from creating the “perfect” via to how you can assure via quality and reliability, the first time, every time.
- Articles
- Columns
- Links
- Media kit
||| MENU - pcb007 Magazine
Estimated reading time: Less than a minute
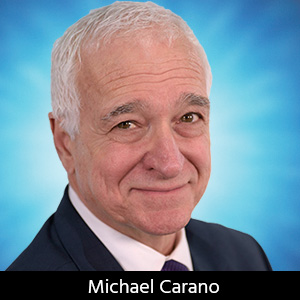
Contact Columnist Form
Trouble in your Tank: Optimizing the Liquid Photoimageable Soldermask Process, Part 1
Introduction
Some of my recent columns in have focused on identifying and resolving some very specific technical issues related to soldermask. It would be prudent at this time to present information on the soldermask process itself in hopes of preventing defects in the future. But first, one should understand the key requirements for the soldermask, in particular for today’s lead-free assembly requirements and fine-pitch circuitry.
The Requirements
Increased wiring density is driving soldermask performance to levels never seen before. Requirements to hold 2 and 3 mil dams are commonplace, especially with the increased use of HDI technology. In addition, PCB end-users are requiring the soldermask to display higher electrical and environmental properties as well as perform effectively with the myriad of lead-free solderable finishes (ENIG, Selective ENIG-OSP, ENEPIG, lead-free HASL, immersion silver and immersion tin).
Soldermask is applied after the surface traces are formed. The challenge for these materials is to impart electrical properties where, historically, soldermask was not part of electrical design. Soldermask attributes are shown in Table 1. (Source: IPC Technology Roadmap 2013)
Editor's Note: This article originally appeared in the May 2013 issue of The PCB Magazine.
More Columns from Trouble in Your Tank
Trouble in Your Tank: Minimizing Small-via Defects for High-reliability PCBsTrouble in Your Tank: Metallizing Flexible Circuit Materials—Mitigating Deposit Stress
Trouble in Your Tank: Can You Drill the Perfect Hole?
Trouble in Your Tank: Yield Improvement and Reliability
Trouble in Your Tank: Causes of Plating Voids, Pre-electroless Copper
Trouble in Your Tank: Organic Addition Agents in Electrolytic Copper Plating
Trouble in Your Tank: Interconnect Defect—The Three Degrees of Separation
Trouble in Your Tank: Things You Can Do for Better Wet Process Control