-
-
News
News Highlights
- Books
Featured Books
- pcb007 Magazine
Latest Issues
Current IssueThe Hole Truth: Via Integrity in an HDI World
From the drilled hole to registration across multiple sequential lamination cycles, to the quality of your copper plating, via reliability in an HDI world is becoming an ever-greater challenge. This month we look at “The Hole Truth,” from creating the “perfect” via to how you can assure via quality and reliability, the first time, every time.
In Pursuit of Perfection: Defect Reduction
For bare PCB board fabrication, defect reduction is a critical aspect of a company's bottom line profitability. In this issue, we examine how imaging, etching, and plating processes can provide information and insight into reducing defects and increasing yields.
Voices of the Industry
We take the pulse of the PCB industry by sharing insights from leading fabricators and suppliers in this month's issue. We've gathered their thoughts on the new U.S. administration, spending, the war in Ukraine, and their most pressing needs. It’s an eye-opening and enlightening look behind the curtain.
- Articles
- Columns
- Links
- Media kit
||| MENU - pcb007 Magazine
A Conversation (and Day) with Joe Fjelstad, Part 5
May 8, 2015 | Barry Matties, I-Connect007Estimated reading time: 10 minutes
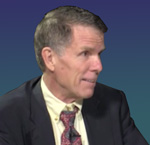
Our five-part interview series with Verdant Electronics Founder Joe Fjelstad wraps up with a look back at the point when Fjelstad’s career began focusing on circuit board technology, and he details his patented Occam process, and why this game-changing, disruptive technology has yet to become standard practice in the industry. Also explained: Why Fjelstad has been referred to as an “iconoclastic polemicist,” and how a Native American story he heard long ago has resonated throughout his career and life.
Matties: You started in circuit boards in what year?
Fjelstad: I started in 1971, and I would say that if I had been tele-transported from that time to today, and somebody toured me through a circuit board shop, I would certainly be impressed with the manufacturing tools, feature sizes and density and the rest of it, but I believe I would know how to do everything required to make a PCB. In other words, nothing much has changed.
Matties: The product is still the same and it’s still the same basic steps.
Fjelstad: As I said, it’s just the feature sizes that have changed: more layers, finer features, and that's it. Well maybe some improved materials, also. But in terms of the end-product, it is the same; the same fundamental materials—epoxy glass or resin glass; the same base, interconnected material— copper; the same means of connecting it—vias. Feature sizes are smaller, and layer counts are up, and the components are smaller, but we are still doing it with solder. Surface mount came on afterward, although surface mount was the original technology. The thing that we did start to do in earnest in the last seven years was the idea of putting in embedded resistors and capacitors. That goes back to the '70s. Some of today’s embedding technologies to structure that are being done in the multi-chip modules, people were doing in the early '90s and the like.
A few years back, I met with the then-president of a household name Japanese electronics company at his invitation, just shortly after Occam kicked off. He said to me, "We're doing these kinds of things now." He handed me something and said, "You see this right here? This is a wafer level package and you can see it right here through the back and we've got a connection." I said, “That's awesome, this is the kind of stuff that we need because this is the right answer going forward. But tell me, what are all these silver balls?" He laughed and he said, "Yes, you're right.” I said, “You need to get rid of the silver balls.” Get rid of the solder. When you look at the height of a component, half the height of component is the solder ball. You want to make things thinner?
If you read The Long Tail by Christian Anderson, editor of Wired magazine, the last chapter is fundamentally saying that, at some point in time in the future, we'll no longer be shipping atoms. We'll be shipping electrons, and that's what we're doing. That's what electronic media is and what a 3D printer is. You have the materials that bring it to fruition and it's not all that different from the Jetsons. You can actually print food today, but I am not sure how tasty it is.
People are saying they can do printed electronics when all they are doing is printing conductive ink. I don't want to dismiss that; I’m just saying that I am old and I have seen a lot of the stuff that people are trotting out, saying it’s new when it's not new. It's old…like me. I have to keep on going back and tipping my hat to the idea of embedding capacitors and embedding resistors. It goes back to the '70s. The idea of embedding more active things goes back to the '80s, at chip level. The fundamental thing that I'm saying is, get rid of solder. That is the game.
Matties: That's the Achilles heel.
Fjelstad: When you get rid of solder, you get rid of the Achilles heel of electronics, in terms of its reliability. Depending on the bill of materials and the complexity of the structure, you knock out anywhere from 5–30% of the cost.
Matties: It's interesting because we were looking at some of our survey results recently and solder alternatives were a very high area of interest for people.
Fjelstad: And it should be. I'm saying not just solder alternatives but the elimination of it, because it can be done, and it can be done with existing technologies. When I was at Tessera, we were developing the micro-BGA for the market, a product which, by the way, was designed to make solder joints more reliable, and at the time we were asking people to go out and develop new materials, new processing equipment, new design tools, etc. We were asking them to do all this stuff and fortunately, the objective resonated with industry: the idea of being able to get a chip-sized package without having to deal with a chip. So they bought in. What made it all work at the end of the day were standards.
Standards are, as I learned during my time on staff at IPC in the early 1980s, vital to industry success. I ultimately came to see industry standards as a glue of sorts that help to hold industries together. It's the same kind of standards thing that plays with Occam. It can work to a point, but it can't work to its best point if you don’t have standards. In other words, in the case of Occam, if you lock in on that standard fundamental grid pitch idea and you build standard base outline and contact feature components with that fundamental grid pitch, boom: it's game, set, and match. It just works.
People have thought on similar lines at the University of Washington and I think the University of Michigan, but their term for it was ‘brick and mortar.’ They want to do it at a chip level and they'll build independent functional blocks.
Page 1 of 2
Suggested Items
Driving Innovation: Direct Imaging vs. Conventional Exposure
07/01/2025 | Simon Khesin -- Column: Driving InnovationMy first camera used Kodak film. I even experimented with developing photos in the bathroom, though I usually dropped the film off at a Kodak center and received the prints two weeks later, only to discover that some images were out of focus or poorly framed. Today, every smartphone contains a high-quality camera capable of producing stunning images instantly.
Hands-On Demos Now Available for Apollo Seiko’s EF and AF Selective Soldering Lines
06/30/2025 | Apollo SeikoApollo Seiko, a leading innovator in soldering technology, is excited to spotlight its expanded lineup of EF and AF Series Selective Soldering Systems, now available for live demonstrations in its newly dedicated demo room.
Indium Corporation Expert to Present on Automotive and Industrial Solder Bonding Solutions at Global Electronics Association Workshop
06/26/2025 | IndiumIndium Corporation Principal Engineer, Advanced Materials, Andy Mackie, Ph.D., MSc, will deliver a technical presentation on innovative solder bonding solutions for automotive and industrial applications at the Global Electronics A
Fresh PCB Concepts: Assembly Challenges with Micro Components and Standard Solder Mask Practices
06/26/2025 | Team NCAB -- Column: Fresh PCB ConceptsMicro components have redefined what is possible in PCB design. With package sizes like 01005 and 0201 becoming more common in high-density layouts, designers are now expected to pack more performance into smaller spaces than ever before. While these advancements support miniaturization and functionality, they introduce new assembly challenges, particularly with traditional solder mask and legend application processes.
Knocking Down the Bone Pile: Tin Whisker Mitigation in Aerospace Applications, Part 3
06/25/2025 | Nash Bell -- Column: Knocking Down the Bone PileTin whiskers are slender, hair-like metallic growths that can develop on the surface of tin-plated electronic components. Typically measuring a few micrometers in diameter and growing several millimeters in length, they form through an electrochemical process influenced by environmental factors such as temperature variations, mechanical or compressive stress, and the aging of solder alloys.