-
-
News
News Highlights
- Books
Featured Books
- pcb007 Magazine
Latest Issues
Current IssueThe Hole Truth: Via Integrity in an HDI World
From the drilled hole to registration across multiple sequential lamination cycles, to the quality of your copper plating, via reliability in an HDI world is becoming an ever-greater challenge. This month we look at “The Hole Truth,” from creating the “perfect” via to how you can assure via quality and reliability, the first time, every time.
In Pursuit of Perfection: Defect Reduction
For bare PCB board fabrication, defect reduction is a critical aspect of a company's bottom line profitability. In this issue, we examine how imaging, etching, and plating processes can provide information and insight into reducing defects and increasing yields.
Voices of the Industry
We take the pulse of the PCB industry by sharing insights from leading fabricators and suppliers in this month's issue. We've gathered their thoughts on the new U.S. administration, spending, the war in Ukraine, and their most pressing needs. It’s an eye-opening and enlightening look behind the curtain.
- Articles
- Columns
- Links
- Media kit
||| MENU - pcb007 Magazine
Insulectro, Oak-Mitsui, and CAC Create Landmark Partnership
June 22, 2015 | InsulectroEstimated reading time: 4 minutes
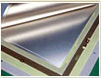
Insulectro, a leading supplier of materials for use in the PCB and printed electronics industries, announced a breakthrough partnership to supply world-class performance copper foils manufactured by Oak-Mitsui throughout North America.
Beginning in July, Insulectro will provide copper foil manufactured by Oak-Mitsui for the PCB outer-layer market requirements. This strategic move will provide long-term sustainable domestic foil to PCB fabrication customers.
In addition, CAC, Inc. will now manufacture its CAC (Copper-Aluminum- Copper) bonded product with Oak-Mitsui copper Foil. CAC products will continue to be distributed through its global distribution partners, including Insulectro.
“I am proud to announce the addition of Oak-Mitsui copper foil to the Insulectro family of high performance materials. Oak-Mitsui is a globally recognized leader in copper foils to the electronics industry and this partnership provides our customers domestically produced products with a more reliable supply chain,” announced Insulectro CEO Tim Redfern. “We will offer Oak-Mitsui’s entire copper product portfolio – from very thin foils to specialty treatments – for today’s challenging adhesion applications. I’m sure our customers will appreciate the net effect of this deal – we’re bringing the highest quality copper to our customers utilizing our US network of ten stocking locations.”
Ken Parent, VP of Sales for Insulectro stated, “The addition of these high performance HTE foils to our line card is very exciting. It significantly enhances our product offering to customers needing adhesion, thin foil or thermally reliable copper.
The foils’ very low profile makes it perfect for thin dielectrics and fine-line applications. It’s natural that Oak-Mitsui copper foils would be a good fit with Insulectro. OakMitsui is well known and highly respected throughout the PCB marketplace. In addition to strong brand identity and market leader, they are known for their high quality, madein-America products.
John Fatcheric, Oak-Mitsui COO said, “This partnership with Insulectro strengthens our ability to supply and service the US PCB market. Oak-Mitsui is committed to maintaining a US manufacturing base and supplying the highest quality copper foil products to meet today’s and tomorrow’s PCB requirements.”
CAC Inc. President Patrick Redfern commented, “We are excited to integrate the Oak-Mitsui materials into our bonded CAC products. While copper supply has recently been inconsistent and over dependent on copper from foreign sources, our efforts together with Oak and Insulectro will help to stabilize the supply chain and directly benefit our customers with American products that are stocked geographically throughout the United States.”
Oak-Mitsui was incorporated in 1976 between Oak industries, Mitsui Mining and Smelting of Japan, and Anaconda. It was one of only three major companies in the United States manufacturing ultrathin copper foil for the printed circuit business. Over the years, the business has grown to become a leader in the supply of copper foil for the printed circuit board business in the U.S. Today, Oak-Mitsui is a wholly owned subsidiary of Mitsui Kinzoku, the world leader in electrodeposited copper foil and is the only electrodeposited copper foil manufacturer in the US & North America.
John Blaber, Senior VP of Sales & Marketing at Oak-Mitsui commented “The addition of Insulectro to our supply team gives PCB customers new options for copper foil products. We are excited about the new opportunities this new relationship offers. Both Oak-Mitsui and Insulectro are committed to the supply and support of US made products.”
“Fabricators can expect to see Oak-Mitsui™ copper foils in our inventory by July 1, 2015. Over the next three months, we will be transitioning our existing copper foil customers to Oak-Mitsui product as well as welcoming new customers to the Insulectro family,” Parent concluded.
About Insulectro
Insulectro (www.insulectro.com) is the leading supplier of PCB and printed electronics materials used to manufacture circuit boards. Insulectro combines its premier product offering with local inventory in 10 strategic stocking locations across the country, fabrication capabilities and backed up by expert customer and technical support services. Insulectro supplies advanced engineered materials manufactured by DuPont®, Isola, LCOA®, CAC, Inc., Ormet Circuits, Pacothane, Circuit Foil, and Focus Tech. These products are used by our customers to fabricate complex, multilayer circuit boards.
Insulectro serves a broad customer base manufacturing rigid, rigid/flex and flexible circuit boards for applications in a variety of end markets including telecom, data communications, high speed computing, mobile devices, military, and medical.
About Oak-Mitsui
Oak-Mitsui is recognized as the technological leader in the manufacture of high-quality electrodeposited copper foils for the printed circuit board industry. With the strength of international scope, Oak-Mitsui produces both conventional cladding and application specific copper foils required by technology's leading edge companies. At Oak-Mitsui, copper foils are electroformed on revolving titanium drums, unique for the ability to deposit copper foils with a high-quality surface. Electroformed foils are then subjected to a variety of surface treating operations contingent upon end-use requirements. During treating, copper dendrites are deposited onto the foil surface to enhance bonding to B-staged resins upon lamination. A "barrier-layer" is deposited for promoting reliability in thermal applications, specific proprietary organic layers are applied to promote chemical adhesion, and foils are stain-proofed to prevent oxidation in shipping, storage, lamination and post-bake cycles.
About CAC, Inc.
CAC, Inc. is a manufacturer of CAC® (Copper Aluminum Copper). Its licensed and patented products feature copper foil attached in its state-of-the-art clean room to one or both sides of an aluminum separator sheet based on the PCB application. CAC provides superior surface quality, important to producers of increasingly high technology printed circuit boards as well as offering labor and material cost savings. CAC’s proprietary process ensures particle and dent-free copper surfaces. It is the best and most economical solution for using difficult to handle thin foils, reverse treated and double treated copper foils.
Suggested Items
The Evolution of Picosecond Laser Drilling
06/19/2025 | Marcy LaRont, PCB007 MagazineIs it hard to imagine a single laser pulse reduced not only from nanoseconds to picoseconds in its pulse duration, but even to femtoseconds? Well, buckle up because it seems we are there. In this interview, Dr. Stefan Rung, technical director of laser machines at Schmoll Maschinen GmbH, traces the technology trajectory of the laser drill from the CO2 laser to cutting-edge picosecond and hybrid laser drilling systems, highlighting the benefits and limitations of each method, and demonstrating how laser innovations are shaping the future of PCB fabrication.
Day 2: More Cutting-edge Insights at the EIPC Summer Conference
06/18/2025 | Pete Starkey, I-Connect007The European Institute for the PCB Community (EIPC) summer conference took place this year in Edinburgh, Scotland, June 3-4. This is the third of three articles on the conference. The other two cover Day 1’s sessions and the opening keynote speech. Below is a recap of the second day’s sessions.
Day 1: Cutting Edge Insights at the EIPC Summer Conference
06/17/2025 | Pete Starkey, I-Connect007The European Institute for the PCB Community (EIPC) Summer Conference took place this year in Edinburgh, Scotland, June 3-4. This is the second of three articles on the conference. The other two cover the keynote speeches and Day 2 of the technical conference. Below is a recap of the first day’s sessions.
Preventing Surface Prep Defects and Ensuring Reliability
06/10/2025 | Marcy LaRont, PCB007 MagazineIn printed circuit board (PCB) fabrication, surface preparation is a critical process that ensures strong adhesion, reliable plating, and long-term product performance. Without proper surface treatment, manufacturers may encounter defects such as delamination, poor solder mask adhesion, and plating failures. This article examines key surface preparation techniques, common defects resulting from improper processes, and real-world case studies that illustrate best practices.
RF PCB Design Tips and Tricks
05/08/2025 | Cherie Litson, EPTAC MIT CID/CID+There are many great books, videos, and information online about designing PCBs for RF circuits. A few of my favorite RF sources are Hans Rosenberg, Stephen Chavez, and Rick Hartley, but there are many more. These PCB design engineers have a very good perspective on what it takes to take an RF design from schematic concept to PCB layout.