-
- News
- Books
Featured Books
- pcb007 Magazine
Latest Issues
Current IssueInventing the Future with SEL
Two years after launching its state-of-the-art PCB facility, SEL shares lessons in vision, execution, and innovation, plus insights from industry icons and technology leaders shaping the future of PCB fabrication.
Sales: From Pitch to PO
From the first cold call to finally receiving that first purchase order, the July PCB007 Magazine breaks down some critical parts of the sales stack. To up your sales game, read on!
The Hole Truth: Via Integrity in an HDI World
From the drilled hole to registration across multiple sequential lamination cycles, to the quality of your copper plating, via reliability in an HDI world is becoming an ever-greater challenge. This month we look at “The Hole Truth,” from creating the “perfect” via to how you can assure via quality and reliability, the first time, every time.
- Articles
- Columns
- Links
- Media kit
||| MENU - pcb007 Magazine
Stepping Up To Laser Processing for Flex, Part 1: Opportunities and Implications
October 8, 2015 | Mike Jennings and Patrick Riechel, ESIEstimated reading time: 3 minutes
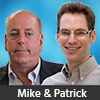
This six-part series will examine how to effectively supplement your flex production capabilities with laser processing.
Market demand for smaller, faster, wearable, lighter and more powerful devices continues to keep PCB manufacturers scrambling to keep up as they evolve and adapt their manufacturing capabilities to meet changing customer needs. But keeping up with the dizzying pace of change in the world of PCB manufacturing need not be a daunting task. Employing laser technology is one of the best ways to stay current, as it enables printed circuit manufacturers to achieve manufacturing flexibility and agility, with more accurate and/or smaller features than is possible with traditional processes.
As highlighted in Figure 1, there are several steps in the flexible circuit manufacturing process where laser processing can play a significant role. In this series, we will focus on the laser micromachining processes related to drilling, coverlay cutting and circuit singulation using general laser micromachining systems. Keep in mind that, although this series deals primarily with flex, many of same laser processing principles discussed also apply to rigid boards—and even to LDI.
Figure 1: The role of laser technology in the flex processing manufacturing flow.
When is the Right Time to Adopt Laser Micromachining?
Printed circuit manufacturers typically invest in laser micromachining systems when current mechanical processing capabilities can no longer address the processing accuracy and quality dictated by size constraints and newer materials. Mechanical punching, routing, and drilling are either no longer feasible or simply not a cost-effective solution due to many of the following issues:
- Features become too small or too complex for drill/routing bit diameters and/or die punch manufacturing capabilities
- Trace width/spacing requirements require via pads to shrink beyond mechanical drilling registration capabilities
- Part tolerances require machining accuracies beyond mechanical processing capabilities
- The number of vias per panel increases sufficiently to make mechanical drilling less cost effective than laser drilling.
- Customer demand includes blind via processing in thin flex material beyond the depth control capabilities of mechanical drills.
- High product mix and/or fast turnaround time requirements become incompatible with the long lead times and expense associated with fabricating dies for coverlay cutting and circuit singulation
If some of these issues sound familiar, it’s probably time to consider laser processing. But before launching into that endeavor, take the time to learn about the opportunities and implications associated with laser processing. It can pay big dividends, but to get optimal results there are some approaches and best practices that you should be aware of.
About This Series
In each future installment of the Stepping up to Laser Processing for Flex series, we will arm you with information you need to investigate the advantages of FPC laser processing and the role it can play in optimizing your processing capabilities. Upcoming installments will cover the following:
- Calculating and Optimizing Production
How do you calculate and optimize total system cost of ownership and cost per panel? We will provide an overview of the high-impact profitability factors in choosing and running your system.
- Readiness and Site Preparation
How do you ensure that your facilities are ready for the introduction of laser processing? Find strategies for addressing shop floor concerns such as HVAC, temperature control, debris removal capabilities, power requirements and more.
- Installation, Training, and Initial Operation
How do you get your new system installed and processing those first runs? We will cover installation best practices, system verification testing, training and safety.
- Process Development
How do you develop your process library? Learn several best practices, tips and tricks for typical flexible circuit laser processes.
- Maintenance and Servicing
How do you minimize system maintenance and repair costs while prolonging its useful life? We’ll examine best practices and considerations related to the “care and feeding” of your laser processing machine.
Mike Jennings is director of product marketing with ESI’s Industrial Products Division.
Patrick Riechel is product manager for ESI’s flexible circuit micromachining tools.
Testimonial
"In a year when every marketing dollar mattered, I chose to keep I-Connect007 in our 2025 plan. Their commitment to high-quality, insightful content aligns with Koh Young’s values and helps readers navigate a changing industry. "
Brent Fischthal - Koh YoungSuggested Items
VVDN Expands Manufacturing Footprint into the UAE to Meet Global Demand
08/20/2025 | PRNewswireVVDN Technologies, a global provider of software, product engineering and electronics manufacturing services & solutions, today announced it is setting up a new manufacturing facility in the UAE as part of its global expansion strategy.
Haylo Labs Acquires Plessey Semiconductors
08/20/2025 | Haylo LabsHaylo Labs has acquired Plessey Semiconductors, the UK’s leading innovator in microLED display technology.
Kimball Electronics Veterans ERG Members Proudly Participate in the 5th Annual Honor and Remember Run
08/20/2025 | Kimball ElectronicsVeterans and Military Service Advocacy (VMSA) Employee Resource Group (ERG) members Michael Mosher (Database Administration Engineer), Michael Stone (Test Technician Team Lead), and Joshua Belcher (Application Development Manager) took part in the 5th Annual Honor & Remember Run, a meaningful event dedicated to honoring fallen service members. The race featured a powerful memorial wall constructed from dog tags.
Meet Incap UK at the Electronic Component Show 2025
08/20/2025 | IncapIncap UK is pleased to be exhibiting at the Electronic Component Show 2025. This one-day event will take place on 18 September at the Kassam Stadium in Oxford, bringing together design engineers, purchasing professionals, manufacturers, distributors, and service providers to discover new products, solutions, and contacts. You will find us at stand 52.
Hon Hai Rotating CEO Yang Qiujin Wins 2025 Golden Yang Award for Women’s Power in Technology
08/20/2025 | Hon Hai Precision Industry Co., Ltd.Amid the global rise of "female-powered technology," Yang Qiujin, Rotating CEO of Hon Hai Precision Industry Co., Ltd. (TWSE: 2317), the world's largest platform solutions provider, has been awarded the "2025 Golden Yang Award - Female-Powered Technology" by the China Software Association/China Software Industry Association.