-
- News
- Books
Featured Books
- pcb007 Magazine
Latest Issues
Current IssueInventing the Future with SEL
Two years after launching its state-of-the-art PCB facility, SEL shares lessons in vision, execution, and innovation, plus insights from industry icons and technology leaders shaping the future of PCB fabrication.
Sales: From Pitch to PO
From the first cold call to finally receiving that first purchase order, the July PCB007 Magazine breaks down some critical parts of the sales stack. To up your sales game, read on!
The Hole Truth: Via Integrity in an HDI World
From the drilled hole to registration across multiple sequential lamination cycles, to the quality of your copper plating, via reliability in an HDI world is becoming an ever-greater challenge. This month we look at “The Hole Truth,” from creating the “perfect” via to how you can assure via quality and reliability, the first time, every time.
- Articles
- Columns
- Links
- Media kit
||| MENU - pcb007 Magazine
Testing Flexible Circuits, Part 3: The Completed Flex Circuit
October 15, 2015 | Dave Becker, All FlexEstimated reading time: 2 minutes
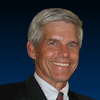
This is the final article in a three-part series relating to testing a flexible circuit. In the first column we cited IPC-6013, “Qualification and Performance Specification of Flexible Printed Boards,” as a comprehensive specification widely accepted in the industry. Many of the tests discussed in this article are outlined in that document.
Most flex houses perform a variety of tests on completed flexible circuits. The type, frequency, and complexity of these tests vary with customer and application. Test requirements are generally defined by the customer, but input is often solicited from the supplier during the quote process.
Production Testing
Most production tests are non-destructive and performed as part of the fabrication or assembly process. Many flex circuit fabricators also perform 100% inspection on final bare circuits. Testing may be done as an automated machine optical inspection (AOI) or as an electrical test. Normal electrical testing generally verifies parts are free of opens and/or shorts, but in some cases high voltage or current may be specified. AOI is recognized as an acceptable substitute (vs. electrical test) for single- and double-sided circuits. AOI can be done by programming a set of “rules” such as minimum trace width and apply that to the circuit pattern.
Destructive testing is used to examine copper thickness thru cross sections of plated thru holes. Porosity of gold plating is another verification also done as a destructive test.
Unique customer requirements can result in a variety of strategies for testing fully assembled product. This may include “in circuit” component testing, or in some cases full or partial functional testing. Machine optical inspection may also be done 100% with sophisticated equipment to examine for orientation and presence of components.
Other production testing involves surface cleanliness. Ionic and surface organic contamination tests are specified in IPC-TM-650. These tests are fairly common for medical and aerospace applications.
Reliability or Performance Testing
While production testing will verify form, fit and function, other tests are used to assess the product reliability. These tests tend to involve environmentally stressing the part and can partially destroy or degrade the tested circuit. They also can be fairly expensive and time consuming.
The following are common reliability tests:
- Long-term humidity aging
- High-temperature stress
- Salt–sulfur fog exposure
- Thermal cycling (with or without current)
- Flammability testing (UL)
- Chemical immersion
The specific parameters of each test depend on the application and customer. Application engineers work with the customer to jointly determine the exact test parameters, balancing cost with product robustness requirements. A specific performance test can be as short as a few seconds or require weeks to complete. When and how frequently reliability tests are performed is mutually determined by both the customer and the supplier. The following are typical:
- One-time testing done as part of the design qualification
- Testing performed on a set time schedule such as weekly, monthly or quarterly
- Testing done on a sample from each lot
- Testing based on production frequency such as every 10th lot, etc.
Many fabricators have resident capability to perform the life cycle testing required by customers, either with an in-house test facility or by outsourcing with an independent test lab.
Fabricators focusing on a specific product niche often develop a large data base of results covering a variety of performance tests. For many applications, previous test results can be a starting point for discussions in determining what tests are needed on a new part number.
Dave Becker is vice president of sales and marketing at All Flex Flexible Circuits LLC.
Testimonial
"In a year when every marketing dollar mattered, I chose to keep I-Connect007 in our 2025 plan. Their commitment to high-quality, insightful content aligns with Koh Young’s values and helps readers navigate a changing industry. "
Brent Fischthal - Koh YoungSuggested Items
How Good Design Enables Sustainable PCBs
08/21/2025 | Gerry Partida, Summit InterconnectSustainability has become a key focus for PCB companies seeking to reduce waste, conserve energy, and optimize resources. While many discussions on sustainability center around materials or energy-efficient processes, PCB design is an often overlooked factor that lies at the heart of manufacturing. Good design practices, especially those based on established IPC standards, play a central role in enabling sustainable PCB production. By ensuring designs are manufacturable and reliable, engineers can significantly reduce the environmental impact of their products.
50% Copper Tariffs, 100% Chip Uncertainty, and a Truce
08/19/2025 | Andy Shaughnessy, I-Connect007If you’re like me, tariffs were not on your radar screen until a few months ago, but now political rhetoric has turned to presidential action. Tariffs are front-page news with major developments coming directly from the Oval Office. These are not typical times. President Donald Trump campaigned on tariff reform, and he’s now busy revamping America’s tariff policy.
Global PCB Connections: Understanding the General Fabrication Process—A Designer’s Hidden Advantage
08/14/2025 | Markus Voeltz -- Column: Global PCB ConnectionsDesigners don’t need to become fabricators, but understanding the basics of PCB fabrication can save you time, money, and frustration. The more you understand what’s happening on the shop floor, the better you’ll be able to prevent downstream issues. As you move into more advanced designs like HDI, flex circuits, stacked vias, and embedded components, this foundational knowledge becomes even more critical. Remember: the fabricator is your partner.
MKS’ Atotech to Participate in IPCA Electronics Expo 2025
08/11/2025 | AtotechMKS Inc., a global provider of enabling technologies that transform our world, announced that its strategic brands ESI® (laser systems) and Atotech® (process chemicals, equipment, software, and services) will showcase their latest range of leading manufacturing solutions for printed circuit board (PCB) and package substrate manufacturing at the upcoming 17th IPCA Show to be held at Pragati Maidan, New Delhi from August 21-23, 2025.
MKS Showcases Next-generation PCB Manufacturing Solutions at the Thailand Electronics Circuit Asia 2025
08/06/2025 | MKS Instruments, Inc.MKS Inc, a global provider of enabling technologies that transform our world, today announced its participation in Thailand Electronics Circuit Asia 2025 (THECA 2025), taking place August 20–22 at BITEC in Bangkok.