-
- News
- Books
Featured Books
- pcb007 Magazine
Latest Issues
Current IssueInventing the Future with SEL
Two years after launching its state-of-the-art PCB facility, SEL shares lessons in vision, execution, and innovation, plus insights from industry icons and technology leaders shaping the future of PCB fabrication.
Sales: From Pitch to PO
From the first cold call to finally receiving that first purchase order, the July PCB007 Magazine breaks down some critical parts of the sales stack. To up your sales game, read on!
The Hole Truth: Via Integrity in an HDI World
From the drilled hole to registration across multiple sequential lamination cycles, to the quality of your copper plating, via reliability in an HDI world is becoming an ever-greater challenge. This month we look at “The Hole Truth,” from creating the “perfect” via to how you can assure via quality and reliability, the first time, every time.
- Articles
- Columns
- Links
- Media kit
||| MENU - pcb007 Magazine
All About Flex: Embracing the Mess
December 3, 2015 | Dave Becker, All FlexEstimated reading time: 5 minutes
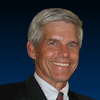
Marketing in the world of printed circuits is an important discipline, but I have learned it is better to be prepared with a nimble reaction than to expect the marketing department to consistently be successful in predicting the future. The path to the goal is often achieved much more quickly by making an early decision followed by a course correction rather than waiting for all the information. Several related factoids characterize the markets for flexible circuits and flexible heaters:
- We live in a world of “time based competition.” Being faster to market can be more profitable than being better.
- Customers’ needs many times don’t fit within the supplier’s existing/proven/Six-Sigma capabilities.
- Technology and markets move quickly, rewarding suppliers that respond rapidly.
- Customers give suppliers money to figure things out.
The myriad of electronic applications drive flexible circuit product configurations and constructions spanning broad engineering imaginations. Circuits that require controlled impedance push trace widths down, and copper thicknesses increasingly thinner, with .0007” copper a common specification. These applications also tend to drive film substrates thicker to increase separation distance between signals and ground planes. Circuitry intended to carry heavy current pushes copper the opposite direction, sometimes involving metal thicknesses in excess of .010”. These circuits tend to stretch the definition of the word flexible
Product configuration selections can also involve adding copper layers to make multilayer structures, plating multiple surface treatments for solder pads vs. switch contact regions, attaching selective stiffeners for mechanical and component support, and orientation of copper grain to properly orient circuit traces in applications requiring dynamic flexing. Requirements for optimizing component attachment create an additional complexity dimension as nesting circuits for material usage competes with assembly panelization requirements. These seemingly endless permutations of “want to have” vs. “need to have” requirements can drive mushrooming product features, untested manufacturing processes, and unique routing sequences. It can tax the creativity of the best product and applications engineers. What a mess!
But it is a wonderful mess. Complexity makes sourcing parts overseas, across multiple time zones and language barriers, a very risky proposition. The world of flexible circuit manufacturing involves custom engineered parts with unique performance requirements. Every application is different. The kiss of death on most any part number is when someone states the circuit is a “no brainer.” When I hear this, it is generally time to get material ready for a restart. In an attempt to deal with the mess, the manufacturer is tempted to “standardize” their offering, often defined by comfortable or existing manufacturing capabilities. Isn’t the solution to stop building the oddball parts? Or define a niche product offering so resources can be focused? Maybe, but the business world is littered with companies that have disappeared because they were too restrictive in their willingness to change. Attempting to put in systems or procedures to deal with the complexity is noble, and existing procedures always deserve challenge, but new rules and procedures should be considered as part of a continuous improvement project rather than an end state. Change takes us out of our comfort zone, it is difficult…and often it is absolutely necessary.
Determining when engineering resources should be invested in a new application is certainly a tightrope walk. But stretching capabilities, investing in capital, and being aggressive are often requirements to staying relevant. And engineers can be pretty ingenious. Often the investment is more a clever technique rather than a new technology. Embrace the mess is a message requiring serious consideration. What does that mean? How can this be done? There are some basic principles.
First, management needs to communicate the business plan. Let employees know where you are going and how you expect them to get there. This needs to be done at a 10,000-foot level; it cannot be overly prescriptive. Goals for on-time delivery, scrap reduction, targeted customers, etc., are examples. Historical performance data helps provide context. The management message should indicate a general direction, but the specifics of execution will change as situations evolve. The best decisions are usually made by those employees closest to the problem—but only if they understand what the company is trying to accomplish and the direction the organization has targeted.
Page 1 of 2
Testimonial
"In a year when every marketing dollar mattered, I chose to keep I-Connect007 in our 2025 plan. Their commitment to high-quality, insightful content aligns with Koh Young’s values and helps readers navigate a changing industry. "
Brent Fischthal - Koh YoungSuggested Items
Indium Corporation Promotes Two Leaders in EMEA (Europe, Middle East, and Africa) Markets
08/05/2025 | Indium CorporationWith its commitment to innovation and growth through employee development, Indium Corporation today announced the promotions of Andy Seager to Associate Director, Continental Sales (EMEA), and Karthik Vijay to Senior Technical Manager (EMEA). These advancements reflect their contributions to the company’s continued innovative efforts with customers across Europe, the Middle East, and Africa (EMEA).
MacDermid Alpha Electronics Solutions Unveils Unified Global Website to Deepen Customer, Talent, and Stakeholder Engagement
07/31/2025 | MacDermid Alpha Electronics SolutionsMacDermid Alpha Electronics Solutions, the electronics business of Elements Solutions Inc, today launched macdermidalpha.com - a unified global website built to deepen digital engagement. The launch marks a significant milestone in the business’ ongoing commitment to delivering more meaningful, interactive, and impactful experiences for its customers, talent, and stakeholders worldwide.
KOKI to Showcase Analytical Services and New HF1200 Solder Paste at SMTA Guadalajara 2025
07/31/2025 | KOKIKOKI, a global leader in advanced soldering materials and process optimization services, will exhibit at the SMTA Guadalajara Expo & Tech Forum, taking place September 17 & 18, 2025 at Expo Guadalajara, Salón Jalisco Halls D & E in Guadalajara, Mexico.
Weller Tools Supports Future Talent with Exclusive Donation to SMTA Michigan Student Soldering Competition
07/23/2025 | Weller ToolsWeller Tools, the industry leader in hand soldering solutions, is proud to announce its support of the upcoming SMTA Michigan Expo & Tech Forum by donating a limited-edition 80th Anniversary Black Soldering Set to the event’s student soldering competition.
Koh Young Appoints Tom Hattori as President of Koh Young Japan
07/21/2025 | Koh YoungKoh Young Technology, the global leader in True 3D measurement-based inspection solutions, announced the appointment of Tom Hattori as President of Koh Young Japan (JKY).