-
- News
- Books
Featured Books
- pcb007 Magazine
Latest Issues
Current IssueInventing the Future with SEL
Two years after launching its state-of-the-art PCB facility, SEL shares lessons in vision, execution, and innovation, plus insights from industry icons and technology leaders shaping the future of PCB fabrication.
Sales: From Pitch to PO
From the first cold call to finally receiving that first purchase order, the July PCB007 Magazine breaks down some critical parts of the sales stack. To up your sales game, read on!
The Hole Truth: Via Integrity in an HDI World
From the drilled hole to registration across multiple sequential lamination cycles, to the quality of your copper plating, via reliability in an HDI world is becoming an ever-greater challenge. This month we look at “The Hole Truth,” from creating the “perfect” via to how you can assure via quality and reliability, the first time, every time.
- Articles
- Columns
- Links
- Media kit
||| MENU - pcb007 Magazine
What a Long, Strange Trip it’s Been—and It’s a Long Way from Being Over
February 9, 2016 | Barry Matties, I-Connect007Estimated reading time: 14 minutes
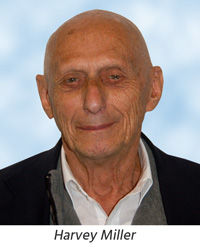
A Conversation with Industry Icon Harvey Miller
Harvey Miller has been in the PCB industry for more than 40 years, and while I’ll let him disclose his exact age, I think it’s safe to say he’s probably seen it all. I recently sat down with Harvey at a local wine bar in Palo Alto, CA to learn more about his history in the industry and where he sees it going forward from his truly unique perspective. I must admit I was a bit inspired when Harvey arrived to our meeting wearing jogging shorts and running shoes. No surprise after what his doctor recently shared with him.
Barry Matties: Harvey, thanks for joining us today. You have been in the industry for many years. What year did you get started?
Miller: In the Middle Ages.
Matties: There is a lot of speculation as to your exact age. Can you clarify for our readers?
Miller: You know, I have no problem disclosing that. I turned 93 on November 23, actually. A year ago, a cardiologist at Stanford told me that I have the heart of a 40-year-old, so I guess it’s 41 now. According to the actuarial tables, I am right around 79 or something like that.
Matties: So you are here for another 30 years.
Miller: Or I have been dead for about 14 years. [laughs]
Matties: It was a different world when you were born.
Miller: Yeah, it was 1922. The big growth industry was the automotive industry.
Matties: It’s the growth industry today too, isn't it?
Miller: Some things never change, right? It’s a different kind of automobile now—not the Model T. Of course, that is when forced obsolescence was born. William Durant of GM came up with the yearly models and that has been the model ever since. Now they do it by Moore's Law. I don't know what’s going to happen when Moore Law's runs out, because that has been the mechanism for obsolescence. Of course it won’t run out; there will be other things that will take its place.
Matties: What sort of education did you have?
Miller: I studied economics at the University of Michigan.
Matties: Were you born here in the San Francisco Bay Area?
Miller: No, I was born in Baltimore, Maryland but I grew up in Northern Ohio and then went to the University of Michigan. My father was a salesman, actually. He sold furniture. In the 1920s, Middletown, Ohio, was at the center of the automobile industries. Middletown as well as Akron were tributaries to Detroit. Akron backed them with tires, of course. Canton had tin can roller bearings and Diebold made safes and other things, and now they make ATMs.
When I was in the Army they sent me to study electrical engineering for 18 months, but that petered out because the war was over. They had a special program, and I got lucky because I was always good in those intelligence tests, and that is how I spent the war years. I later went back to the University of Michigan.
Matties: So not only were you trained in electrical engineering, you finished up in economics. It sounds like you were very well-suited for analysis in our business. Has your entire career been in circuits?
Miller: I went to work for a consulting company as a precursor. It wasn't as a participant. I never had my hands in the chemistry, but just as an analyst.
Matties: What year did you start?
Miller: I worked for a bunch of OEMs and back then whenever an OEM got to around $100 million they built a board shop. They all had board shops. I guess when I got interested in boards and printed circuit technology it was probably the early ‘70s, maybe 1973 or so.
In those days, probably more than half of the shops were captive shops, and certainly then for the next decade and through the 1980s. It wasn't until Moore's Law forced density and the fabrication got a little too sophisticated that OEMs like IBM, etc., decided that it wasn't their business. That’s when all the big independents started to blossom and bloom, like Hadco and Zycon, etc., in response to the captives getting out of the business.
Matties: In all the years that you have been involved in this industry, what is the most surprising thing that comes to mind?
Miller: I guess the most surprising thing is the growth of the Chinese industry, because nobody would have anticipated that.
Matties: What do we have left in the U.S.? Something like 280 shops?
Miller: Around 300, but it’s the dollars that matter. It’s been totaled around $3 billion, which represents 5% worldwide. That is another surprising thing. The North American share went from 90% to 5% between the years of 1975 and 2015.
Matties: But most of it left around 2001; it was like somebody turned off a light switch. It was just gone. That was surprising, but there was a big race to low-cost labor.
Miller: And that is part of a pattern. It wasn't just the board industry, obviously. People talk about reshoring, but they don't realize it is going to take one of those paradigm shifts. So we are going to do an end run around those guys over there. That is what we should be looking at, not reconstituting the old technology and beating them with that, because we can't.
Matties: It has to be something new, like the Occam process.
Miller: I think embedded is the more general term, and Occam includes that. What Occam and Joe Fjelstad did was add another feature to embedding—which has not made an appearance yet, in general—that separates the two platforms. I’m paraphrasing Joe's work on Occam, but he had one platform for the components and another platform for the interconnect. Except most of the interconnects are relegated to the third dimension. That does a lot of really wonderful things, because it relieves the substrate of the constraints for doing both. They’re two separate functions: holding the components and interconnecting them. They should not be on the same substrate, because one of the drawbacks is you have conductive anodic filaments (CAF). They grew up with the glass cloth idea. They needed a really rigid substrate and glass cloth with epoxy cure made a great substrate.
And that is the backbone of the conventional board industry. But it has the drawback that as the dimensions get smaller, filaments in the glass are conductive, and it shorts. If you separate the two functions of holding components and interconnecting them, then you are free to go to all kinds of other substrates that don't have that drawback, besides the cost savings, etc. So embedding is the general word and I think Occam is a little twist that adds a lot to that, which people haven't seen yet.
Matties: How long do you think it will be before we really embrace embedded technology, because solder joints are the big cause of failure, right?
Page 1 of 3
Testimonial
"Advertising in PCB007 Magazine has been a great way to showcase our bare board testers to the right audience. The I-Connect007 team makes the process smooth and professional. We’re proud to be featured in such a trusted publication."
Klaus Koziol - atgSuggested Items
Indium Corporation Promotes Two Leaders in EMEA (Europe, Middle East, and Africa) Markets
08/05/2025 | Indium CorporationWith its commitment to innovation and growth through employee development, Indium Corporation today announced the promotions of Andy Seager to Associate Director, Continental Sales (EMEA), and Karthik Vijay to Senior Technical Manager (EMEA). These advancements reflect their contributions to the company’s continued innovative efforts with customers across Europe, the Middle East, and Africa (EMEA).
MacDermid Alpha Electronics Solutions Unveils Unified Global Website to Deepen Customer, Talent, and Stakeholder Engagement
07/31/2025 | MacDermid Alpha Electronics SolutionsMacDermid Alpha Electronics Solutions, the electronics business of Elements Solutions Inc, today launched macdermidalpha.com - a unified global website built to deepen digital engagement. The launch marks a significant milestone in the business’ ongoing commitment to delivering more meaningful, interactive, and impactful experiences for its customers, talent, and stakeholders worldwide.
KOKI to Showcase Analytical Services and New HF1200 Solder Paste at SMTA Guadalajara 2025
07/31/2025 | KOKIKOKI, a global leader in advanced soldering materials and process optimization services, will exhibit at the SMTA Guadalajara Expo & Tech Forum, taking place September 17 & 18, 2025 at Expo Guadalajara, Salón Jalisco Halls D & E in Guadalajara, Mexico.
Weller Tools Supports Future Talent with Exclusive Donation to SMTA Michigan Student Soldering Competition
07/23/2025 | Weller ToolsWeller Tools, the industry leader in hand soldering solutions, is proud to announce its support of the upcoming SMTA Michigan Expo & Tech Forum by donating a limited-edition 80th Anniversary Black Soldering Set to the event’s student soldering competition.
Koh Young Appoints Tom Hattori as President of Koh Young Japan
07/21/2025 | Koh YoungKoh Young Technology, the global leader in True 3D measurement-based inspection solutions, announced the appointment of Tom Hattori as President of Koh Young Japan (JKY).