-
- News
- Books
Featured Books
- pcb007 Magazine
Latest Issues
Current IssueInventing the Future with SEL
Two years after launching its state-of-the-art PCB facility, SEL shares lessons in vision, execution, and innovation, plus insights from industry icons and technology leaders shaping the future of PCB fabrication.
Sales: From Pitch to PO
From the first cold call to finally receiving that first purchase order, the July PCB007 Magazine breaks down some critical parts of the sales stack. To up your sales game, read on!
The Hole Truth: Via Integrity in an HDI World
From the drilled hole to registration across multiple sequential lamination cycles, to the quality of your copper plating, via reliability in an HDI world is becoming an ever-greater challenge. This month we look at “The Hole Truth,” from creating the “perfect” via to how you can assure via quality and reliability, the first time, every time.
- Articles
- Columns
- Links
- Media kit
||| MENU - pcb007 Magazine
Patricia (Patty) Goldman Inducted into IPC Hall of Fame
March 18, 2016 | Barry Matties, I-Connect007Estimated reading time: 10 minutes
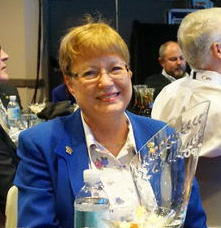
This week we attended the 2016 IPC APEX EXPO in Las Vegas, and one part of that was the introduction of this year’s IPC Hall of Fame inductee. We at I-Connect007 are thrilled that our own Patty Goldman has been awarded the highest level of volunteer recognition that IPC can give to an individual, the Raymond E. Pritchard Hall of Fame Award. The award is given in recognition of superior achievement, extraordinary contributions and distinguished service to IPC and the advancement of the electronics industry.
Patty has more than three decades of experience in the PCB industry and has volunteered countless hours to IPC. During this time she has been an active participant in numerous committees and chairman of several, including theTechnical Activities Executive Committee (TAEC) and the Technical Program Committee (TPC) for IPC APEX EXPO. Among her past honors, Patty was recognized in 1984 with the IPC President's Award for her contributions to IPC and the industry.
Patty joined the I-Connect007 team in 2011 and has since become managing editor of The PCB Magazine and an integral part of the team. When we attend industry events with Patty it’s clear how impactful she has been and how well respected she is by her peers. Congratulations Patty! We’re so happy for you.
The following is a brief interview with Patty about her history at IPC.
Barry Matties: Why don't we just start with you telling us a little bit about how you got started with IPC?
Patty Goldman: In the very early ‘80s, I went to my first IPC meeting. I was working at a small PCB facility in Connecticut—Qualitron—and I was the chemist, so I was the go-to person for most production problems. At the time, there was very little information out there on how to make a PCB. There were no magazines; there was only The Printed Circuits Handbook, and that really didn't go into the detail I needed.
I went to the meeting and found a few subcommittees that could be helpful, and the one that I really hooked up with was the Process Effects subcommittee, which is all about troubleshooting. But the troubleshooting guide, called PE-74, was brief and at least half of it was TBD— to be developed; there were so many blanks in it. An effort to revise it was underway but it was going nowhere. After a meeting or two, I asked the IPC liaison person, Dieter Bergman, how to get this moving. I said, "I'll even chair it if that helps." Which was, of course, as you can imagine, just what he wanted—a real live volunteer.
Anyhow, we started with an interim meeting in December in Boston. We were a group of about 10 people and we spent three days developing an outline. We all took chapters to write and work on, and went from there. In a couple of years, we had a finished document that had no TBDs in it. It may not have had all the troubleshooting information, but it was a great start. In the meantime, I learned a ton about how to make PCBs.
That’s when I realized that volunteering and getting involved is not just beneficial for the documents and specs and everything else, but perhaps as importantly, you yourself learn so much. In the meantime, you also are working with people with the same interests. You start to build a whole network of people that you can call upon whenever you have a problem that you can't solve yourself.
That's how I got started. I was chairman of that subcommittee for about 20 years. We went through three revs and somewhere in there I was chairing the committee that was above that subcommittee, and moved through a couple of jobs and so forth. I was elected as chairman of TAEC in 1998, when I was out of the room, but I did make a couple of changes to those meetings and for the better, I believe. After a while, I turned the PE subcommittee over to somebody else, and was asked to chair the Woven Glass Reinforcement Subcommittee, mainly because it was a really contentious group, and they were hoping that I would calm everything down—which actually worked out really well. Once you get involved in IPC, they know who can make things move and who can solve some problems, so they call on you when they need you.
Matties: So you’ve been actively involved for more than 30 years, right?
Goldman: Since the early ‘80s—‘80 or ‘81, somewhere around there. One of the things I've seen with people is you can change jobs but as long as your company sees fit to send you to IPC, the same people are volunteers no matter where they work. You just are that type of person, and you see the value in it. I've learned a tremendous amount and I've met a ton of people, many of whom have become very good, close friends.
I was working on the Process Effects Handbook (the troubleshooting guide), and we were talking everything to do with printed circuits, including some design, so every person that I met, I swear, once I found out what they were good at, I asked them to write a section. You can ask a lot of people at IPC, and they'll say, "Yeah. I worked on that. I worked for her." That's how I met so very many people.
Matties: In your time with IPC and volunteering and working there, what was the greatest surprise for you?
Goldman: One of the surprises for me, and this has nothing to do with the industry, was that I actually picked up some really good management skills while I was chairman that I have found very useful all along the line. That was unexpected, but great. I always say that managing volunteers is like herding cats—all these people from different companies who don’t really have to listen to you or follow you, so you have to figure out how to get everyone moving in the same direction.
As far as surprises in the industry, we can all say that the big move to China was, but it wasn't really a surprise. You could see it coming, and as it happened, no matter how much we railed against it, it still happened.
Matties: A lot of people would say they didn't even see it coming when the first crash came around.
Page 1 of 2
Testimonial
"In a year when every marketing dollar mattered, I chose to keep I-Connect007 in our 2025 plan. Their commitment to high-quality, insightful content aligns with Koh Young’s values and helps readers navigate a changing industry. "
Brent Fischthal - Koh YoungSuggested Items
How Good Design Enables Sustainable PCBs
08/21/2025 | Gerry Partida, Summit InterconnectSustainability has become a key focus for PCB companies seeking to reduce waste, conserve energy, and optimize resources. While many discussions on sustainability center around materials or energy-efficient processes, PCB design is an often overlooked factor that lies at the heart of manufacturing. Good design practices, especially those based on established IPC standards, play a central role in enabling sustainable PCB production. By ensuring designs are manufacturable and reliable, engineers can significantly reduce the environmental impact of their products.
50% Copper Tariffs, 100% Chip Uncertainty, and a Truce
08/19/2025 | Andy Shaughnessy, I-Connect007If you’re like me, tariffs were not on your radar screen until a few months ago, but now political rhetoric has turned to presidential action. Tariffs are front-page news with major developments coming directly from the Oval Office. These are not typical times. President Donald Trump campaigned on tariff reform, and he’s now busy revamping America’s tariff policy.
Global PCB Connections: Understanding the General Fabrication Process—A Designer’s Hidden Advantage
08/14/2025 | Markus Voeltz -- Column: Global PCB ConnectionsDesigners don’t need to become fabricators, but understanding the basics of PCB fabrication can save you time, money, and frustration. The more you understand what’s happening on the shop floor, the better you’ll be able to prevent downstream issues. As you move into more advanced designs like HDI, flex circuits, stacked vias, and embedded components, this foundational knowledge becomes even more critical. Remember: the fabricator is your partner.
MKS’ Atotech to Participate in IPCA Electronics Expo 2025
08/11/2025 | AtotechMKS Inc., a global provider of enabling technologies that transform our world, announced that its strategic brands ESI® (laser systems) and Atotech® (process chemicals, equipment, software, and services) will showcase their latest range of leading manufacturing solutions for printed circuit board (PCB) and package substrate manufacturing at the upcoming 17th IPCA Show to be held at Pragati Maidan, New Delhi from August 21-23, 2025.
MKS Showcases Next-generation PCB Manufacturing Solutions at the Thailand Electronics Circuit Asia 2025
08/06/2025 | MKS Instruments, Inc.MKS Inc, a global provider of enabling technologies that transform our world, today announced its participation in Thailand Electronics Circuit Asia 2025 (THECA 2025), taking place August 20–22 at BITEC in Bangkok.