-
-
News
News Highlights
- Books
Featured Books
- pcb007 Magazine
Latest Issues
Current IssueThe Hole Truth: Via Integrity in an HDI World
From the drilled hole to registration across multiple sequential lamination cycles, to the quality of your copper plating, via reliability in an HDI world is becoming an ever-greater challenge. This month we look at “The Hole Truth,” from creating the “perfect” via to how you can assure via quality and reliability, the first time, every time.
In Pursuit of Perfection: Defect Reduction
For bare PCB board fabrication, defect reduction is a critical aspect of a company's bottom line profitability. In this issue, we examine how imaging, etching, and plating processes can provide information and insight into reducing defects and increasing yields.
Voices of the Industry
We take the pulse of the PCB industry by sharing insights from leading fabricators and suppliers in this month's issue. We've gathered their thoughts on the new U.S. administration, spending, the war in Ukraine, and their most pressing needs. It’s an eye-opening and enlightening look behind the curtain.
- Articles
- Columns
- Links
- Media kit
||| MENU - pcb007 Magazine
New Management and Strategies at eSurface
June 3, 2016 | Barry Matties, I-Connect007Estimated reading time: 11 minutes
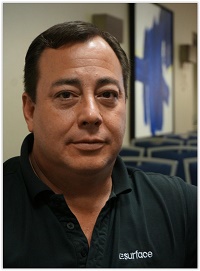
At the recent Geek-A-Palooza, I spoke with Alex Richardson and Rick McCann of eSurface Technologies, to learn about the condition of the company, their new semi-additive approach, and a couple of big announcements.
Barry Matties: Alex, let’s start with what eSurface does.
Alex Richardson: Basically we're a technology company, and what we have is a proprietary chemistry and process that we license enabling a new ability to construct circuit boards with an additive process, as opposed to conventional subtractive processes. It is a photoactive chemistry, and we use UV activation, which triggers an auto catalytic conversion that happens during the exposure. We have the ability to either do pattern imaging or complete flood imaging of the panel and utilize those for either fully-additive or semi-additive manufacturing processes.
Matties: How long have you been in the market?
Richardson: About five years.
Matties: Are you where you thought you would be?
Richardson: Well, it takes a long time for the patents to be granted and we intentionally had to stay below the radar until this was accomplished. In the summer of 2014 we were awarded global pioneering patents for our technology, and that allowed us to emerge with less apprehension and a more public posture. We then started rolling out the technology without the obvious IP infringement concerns.
Matties: How's the industry adopting this technology—are they embracing it fully? I ask this question because I've heard mixed reviews.
Richardson: Adoption to major changes in this industry is always slow, but we have made great strides in edifying the technology and getting adoption over the last year. You have to understand, the industry's seen at least three decades of failed promises on additive approaches. Holistically, eSurface is a completely different approach to this type of technology because we're not a topical agent, a silver ink, or other method that has been tried in the past, which typically yielded very poor results with resistance to solvents or adhesion in manufacturing further downstream. We have a very robust process. With our chemistry and process we get an elemental bond between the metal and the actual material itself, so we don't have the typical delamination factors. What we have is a very robust bond. To separate the bond, we typically see a cohesive failure or a breakdown of the material itself instead of adhesion failure which is what the industry has typically seen as the failure point in historical approaches.
We also have the ability to control circuit dimensions, to the constraints of applied imaging capability and quality. This translates to unmatched ultra-fine feature and tolerance capabilities.
As far as the adoption process, we've gone through a gamut of testing on different types of materials. Obviously our global industry is coming up with more and more materials on a consistent basis that we need to then validate. We've become quite inundated with the number of requests from entities looking for testing on their specific material. Many of these materials are custom or proprietary and not in catalogues or available here in the United States. We've seen a very wide influx of advanced materials, and opportunities to move forward on high volume applications.
Matties: What sort of approval cycle does a fabricator or an OEM require for this process to be adopted?
Richardson: This is basically a process change. There are no impactful barriers and no real specifications put out by any of our governing bodies like the IPC or any of the industry standards committees. What we're looking for is the adhesion qualities of the copper to the panel. We're currently leaning with the path that most of the industry has adopted, which is the semi-additive approach, where eSurface is a drop-in opportunity using all the current prolific processes. We are simply replacing the copper clad foil laminated or bonded onto the panel, and we're applying a stronger and more robust layer of copper that is elementally bonded to the substrate. We are using the same build-up copper that they are already using in production today. There really is no need for any qualification beyond adhesion, solderability, SIR, and the things that you normally associate with standard PCB testing, all of which we have accomplished.
Matties: And the customers are fine with this, and they adopt it?
Richardson: Absolutely. I think the biggest obstacle was people getting their head around interconnect/via construction. Once they understand the technology, and this does not affect or change their current via plating and interconnect process, adoption is typically imminent.
Matties: In terms of pricing, is this a process that actually lowers the total manufacturing cost, or is it on par?
Richardson: I think if you look at semi-additive, it is definitely in parity to conventional costs, because we're using most of the same practices. So there isn't a real cost delta for the actual manufacturing process, or labor that goes into the manufacturing cycle. Where we do see the cost advantage is if we take challenging designs and improve yields from the twenties and thirties to above nineties, then we have an opportunity for a large rolled yield savings. Obviously this also optimizes throughput of the factory by mitigating restarts.
Matties: Is the 90+ a typical result?
Richardson: Yes, we have seen incredible results that can be realized quickly.
Matties: How many facilities have adopted this process so far?
Richardson: Today we have seven facilities commercially licensed globally. We really just started rolling out the technology into facilities in the last year or so. We are excited to continue to secure new licensees; this month we signed a new local fabricator and are in the process of putting equipment into place. Beyond fabricator licensees, we are working with iconic OEMs in strategic relationships.
Matties: Are the facilities primarily here in North America?
Richardson: Over half of them are here in North America; we also have some licensees in Asia and Europe.
Matties: Are those high-volume production situations?
Richardson: They’re all different. It's a mixed bag. Some are used for micro-electronics, some are used for three dimensional items, and some are planar applications like for PCB or flex. Our current equipment is already designed for automated rate production.
Matties: So what do you guys expect? Where do you see this in the next couple of years?
Richardson: Well, we've taken a different model as of Q4 2015. I think we took our first swing at bat in early 2015 with a royalty licensing model, and were trying to push adoption from the PCB manufacturing level. We've changed that strategy. Now we're actually partnering with large, iconic OEMs and driving it down the food chain, which I think is going to make a significant difference. We're a great enabler for some technologies, or for stranded IP that can't get to market due to some of the manufacturing concerns related to etching processes or other challenges in the industry. This is a great enabler, and I think we're going to find a lot of big wins as we develop relationships with the OEMs and drive this technology into the market, while still licensing and supporting our manufacturing partners to enable manufacturing resource availability.
Matties: Now we've talked about the technology, what about the health of the company? I've heard there's been some ups and downs; where are you guys at in terms of that?
Richardson: We're a startup company, and as with most startups, we’ve had our ups and downs. Everybody wants to talk about an IPO home run like Google, or Facebook, but they've all had their internal issues as well. We did have to go through a management and model change-up in Q4 of last year, and we had to make a calculated decision whether to take the technology and restart the company, or to go on and just knuckle through it. We opted to knuckle through it and respect our shareholders and our licensees. Quite frankly we've done an outstanding job and are emerging in Q2 2016 with a very solid and bright future.
The new philosophies are working extremely well, and we've had some great successes. I think the tenacity and efforts are well appreciated within our shareholders, licensees, and our employees.
Matties: That’s great. One of the toughest things I've seen in this industry is people trying to bring in new technologies, and the rate of failure. Even technologies where you think, “Holy cow, this is a home run,” just don't make it.
Richardson: This is a “show me” industry and a tough one at that. They're not fast adopters; there's a lot of gray beards that say, “We've done it for years this way, and this is the way we shall be doing it in the future…” We're being driven by market demand from design, the chipsets that are going on boards, the frequencies that we're utilizing, and the types of applications and environments. Unfortunately, we need advancement and change. The PCB industry hasn’t really experienced a radical construction change over the last two decades. Beyond advances in laser imaging and drilling we haven’t experienced any real significant impacts. Capabilities have grown and are now stretched, but the basic construction methodology hasn't evolved. We need to get creativity flowing and enable novel new technologies to advance.
Matties: Printed electronics obviously is coming into play in a strong way, and doing interviews with companies like Nano Dimension, who is printing multi-layers. It just seems like we're only years away from a truly disruptive replacement to a complete additive process.
Richardson: I agree with printing technologies being on the forefront, and eSurface supports that technology jump. We actually can change the media or carrier of our chemistry and how it is applied. Right now we use an aqueous-based carrier. We can change that to be dry, like a toner cartridge, or it could be more viscous like those in an inkjet, and we've already explored different paths. We see our technology as being a very enabling aspect of printed electronics. We can see PCBs being produced using this type of technology, preparing surfaces, UV activating, metallization, and curing all in the same piece of equipment.
Matties: Even though we see it coming, I think it still is going to take us by surprise.
Rick McCann: We agree, Barry. This is something that our team has been anticipating. We have a thoughtfully constructed technology roadmap that encompasses printed electronics and more. As Alex pointed out, eSurface’s present iteration has been designed to easily integrate into existing PCB facilities right now, as is; with their existing equipment and processes, with little or no barriers for adoption. Looking forward, the eSurface roadmap is intended to help manufacturers adopt and optimize new practices (like printed electronics), explore new market opportunities, and to meet the challenges ahead of us as electronics evolve and advance.
Matties: Is there a point in time when someone should consider using your product, or is this just something that they should consider using in all applications?
Richardson: Saying eSurface is the fix-all for everything is not realistic. For PCB fabricators we are a bolt-on technology; and I think we're an enabling technology. and I think it's more of a technology that doesn't disrupt all aspects of the PCB supply chain and processing, but complements current manufacturing practices. The semi-additive approach can be dropped into almost any board shop today and have huge impacts for capabilities. We recently took a manufacturer with 5-mil L/S capabilities, and converted them over to a 1-mil L/S facility in a matter of a week or two, with less than $100k of capital equipment, training and infrastructure. That would typically take years and a very significant impact on capital expenditures.
Matties: And yield?
Richardson: We see a significant yield improvement. I believe the drop-in semi-additive approach will be quickly and widely adopted as we continue to roll out products and grow acceptance with large OEMs that see the benefit of this technology. I see the creativity that has been somewhat stalled over the last few years in U.S. PCB innovation getting revitalized. Advanced technical leads get invigorated when they understand the eSurface technology and they are eager to employ this technology to develop a multitude of different of paths with their own subject matter experts within their facilities.
Matties: It sounds like you guys are at an exciting point in time right now with some new management and strategies. Is there anything else you would like to add?
McCann: If we could, this might be a good forum to announce the two agreements that we executed this quarter.
Richardson: Yes, we have some announcements. eSurface has signed a Letter of Intent with a very iconic, publicly traded company with a huge portfolio of IP that they spent hundreds of millions of dollars on for development but never carried to the finish line. Many of the patents can utilize eSurface to complete that technology, and come to production and commercialization. The agreement calls for the formation of a Special Purpose Entity that will be focused on the joint development of over 150 technology patents, many related to photonics and photovoltaics.
Matties: If that comes to fruition in the way you hope, that's a huge win right there.
Richardson: It's a huge win, and there's a big governmental initiative in the area of photonics to bring back innovation and new technology in the U.S., for obvious reasons. We are right in the sweet spot of that technology sector.
We've also just signed a technology License with Firan Technology Group, a prominent North American based PCB manufacturer with facilities in the U.S., Canada, and Asia. FTG has been a longtime supporter and strategic partner of eSurface and we are excited about the many commercial opportunities that are already on deck.
Matties: Well, congratulations, guys. This is very exciting. Thanks for spending time with me today.
Richardson: Thank you.
Suggested Items
The Evolution of Picosecond Laser Drilling
06/19/2025 | Marcy LaRont, PCB007 MagazineIs it hard to imagine a single laser pulse reduced not only from nanoseconds to picoseconds in its pulse duration, but even to femtoseconds? Well, buckle up because it seems we are there. In this interview, Dr. Stefan Rung, technical director of laser machines at Schmoll Maschinen GmbH, traces the technology trajectory of the laser drill from the CO2 laser to cutting-edge picosecond and hybrid laser drilling systems, highlighting the benefits and limitations of each method, and demonstrating how laser innovations are shaping the future of PCB fabrication.
Day 2: More Cutting-edge Insights at the EIPC Summer Conference
06/18/2025 | Pete Starkey, I-Connect007The European Institute for the PCB Community (EIPC) summer conference took place this year in Edinburgh, Scotland, June 3-4. This is the third of three articles on the conference. The other two cover Day 1’s sessions and the opening keynote speech. Below is a recap of the second day’s sessions.
Day 1: Cutting Edge Insights at the EIPC Summer Conference
06/17/2025 | Pete Starkey, I-Connect007The European Institute for the PCB Community (EIPC) Summer Conference took place this year in Edinburgh, Scotland, June 3-4. This is the second of three articles on the conference. The other two cover the keynote speeches and Day 2 of the technical conference. Below is a recap of the first day’s sessions.
Preventing Surface Prep Defects and Ensuring Reliability
06/10/2025 | Marcy LaRont, PCB007 MagazineIn printed circuit board (PCB) fabrication, surface preparation is a critical process that ensures strong adhesion, reliable plating, and long-term product performance. Without proper surface treatment, manufacturers may encounter defects such as delamination, poor solder mask adhesion, and plating failures. This article examines key surface preparation techniques, common defects resulting from improper processes, and real-world case studies that illustrate best practices.
RF PCB Design Tips and Tricks
05/08/2025 | Cherie Litson, EPTAC MIT CID/CID+There are many great books, videos, and information online about designing PCBs for RF circuits. A few of my favorite RF sources are Hans Rosenberg, Stephen Chavez, and Rick Hartley, but there are many more. These PCB design engineers have a very good perspective on what it takes to take an RF design from schematic concept to PCB layout.