-
- News
- Books
Featured Books
- pcb007 Magazine
Latest Issues
Current IssueInventing the Future with SEL
Two years after launching its state-of-the-art PCB facility, SEL shares lessons in vision, execution, and innovation, plus insights from industry icons and technology leaders shaping the future of PCB fabrication.
Sales: From Pitch to PO
From the first cold call to finally receiving that first purchase order, the July PCB007 Magazine breaks down some critical parts of the sales stack. To up your sales game, read on!
The Hole Truth: Via Integrity in an HDI World
From the drilled hole to registration across multiple sequential lamination cycles, to the quality of your copper plating, via reliability in an HDI world is becoming an ever-greater challenge. This month we look at “The Hole Truth,” from creating the “perfect” via to how you can assure via quality and reliability, the first time, every time.
- Articles
- Columns
- Links
- Media kit
||| MENU - pcb007 Magazine
Flex is Where It’s At
August 18, 2016 | Patty Goldman, I-Connect007Estimated reading time: 4 minutes
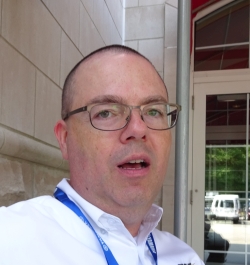
A number of the more astute PCB companies are finding the local SMTA expos very advantageous to attend and exhibit at, and it is interesting to talk with them when possible. I met with Jack Baculik of Circuits LLC, a rather new flex manufacturer not far from the SMTA-Ohio Expo we were both attending. It sure seems that flex and rigid-flex is what everyone is looking at.
Patty Goldman: Jack, please fill me in a little bit on Circuits LLC. I don't know very much even though they're rather close by to me.
Jack Baculik: We are close by. Circuits LLC has been in business since 2008, so we’re a relatively new company located in Murrysville, Pennsylvania, which is a suburb of Pittsburgh. We’re considered a small company by the federal government; we have 25 employees. We make flex and rigid-flex printed circuit boards, so we don't make any rigid boards, but if it has a piece of flex in it we'll build it. So that's one niche of ours.
Another niche of ours is our experience. Even though we're a new company we have well over 200 years of manufacturing and engineering experience in making the flex product. We work with companies up front and help them out with material choices, bend radius, impedance—because a lot of companies are still new to flex, even though flex has been around for many, many years some people are new to it.
Goldman: I feel like they're waking up to it.
Baculik: Waking up to it out of necessity. Some people have maybe used it 20 years ago, got burned by it because it was just a bad experience and now they need to fit something big into a small footprint and flex or rigid-flex is the only way to go.
Goldman: I guess there are more and more applications, and more need?
Baculik: Yeah, a lot of hand-held products. Military is big in flex and rigid-flex. It's a very robust product. We make boards that go into military devices. They're out in the field and these soldiers need to communicate with each other so they can't be having breakdowns out in the field.
Goldman: So military is one of the markets you serve. How about medical?
Baculik: Medical, industrial controls, industrial products.
Goldman: So a lot of things use flex, really.
Baculik: Yes. Your iPhone has flex even though it's not bent, like for weight issues, because it's very light and thin.
Goldman: Are most of the applications involving something that's going to be bent or folded? Like you said, the cellphone has it in there but it's flat.
Baculik: I would say the majority of the applications would be bend-to-install. So you'll populate the parts and you'll bend the flex circuit and put it into whatever box it's going into.
Goldman: And there it stays.
Baculik: It temporarily stays. Sometimes it can be dynamic, where it's opening and closing a couple hundred thousand times, but more times than not it will be bend-to-install.
Goldman: That's a pretty important part of it though, because otherwise it won't fit! Laughs)
Baculik: We need to know bend-to-install versus a dynamic application. If it’s dynamic, you’re going to get a change of material, you’re going to have to change your copper, and then change how it’s manufactured. It's good to work with the costumer up front to know what their end products will be so we can help them go down the right path.
Goldman: I hear that both ways, that some costumers don't want to work with the circuit board shop. They just want to throw it over the wall. Do you find in flex that most people want to work with you?
Baculik: They do, because you can take the other parts and throw it over the wall and who knows how many times you're going to revise something to get it to work. You’re spending all that time and money trying to get your end product to do what you want it to do. Whereas if you work with them up front it will only take one or two spins, and then you can define the design a lot quicker and cheaper. It's less of a headache for everybody.
Goldman: How long have you been with Circuits LLC?
Baculik: I've been there since 2013. So three and a half years.
Goldman: It's going well, I take it?
Baculik: Yeah, things are going well. Business is improving every year and there's more and more need for flex.
Goldman: It's the latest, greatest, we always say. Especially when you throw in rigid-flex, your possibilities become endless, I would think. How's the show here for you?
Baculik: The show's been going well. We've had a few people stop by that could be some potential business. All it takes is the one good one and it's all worthwhile.
Goldman: As I was thinking before that, if you want to pick up business in the local area, these little SMTA shows seem like the way to go. They present a great opportunity to meet potential customers face-to-face in a nice, laid-back atmosphere.
Baculik: We're about half way through the day, but it's been going good.
Goldman: Great. More power to you! Nice talking with you.
Baculik: Thank you very much.
Testimonial
"The I-Connect007 team is outstanding—kind, responsive, and a true marketing partner. Their design team created fresh, eye-catching ads, and their editorial support polished our content to let our brand shine. Thank you all! "
Sweeney Ng - CEE PCBSuggested Items
How Good Design Enables Sustainable PCBs
08/21/2025 | Gerry Partida, Summit InterconnectSustainability has become a key focus for PCB companies seeking to reduce waste, conserve energy, and optimize resources. While many discussions on sustainability center around materials or energy-efficient processes, PCB design is an often overlooked factor that lies at the heart of manufacturing. Good design practices, especially those based on established IPC standards, play a central role in enabling sustainable PCB production. By ensuring designs are manufacturable and reliable, engineers can significantly reduce the environmental impact of their products.
50% Copper Tariffs, 100% Chip Uncertainty, and a Truce
08/19/2025 | Andy Shaughnessy, I-Connect007If you’re like me, tariffs were not on your radar screen until a few months ago, but now political rhetoric has turned to presidential action. Tariffs are front-page news with major developments coming directly from the Oval Office. These are not typical times. President Donald Trump campaigned on tariff reform, and he’s now busy revamping America’s tariff policy.
Global PCB Connections: Understanding the General Fabrication Process—A Designer’s Hidden Advantage
08/14/2025 | Markus Voeltz -- Column: Global PCB ConnectionsDesigners don’t need to become fabricators, but understanding the basics of PCB fabrication can save you time, money, and frustration. The more you understand what’s happening on the shop floor, the better you’ll be able to prevent downstream issues. As you move into more advanced designs like HDI, flex circuits, stacked vias, and embedded components, this foundational knowledge becomes even more critical. Remember: the fabricator is your partner.
MKS’ Atotech to Participate in IPCA Electronics Expo 2025
08/11/2025 | AtotechMKS Inc., a global provider of enabling technologies that transform our world, announced that its strategic brands ESI® (laser systems) and Atotech® (process chemicals, equipment, software, and services) will showcase their latest range of leading manufacturing solutions for printed circuit board (PCB) and package substrate manufacturing at the upcoming 17th IPCA Show to be held at Pragati Maidan, New Delhi from August 21-23, 2025.
MKS Showcases Next-generation PCB Manufacturing Solutions at the Thailand Electronics Circuit Asia 2025
08/06/2025 | MKS Instruments, Inc.MKS Inc, a global provider of enabling technologies that transform our world, today announced its participation in Thailand Electronics Circuit Asia 2025 (THECA 2025), taking place August 20–22 at BITEC in Bangkok.