All About Flex: Flexible Circuit Prototypes
October 13, 2016 | Dave Becker, All FlexEstimated reading time: 4 minutes
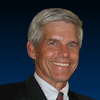
Most electronic projects begin with at least one build of prototype parts before moving into volume manufacturing. But the definition of a flex circuit prototype can vary considerably from one project to another. In many cases, a prototype build is only a few parts used to verify form, fit and function, with engineering trying to determine if something actually works. In other instances, a prototype must not only satisfy the requirement of form, fit and function but the materials and processes used in the prototype stage are expected to be representative of what is used during serial volume production. These prototype parts may also be used for customer qualification testing with the intention of ‘baselining’ a design, process sequence, or equipment. It is more descriptive to refer to these parts as ‘pre-production prototypes’ or even ‘qualification parts.’
While there tends to be differences in what an individual company may view as the scope of a prototype, there are several elements common to most prototype requirements. These generally include compressed lead times, low volume and in most instances soft tooling.
Some companies expect multiple runs of prototypes with the intention of going into production with a ‘copy exact’ design. This approach is intended to reduce startup costs but may delay a design decision as a part iteratively evolves through multiple build cycles. Early involvement between the designer and the circuit fabrication manufacturer often helps eliminate some of the iterations.
There are a few different prototype manufacturing and support strategies evident in the flexible circuit industry. Some “prototype shops” specialize in low volume, quick-turn flexible circuits and don’t intend to support volume production. These quick-turn shops may have less formal manufacturing systems and often are more restrictive with material limitations due to stocked inventory. They depend on skilled operator/technicians to accompany parts throughout the manufacturing sequence within facilities structured to quickly produce low volume parts. In many cases, once the quick turn prototype phase is complete the customer will seek sources for the serial production parts in an alternative facility.
Another option occurs when a circuit fabrication facility operates a prototype area separate from the production area. This might include separate staffing in addition to equipment and physical location. With this option the prototype area deploys similar but alternative processing equipment and technology. When the prototype stage has been completed, the product is moved to the production group and is tooled to run at high volume.
These two strategies have the advantage of allowing each group or facility to focus more on its competency. A production facility can focus on high-volume production. The prototype facility can focus on fast turnaround.
This strategy can also have some disadvantages. First, some projects require prototypes to be representative of production parts. A prototype built in a different facility with different equipment and perhaps using different chemistries and process materials is not likely to satisfy a customer with a strict requirement for a product that’s tested and qualified as a final step before volume production. Differences between prototype and production could include plating and etching chemistries, imaging resists, press materials and processing methods. Even if the two parts built in different facilities both meet IPC 6013 tests and inspections, high reliability customers are likely to have issues with these differences. Second, there is a ‘lessons learned’ consideration. A prototype build offers an opportunity to optimize processing to improve yields or efficiency—which ultimately converts to price. If the prototype is built somewhere else, the production facility will go through their own learning curve.
Another printed circuit prototype model is to fabricate with the same equipment, chemicals and process materials as volume production parts. This requires more sophisticated scheduling and nimbleness with equipment set-up and tooling. But in this way, the transition from prototype stage to production manufacturing becomes a matter of scale. It has the advantage of using the same equipment between the initial run and subsequent builds. A key requirement is to produce parts without any long lead time tooling. Numerically controlled drilling and routing, laser direct imaging, laser ablation and NC-controlled punches are examples. There is no time waiting for a tool and very little setup time, and changes can be made quickly.
Physical tools may be introduced to improve efficiency or throughput when parts move to steady state and higher volume. Examples of physical tooling might include a hard tool blank die to define the cutline instead of an NC-controlled router, more sophisticated assembly fixturing, or use of a dedicated electrical test fixture instead of a universal flying probe tester.
Prototypes present a vital opportunity to not only reduce start-up costs, but to provide the customer a better part with higher quality levels and better delivery performance. Early design involvement by the supplier can often result in a more robust product with lower manufacturing costs—and fewer prototype builds.
Dave Becker is vice president of sales and marketing at All Flex Flexible Circuits LLC.
Testimonial
"In a year when every marketing dollar mattered, I chose to keep I-Connect007 in our 2025 plan. Their commitment to high-quality, insightful content aligns with Koh Young’s values and helps readers navigate a changing industry. "
Brent Fischthal - Koh YoungSuggested Items
Meet the Author Podcast: Martyn Gaudion Unpacks the Secrets of High-Speed PCB Design
07/16/2025 | I-Connect007In this special Meet the Author episode of the On the Line with… podcast, Nolan Johnson sits down with Martyn Gaudion, signal integrity expert, managing director of Polar Instruments, and three-time author in I-Connect007’s popular The Printed Circuit Designer’s Guide to... series.
Intervala Hosts Employee Car and Motorcycle Show, Benefit Nonprofits
08/27/2024 | IntervalaIntervala hosted an employee car and motorcycle show, aptly named the Vala-Cruise and it was a roaring success! Employees had the chance to show off their prized wheels, and it was incredible to see the variety and passion on display.
KIC Honored with IPC Recognition for 25 Years of Membership and Contributions to Electronics Manufacturing Industry
06/24/2024 | KICKIC, a renowned pioneer in thermal process and temperature measurement solutions for electronics manufacturing, is proud to announce that it has been recognized by IPC for 25 years of membership and significant contributions to electronics manufacturing.
Boeing Starliner Spacecraft Completes Successful Crewed Docking with International Space Station
06/07/2024 | BoeingNASA astronauts Barry "Butch" Wilmore and Sunita "Suni" Williams successfully docked Boeing's Starliner spacecraft to the International Space Station (ISS), about 26 hours after launching from Cape Canaveral Space Force Station.
KIC’s Miles Moreau to Present Profiling Basics and Best Practices at SMTA Wisconsin Chapter PCBA Profile Workshop
01/25/2024 | KICKIC, a renowned pioneer in thermal process and temperature measurement solutions for electronics manufacturing, announces that Miles Moreau, General Manager, will be a featured speaker at the SMTA Wisconsin Chapter In-Person PCBA Profile Workshop.