Sensible Design: The Little Guide to Resins
October 17, 2016 | Alistair Little, ElectrolubeEstimated reading time: 2 minutes
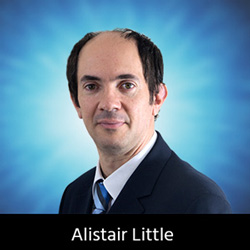
Over past months, this column has seen Electrolube’s Phil Kinner provide The PCB Design Magazine readers with information, guidance and practical tips on the uses and application of conformal coatings. He now hands over the reins to me, and I plan to do the same for resins, starting this month with a “back to basics” piece that questions the core rationale for potting—why and how do we do it, and what are we trying to achieve or protect?
First, a little background. I joined Electrolube as global business technical director for the Resins Division in January 2016. I currently head up a team of chemists developing formulations that encompass epoxy, polyurethane and silicone resin systems for encapsulating or potting electrical devices or electronic components in order to protect them against a wide range of environments.
In my previous appointment at Gurit (UK) I held the position of senior product development chemist, responsible for the development of new epoxy and vinyl ester resin systems for aerospace, automotive, engineering and marine composite systems. Prior to this, I worked for 2K Polymer Systems, where I developed civil engineering and structural adhesives, and at SI Group, where I worked on UV curing and high-performance resins.
I have wide experience working within ISO 9000, 14001 and 18001 accredited systems, and I am an expert in vinyl ester resin systems (for which I am in the process of completing a PhD in Polymer Chemistry at Loughborough University). I am a Chartered Chemist, an active member of the Royal Society of Chemistry, and a member of the Society of Adhesion and Adhesives.
Resins: Why, Where and How?
I would like to start this series of columns by going back to basics, questioning the core rationale for potting and encapsulation with resins, their fundamental chemistries and how each resin type differs one from the other—indeed, how their individual properties can be exploited to maximise performance under a wide range of environmental conditions.
Let’s start with moisture, the archenemy of electrical and electronic devices that, quite apart from causing short-circuits, can also lead to premature deterioration of components due to corrosion. Polyurethane resins—usually supplied as two-part products, which, when mixed achieve the desired cure—provide that all-important moisture resistance, as well as excellent electrical insulation, flexibility and good adhesion to most substrates, both metal and plastic. Some polyurethane resin systems provide exceptional resistance to sea water, as well as temperature extremes, making them an ideal choice for marine applications such as sensor encapsulation. A good outdoor example of a polyurethane resin encapsulated component that requires maximum protection against water ingress is an LED lighting unit; these resins are also optically clear and UV stable, making them ideal for the task.
To read this entire article, which appeared in the September 2016 issue of The PCB Design Magazine, click here.
Suggested Items
Merlin Circuit Technology Earns NADCAP 2nd Year Merit
05/13/2025 | Merlin Circuit TechnologyMerlin Circuit Technology Ltd, a leading manufacturer of advanced printed circuit boards (PCBs) for mission-critical applications, has announced the successful completion of its latest NADCAP audit, achieving prestigious 2nd Year Merit Status.
Vertical Aerospace, Honeywell Expand Partnership to Bring VX4 eVTOL to Market
05/13/2025 | HoneywellVertical Aerospace and Honeywell announced the signing of a new long-term agreement that expands their existing partnership and reinforces Honeywell’s commitment to the certification and production of Vertical’s electric vertical take-off and landing (eVTOL) aircraft, the VX4.
Barnes Aerospace Appoints George Whittier as CEO
05/12/2025 | BUSINESS WIREBarnes Aerospace, a global provider of component repair services and manufacturer of highly-engineered parts primarily for aeroengines and an operating division of Barnes Group Inc., announced the appointment of George Whittier to the newly created role of CEO, effective May 12, 2025.
'Chill Out' with TopLine’s President Martin Hart to Discuss Cold Electronics at SPWG 2025
05/02/2025 | TopLineBraided Solder Columns can withstand the rigors of deep space cold and cryogenic environments, and represent a robust new solution to challenges facing next generation large packages in electronics assembly.
Kitron: Q1 2025 - Strong Start to the Year
04/25/2025 | KitronKitron reported first-quarter results characterised by continued momentum in the Defence & Aerospace market sector and a growing order backlog.