IPC Validation Services Audit Program to Include Laminate, Prepreg Manufacturers
November 1, 2016 | Patty Goldman, I-Connect007Estimated reading time: 9 minutes
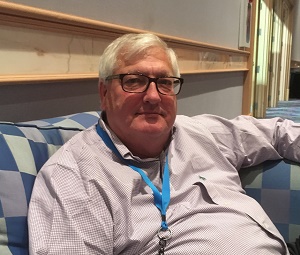
Essex Technologies’ Doug Sober is a long-time IPC chairman who is now also working with IPC’s Validation Services division. I met with Doug while at the recent SMTA International conference, and we discussed the upcoming audit program for laminate manufacturers, which is ready to go.
Patty Goldman: Doug, tell us a little about what you’ve been working on here.
Doug Sober: On the IPC front, back in November, we rolled out a program for Validation Services of IPC-6012, which is the rigid board specification. Two companies have participated—gone through the audit and done the testing of the coupons—and now IPC has an active QML for IPC-6012.
In addition to that, the exciting part now for me—since I've been the Base Materials Chairman since 1996—is that we're going to have a validation services program for IPC-4101D—the base material specification for laminates and prepregs that go into rigid printed boards.
Goldman: So it would be the laminate suppliers that would go through this testing?
Sober: Yes. This is specifically for the manufacturers of laminates and prepregs, not flexible materials, just the normal laminates and prepregs that go into rigid printed boards.
Goldman: And it’s ready to roll?
Sober: It's ready to roll. Dave Bergman and I conceived it at a meeting in Nuremberg, Germany. We've scoped a program out. We've determined the program cost. This program is a little bit different in that it is a QPL, meaning it's a qualified product list as opposed to a QML which is a qualified manufacturing list. Like we did in MIL-S-13949, the old mil spec that we had cancelled in 1997, there are qualification tests that have to be run.
The way it works is just like the other Validation Services programs. There's a list of pre-audit questions that come right out of the specification. So in IPC-4101D, each paragraph that says "You shall…" means we're going to have some sort of verification step that documents that you actually do it. The CCL and prepreg supplier will have this list of questions up front. In the case of 4101, there are about 98 questions that are already on the pre-audit checklist.
The laminate and prepreg supplier will get a copy of the questions in advance, and they have to self-evaluate themselves versus the requirement paragraph. For example, if it says that you will have am IPC-1730 document on file, (which is a self-reporting document that we developed at IPC a long time ago) then the auditor will look to see if you have that document in place. Now, you'll already have told us on a scale of 0 to 4 whether you have that in place and we just come in and verify that it is there. Or in the case of prepreg, where it says you shall store your prepregs in one of two storage conditions, you'll rate yourself on a scale of 0 to 4 on that aspect of it as well; then, we will come in and just simply look in your prepreg storage room to see that it meets one of the two conditions outlined in 4101D.
It's not an ISO audit. It's very straightforward, right out of the document and the good thing is you get a chance to see exactly what we're going to ask. We don't deviate from the pre-audit questions at all, and so that is the audit portion of the Validations Services program.
Goldman: Why is there a feeling that this is necessary? Surely people have been testing stuff all along, right?
Sober: Well, DSCC, the military group that administered MIL-S-13949, was the policeman for the laminate and prepreg group, and when we discontinued it to go to IPC-4101, there was a conscious decision made on the part of several of us that had generated that document and the IPC office that we did not want the policeman anymore. The policeman was very expensive and we were spending somewhere between $250,000 and $300,000 a year per company to be able to sign ourselves to a MIL-S-13949 mil spec cert.
On the other hand, I could go to jail if I signed something on a cert and I wasn't actually doing the testing, or if I lied on the testing or did something that was a little more devious than that. There was a lot of teeth to it, and so we all did things to the letter of the law, but we did not want to do that for IPC-4101 and the companies that were already mil spec certified. We continued to do things on the up-and-up like we should have. The problem is quite frankly we now have all of these new laminate prepreg suppliers, who have started from scratch. We all know the problems we've had with counterfeit materials and things not being exactly the way they are supposed to be. The problem was nobody was looking over their shoulder to make sure that materials were qualified, that the testing for the certification process was being followed or any of that sort of thing. A lot of the low cost opportunities that the Asian manufacturers brought to the table were because they weren't actually doing a lot of the backup work to make sure that their products were up to snuff.
For example, I was dealing with a company in China and the certification said for a Tg that it was 135°C minimum, and the certification said that the tested value was 137.2. However, this 137.2 was on each and every certification that they signed and sent out. When we examined the company, we found that there wasn't even a TMA or DSC instrument on site.
Goldman: So they couldn't have been measuring it.
Sober: They could not have been measuring it. In addition, they had stamped their documents saying that they were an IPC member, which they were not. This is the kind of thing that we want to glean out. These kinds of people would never come to the table and want a Validation Services audit done at their facility. We're looking for the ones that have already been toeing the line and want to separate themselves from some of these other people.
Let me tell you about the QPL part of it. We have Specification Sheets in IPC-4101D, so let's pick Slash Sheet 99, which everybody has the material for and some manufacturers have several materials for. What you would do is send samples found in the Table 3-1 out of IPC-4101D qualification scheme. There are 23 tests I believe that have to be qualified, and these have to be tested at a Validation Services accredited laboratory, of which there are three around the world. So you have to cut the specimens, send them to the test lab and have them tested.
Once they're tested, that product will be put on the QPL listing under that specification sheet. You will have an audit of a facility that will be on the IPC website in the listing, and for each facility in your company, you have to do the audit again, so you might have multiple sites that have been audited, and then you would have the material that was tested for Specification Sheet 99. It would be on that website listed under a table, so customers, board shops, assembly shops, OEMs, if they want to see all the people that are QPL listed for Slash Sheet 99, they simply would have to go to the website and the manufacturer and the material grade would show under that column.
Now if you have a second material that you're selling to Slash Sheet 99, here you would simply have to present data from any laboratory to the IPC office and you could have that also put on the QPL, but that will be listed as “self-tested.” So it will show which ones have been tested, which ones have been “self-tested,” but for each Specification Sheet you only have to do the outside test once.
Goldman: Would they do this outside testing once a year, or once a lifetime? What’s the time frame like?
Sober: The QPL part of the qualification testing is done once every five years. For the QML part, the audit of the facility is done every year, but the second and third years are very limited. It can be done without even visiting the facility, so it's basically a three-year program with years two and three just being a cursory review mostly by paperwork.
Right now we have the pre-audit questions finished. We have the quote package finished. We have the manufacturers’ agreement finished, and we have quoted two laminate suppliers, both in Asia. We have several more that we've talked to here in the United States. I believe that we'll do at least two audits before the end of the year. So this is rolling out a little bit faster than even the IPC-6012 validation services plan that was rolled out.
Goldman: I'm guessing that at least some of these laminate manufacturers are looking to this as a really good thing because it will help to differentiate them from those that are making counterfeit materials or materials that aren't really tested, and I know this has been a problem for a lot of years.
Sober: Yes. The program is not nearly as complex as for 6012 or for an assembly shop. The board shop has 50−70 different process steps. The laminate facility has basically eight or 10 process steps, so it's a lot simpler and a lot cleaner and a lot easier to judge whether you're doing things in the proper way.
Goldman: It's mainly testing the material to make sure it's what you say it is.
Sober: Exactly, and that you have the equipment on-site to do the testing and to do the proper certifications. There's a workmanship aspect to 4101 which allows us to look into some of the processes to make sure that there are things like viscosity control at the prepreg machines and so forth.
Goldman: How about their raw materials? Is some part of it controlling their incoming materials?
Sober: Yes, for example, with glass fabric. It says that the glass fabric purchased must be purchased in accordance with IPC 4412, the glass fabric specification. We're just going to look at the purchase orders to see if that indeed is being done, and that'll cover the raw materials part of it. There are other aspects of the materials, like for example the difference between brominated materials and halogen-free materials. We could send that test out to have it verified that the halogen-free materials are indeed meeting the maximum requirement for chlorine and bromine, but in that particular case, to save money, we're just simply going to let them supply us their UL certification.
Goldman: Oh, which will tell you the same thing.
Sober: That will tell us that it's been tested at the UL lab and they passed the halogen-free specifications, so I've tried to take a lot of the costs out of the qualification process. The audit itself would only take a couple of days to do, so we're trying to keep this program well under $10,000 for the first audit and one specification sheet.
Goldman: Super. We should definitely talk at IPC APEX EXPO 2017 in February and see how it's going.
Sober: Yes, I hope by then that we will have maybe four companies, at least two, already on the website. In the case of the IPC-4101D, they see the value of themselves being listed, where the IPC-6012 people seem to feel that they will not do it unless they're dragged kicking and screaming by their customer base. It's a whole different mindset as far as how the program has been accepted, and again this happened really quickly. I think we first started somewhere in May or April and here we are already rocking and rolling.
Goldman: Okay, this going to be very interesting. Thanks so much for your time.
Sober: Thank you.
Suggested Items
Legislative Update: Is the SEMI Investment Act Inclusive of PCB and Substrates?
05/13/2025 | I-Connect007 Editorial TeamIn response to this week's news about new U.S. legislation being put forth by SEMI to support our domestic electronics supply chain—the Strengthening Essential Manufacturing and Industrial (SEMI) Investment Act—IPC’s Richard Capetto, senior director of North American Government Relations, made the following statement.
Delta Builds First IPC-CFX Demonstration Line in Asia-Pacific
05/14/2025 | Chuck Li, IPC North AsiaAs a key standard in the global electronics manufacturing industry, IPC-CFX has been implemented in various regions worldwide, providing the foundation for digital factory solutions. In the Asia-Pacific region, IPC actively promotes this standard, helping enterprises enhance efficiency and competitiveness through digital transformation.
Hunting for Clues: Feng Xue Solving Circuit Board 'Crimes' With AOI Standard
05/08/2025 | Linda Stepanich, IPCWhen residents in sleepy English villages needed a top-tier detective to solve a murder, they called on Belgian super-sleuth Hercule Poirot, author Agatha Christie’s fictional detective famous for using his “little grey cells” to solve crimes. In the same way, IPC standards development committees, when creating a standard to detect defects in circuit boards using Automated Optical Inspection (AOI), call on IPC A-Team, Hercule.
IPC Strengthens Global Focus with Promotion of Sanjay Huprikar to Chief Global Officer
05/08/2025 | IPCIPC, the global electronics association, announces the promotion of Sanjay Huprikar to chief global officer. This newly created position reflects the association’s forward-looking strategy and industry needs to strengthen the electronics supply chain.
Navigating Global Manufacturing in an Era of Uncertainty
05/07/2025 | Philip Stoten, ScoopThe EMS industry faces unprecedented challenges as global trade tensions rise and tariff announcements create market uncertainty. In an overview of IPC Europe’s podcast, MADE IN EUROPE, industry experts from GPV and Zollner examine how these developments impact our businesses and customers, and what strategies will prevail in this new landscape.