NASA Aircraft Arrival Technology Gets Big Test in 2017
November 1, 2016 | NASAEstimated reading time: 3 minutes
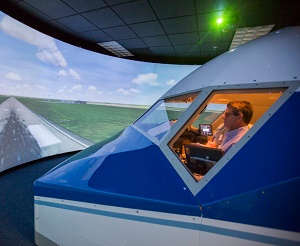
Commercial airline pilots who as children played “Follow the Leader” will have no problem with a new air traffic control innovation NASA and its partners are working on that also will make passengers happier.
It’s called Flight Deck Interval Management, or FIM, and it promises to safely increase the number of airplanes that can land on the same runway at busy airports by more precisely managing the time, or interval, between each aircraft arrival.
Less time in the air also means additional savings in expensive jet fuel and reduced aircraft emissions. Even better: passengers would enjoy an increased chance their flights – connecting or otherwise – will arrive on time.
FIM is part of NASA’s Air Traffic Management Technology Demonstration-1– or ATD-1 – a coordinated effort involving NASA, the Federal Aviation Administration (FAA), and industry to develop and evaluate new technologies and procedures related to aircraft scheduling and airport arrivals.
A complex field demonstration of FIM involving NASA, the FAA and industry will be conducted in early 2017 over Washington State.
Today, current air traffic control technology and procedures can predict arrival times to within a minute or so. But FIM is expected to enable controllers and the airport to count on aircraft arriving within five to ten seconds of a predicted time.
The cockpit-based prototype FIM system combines NASA-developed software with commercially available off-the-shelf hardware and connects the system to the aircraft’s onboard information and navigation systems.
“FIM allows controllers to deliver the aircraft more precisely and more predictably, which is a huge advantage that helps the airlines and airport operators more efficiently manage air traffic to minimize delays,” said William Johnson, ATD-1 project manager at NASA’s Langley Research Center in Virginia.
Here’s how FIM is to work:
Relying on their experience and existing tools – some previously developed by NASA and turned over to the FAA for deployment – air traffic controllers determine the ideal goal for spacing aircraft as they approach the airport.
A controller then contacts the pilots of a particular aircraft, informing them of the spacing goal, the trajectory the aircraft should fly, and the ID of an aircraft ahead of them. This is where the idea of playing “follow the leader” comes into the picture.
The pilots then enter all of this information into the FIM system, which then computes a solution with the additional help of input from the airplane’s Automatic Dependent Surveillance-Broadcast (ADS-B) unit. ADS-B is a satellite-based navigation tool that allows pilots to know where they and other ADS-B-equipped aircraft are at all times.
The result is a number displayed on FIM screens for the pilots to see that tells them what speed to fly so they can follow the specified aircraft a safe distance in front of them all the way down to the runway.
“The FIM operation was designed to work in today’s modern commercial aircraft with minimal changes to the aircraft and flight crew procedures,” Johnson said.
At the heart of FIM is NASA software called ASTAR, or Airborne Spacing for Terminal Arrival Routes, which was successfully demonstrated in 2014 flying aboard Boeing’s ecoDemonstrator 787 aircraft.
During those “proof of concept” flight tests, ASTAR was operated on a laptop by a NASA engineer located in the main cabin of the airplane, who then radioed the speed commands to the pilots up in the cockpit.
For ATD-1 in 2017, ASTAR will be loaded into commercially available hardware, which is essentially flight hardened and certified personal tablets that will be installed on the flight deck in plain view of the pilots.
The field demonstration will take place over Seattle and encompass a fully coordinated effort involving NASA, FAA facilities, and three different aircraft: A Falcon 900 jet and Boeing 757 supplied by Honeywell, and a Boeing 737 provided by United Airlines.
The Honeywell 757 and United 737 will be equipped with the FIM system in its cockpits, where its pilots will “follow the leader” behind the Falcon.
After years of research and laboratory work, final preparations for the full airborne demonstration of FIM are well underway. Pilot orientations have already taken place and more are scheduled, while a major review of lessons learned so far will be presented to a joint NASA/FAA/industry committee during a four-day meeting beginning Oct. 31.
Suggested Items
Meet the Author Podcast: Martyn Gaudion Unpacks the Secrets of High-Speed PCB Design
07/10/2025 | I-Connect007In this special Meet the Author episode of the On the Line with… podcast, Nolan Johnson sits down with Martyn Gaudion, signal integrity expert, managing director of Polar Instruments, and three-time author in I-Connect007’s popular The Printed Circuit Designer’s Guide to... series.
Intervala Hosts Employee Car and Motorcycle Show, Benefit Nonprofits
08/27/2024 | IntervalaIntervala hosted an employee car and motorcycle show, aptly named the Vala-Cruise and it was a roaring success! Employees had the chance to show off their prized wheels, and it was incredible to see the variety and passion on display.
KIC Honored with IPC Recognition for 25 Years of Membership and Contributions to Electronics Manufacturing Industry
06/24/2024 | KICKIC, a renowned pioneer in thermal process and temperature measurement solutions for electronics manufacturing, is proud to announce that it has been recognized by IPC for 25 years of membership and significant contributions to electronics manufacturing.
Boeing Starliner Spacecraft Completes Successful Crewed Docking with International Space Station
06/07/2024 | BoeingNASA astronauts Barry "Butch" Wilmore and Sunita "Suni" Williams successfully docked Boeing's Starliner spacecraft to the International Space Station (ISS), about 26 hours after launching from Cape Canaveral Space Force Station.
KIC’s Miles Moreau to Present Profiling Basics and Best Practices at SMTA Wisconsin Chapter PCBA Profile Workshop
01/25/2024 | KICKIC, a renowned pioneer in thermal process and temperature measurement solutions for electronics manufacturing, announces that Miles Moreau, General Manager, will be a featured speaker at the SMTA Wisconsin Chapter In-Person PCBA Profile Workshop.