Aismalibar on Markets, Materials, and the Increase in Copper Prices
December 5, 2016 | Pete Starkey, Barry Matties - I-Connect007Estimated reading time: 15 minutes
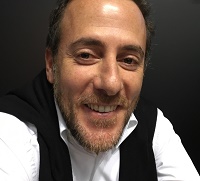
As a European laminate provider specializing in insulated metal substrates and thermal management, Aismalibar is often put in the demanding position of catering to some of Europe’s toughest customers, including the automotive industry. Pete Starkey and Barry Matties caught up with Director General Eduardo Benmayor at the most recent Electronica trade show to learn more about the company and get his take on the current state of the IMS marketplace.
Barry Matties: Eduardo, can you begin by telling us a little bit about Aismalibar?
Eduardo Benmayor: Aismalibar is a copper-clad laminate company and we have been in this industry since the beginning of electronics. Aismalibar was one of the first laminate companies in Europe, launching the first laminates in the 1950s. Today we are following electronics and we are concentrated on a niche product in the laminate business, an insulated metal substrate dedicated to thermal management problems. As you know, electronics are getting smaller and smaller every day and heat dissipation is a key factor. We are really dedicated to this segment inside electronics.
Pete Starkey: Eduardo, when we walked into your booth you were forming a very intricate paper doll out of a profiled and etched material. Can you tell us a little bit about that?
Benmayor: That's right. You have seen one of our most popular laminates today. It's called Flextherm. That's a thin aluminum in the range of 0.8 mm to 1.5 mm cladded into copper with a very thin, dielectric layer and it's capable to be formed to different shapes. The goal here is to make flat PCBs, populate them with the components, and then be able to bend and shape them into different forms. The goal of this laminate is to improve the old technology built with a conformed aluminium cladded with a flex PCB on top from one shot of element. Flextherm saves a lot of money on assembly and gives a lot of reliability to the electronic component itself, as technology and thermal performance is much better.
Starkey: That particular circuit that you were forming, what would be the application for that?
Benmayor: That's a real light of a BMW 7. We developed this together with their team. We are doing a lot of lights development in the automotive industry.
Starkey: Is the automotive industry the main growth area for IMS materials?
Benmayor: No, it's not the main growth area but it's the most demanding area. The automotive industry is probably peaking with technology and quality and there is a big request for fast dissipation on PCBs in the automotive industry and that's why we are really focused in this area.
Starkey: We're familiar with application of this automotive lighting, but what about developments in the electric vehicles and power management? Do you have applications in that area?
Benmayor: Yes, it's based always on the same principle. The electrical vehicles have a lot of power inside the models and require a lot of electrical strength. That's also a niche area of Aismalibar, where the fast thermal dissipation and the electrical strength are very important in these elements, and we are seeing a nice increase, especially in the power models used in the electrical automotive industry.
Page 1 of 3
Suggested Items
Trouble in Your Tank: Can You Drill the Perfect Hole?
07/07/2025 | Michael Carano -- Column: Trouble in Your TankIn the movie “Friday Night Lights,” the head football coach (played by Billy Bob Thornton) addresses his high school football team on a hot day in August in West Texas. He asks his players one question: “Can you be perfect?” That is an interesting question, in football and the printed circuit board fabrication world, where being perfect is somewhat elusive. When it comes to mechanical drilling and via formation, can you drill the perfect hole time after time?
The Evolution of Picosecond Laser Drilling
06/19/2025 | Marcy LaRont, PCB007 MagazineIs it hard to imagine a single laser pulse reduced not only from nanoseconds to picoseconds in its pulse duration, but even to femtoseconds? Well, buckle up because it seems we are there. In this interview, Dr. Stefan Rung, technical director of laser machines at Schmoll Maschinen GmbH, traces the technology trajectory of the laser drill from the CO2 laser to cutting-edge picosecond and hybrid laser drilling systems, highlighting the benefits and limitations of each method, and demonstrating how laser innovations are shaping the future of PCB fabrication.
Day 2: More Cutting-edge Insights at the EIPC Summer Conference
06/18/2025 | Pete Starkey, I-Connect007The European Institute for the PCB Community (EIPC) summer conference took place this year in Edinburgh, Scotland, June 3-4. This is the third of three articles on the conference. The other two cover Day 1’s sessions and the opening keynote speech. Below is a recap of the second day’s sessions.
Day 1: Cutting Edge Insights at the EIPC Summer Conference
06/17/2025 | Pete Starkey, I-Connect007The European Institute for the PCB Community (EIPC) Summer Conference took place this year in Edinburgh, Scotland, June 3-4. This is the second of three articles on the conference. The other two cover the keynote speeches and Day 2 of the technical conference. Below is a recap of the first day’s sessions.
Preventing Surface Prep Defects and Ensuring Reliability
06/10/2025 | Marcy LaRont, PCB007 MagazineIn printed circuit board (PCB) fabrication, surface preparation is a critical process that ensures strong adhesion, reliable plating, and long-term product performance. Without proper surface treatment, manufacturers may encounter defects such as delamination, poor solder mask adhesion, and plating failures. This article examines key surface preparation techniques, common defects resulting from improper processes, and real-world case studies that illustrate best practices.