Could a Seawater Battery Help End our Dependence on Lithium?
December 9, 2016 | ACSEstimated reading time: 1 minute
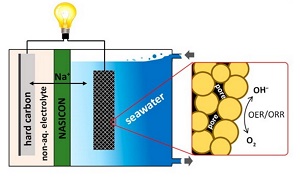
With the ubiquity of lithium-ion batteries in smartphones and other rechargeable devices, it’s hard to imagine replacing them. But the rising price of lithium has spurred a search for alternatives. One up-and-coming battery technology uses abundant, readily available seawater. Now, making this option viable is one step closer with a new report on a sodium-air, seawater battery. The study appears in the journal ACS Applied Materials & Interfaces.
Sodium-air — or sodium-oxygen — batteries are considered one of the most promising, and cost-effective alternatives to today’s lithium-ion standby. But some challenges remain before they can become a commercial reality. Soo Min Hwang, Youngsik Kim and colleagues have been tackling these challenges, using seawater as the catholyte — an electrolyte and cathode combined. In batteries, the electrolyte is the component that allows an electrical charge to flow between the cathode and anode. A constant flow of seawater into and out of the battery provides the sodium ions and water responsible for producing a charge. The reactions have been sluggish, however, so the researchers wanted to find a way to speed them up.
For their new battery, the team prepared a catalyst using porous cobalt manganese oxide nanoparticles. The pores create a large surface area for encouraging the electrochemical reactions needed to produce a charge. A hard carbon electrode served as the anode. The resulting battery performed efficiently over 100 cycles with an average discharge voltage of about 2.7 volts. This doesn’t yet measure up to a lithium-ion cell, which can reach 3.6 to 4.0 volts, but the advance is getting close to bridging the gap, the researchers say.
Suggested Items
Foxconn's Tiger Leap Combining Nature and Technology in Ecological Roof Garden
04/23/2025 | FoxconnHon Hai Technology Group, the world's largest technology manufacturing and service provider, has actively responded to the United Nations Sustainable Development Goals (SDGs).
IDTechEx Highlights Recyclable Materials for PCBs
04/10/2025 | IDTechExConventional printed circuit board (PCB) manufacturing is wasteful, harmful to the environment and energy intensive. This can be mitigated by the implementation of new recyclable materials and technologies, which have the potential to revolutionize electronics manufacturing.
Bridging the Gap Between PCB Designers and Fabricators
04/03/2025 | Stephen V. Chavez, Siemens EDAWith today’s advanced EDA tools, designing complex PCBs in the virtual world does not necessarily mean they can be built in the real world. This makes the relationship between a PCB designer and a fabricator pivotal to the success of a project. In keeping with solid design for manufacturing (DFM) practices, clear and frequent communication is needed to dial and lock in design constraints that meet expectations while addressing manufacturing concerns.
Hitachi Announces Completion of New Production Facility for Semiconductor Manufacturing Equipment
04/01/2025 | JCN NewswireHitachi High-Tech Corporation announced that the new production facility for semiconductormanufacturing equipment (etch systems), which had been under construction since December 2023 in the Kasado area (Kudamatsu City, Yamaguchi Prefecture), was completed and started the operation on March 17, 2025.
Paige Fiet: From Emerging Engineer to Quality at TTM
03/19/2025 | Marcy LaRont, PCB007 MagazinePaige Fiet is a graduate of the IPC Emerging Engineer program and now works at TTM Technologies in Logan, Utah. She was an IPC Student Board Member and has been a columnist for I-Connect007. She is a stellar example and an encouragement to other young engineers about how to be successful in your early career.