Advanced Copper Foil Secures a Non-Provisional Patent for New Product: Poly-Supported Copper Foil
January 13, 2017 | Advanced Copper FoilEstimated reading time: 1 minute
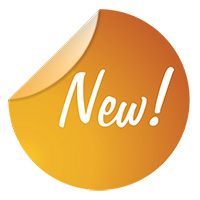
Advanced Copper Foil has secured an international patent for Poly-Supported Copper Foil, promoted under the name ACF-Screen. This patent is non-Provisional under International Application number PCT/050938.
ACF-Screen is comprised of a proprietary protective Poly Release film, which is adhered to sheets of ultra-thin copper foil in a cleanroom environment. This product provides complete protection of the copper surface throughout the entire cycle of PCB layup and lamination. ACF-Screen utilizes an inert adhesive which results in a guaranteed residue-free copper surface during subsequent processing. The release film will withstand temperatures of the lamination cycle, allowing for easy removal during break-down. ACF-Screen will eliminate anomalies caused by bending or creasing of copper foils during handling, while always completely protecting the surface from foreign materials and contamination. This product is available on copper foils from 5 µm, 9 µm to 70 µm. ACF-Screen is available on Standard, VLP, HVLP and ANP (Almost No Profile) copper foils.
“This product is going to revolutionize the industry. It will ease the handling of copper foils compared to loose foils, resulting in more efficient and speedier layup process,” says Shane Stewart, Product Manager.
ACF will be showcasing this product at the IPC APEX show in San Diego on February 14-16. Drop by the booth (#3701) for more information and to request samples of this new revolutionary product.
About Advanced Copper Foil
Advanced Copper Foil is a company dedicated to High Performance Copper Foils and their applications in the Printed Circuit and Battery Shielding Industries. Advanced Copper Foil is committed to providing PCB Fabricators, Laminate Manufacturers and Battery Shielding Companies with a cost-effective alternative to the traditional products on the market today. For further information visit: www.advancedcopperfoil.com
Suggested Items
RF PCB Design Tips and Tricks
05/08/2025 | Cherie Litson, EPTAC MIT CID/CID+There are many great books, videos, and information online about designing PCBs for RF circuits. A few of my favorite RF sources are Hans Rosenberg, Stephen Chavez, and Rick Hartley, but there are many more. These PCB design engineers have a very good perspective on what it takes to take an RF design from schematic concept to PCB layout.
Trouble in Your Tank: Causes of Plating Voids, Pre-electroless Copper
05/09/2025 | Michael Carano -- Column: Trouble in Your TankIn the business of printed circuit fabrication, yield-reducing and costly defects can easily catch even the most seasoned engineers and production personnel off guard. In this month’s column, I’ll investigate copper plating voids with their genesis in the pre-plating process steps.
Elephantech: For a Greener Tomorrow
04/16/2025 | Marcy LaRont, PCB007 MagazineNobuhiko Okamoto is the global sales and marketing manager for Elephantech Inc., a Japanese startup with a vision to make electronics more sustainable. The company is developing a metal inkjet technology that can print directly on the substrate and then give it a copper thickness by plating. In this interview, he discusses this novel technology's environmental advantages, as well as its potential benefits for the PCB manufacturing and semiconductor packaging segments.
Trouble in Your Tank: Organic Addition Agents in Electrolytic Copper Plating
04/15/2025 | Michael Carano -- Column: Trouble in Your TankThere are numerous factors at play in the science of electroplating or, as most often called, electrolytic plating. One critical element is the use of organic addition agents and their role in copper plating. The function and use of these chemical compounds will be explored in more detail.
IDTechEx Highlights Recyclable Materials for PCBs
04/10/2025 | IDTechExConventional printed circuit board (PCB) manufacturing is wasteful, harmful to the environment and energy intensive. This can be mitigated by the implementation of new recyclable materials and technologies, which have the potential to revolutionize electronics manufacturing.