Ladle on Manufacturing: Material Matters
January 17, 2017 | Marc Ladle, Viking Test Ltd.Estimated reading time: 5 minutes
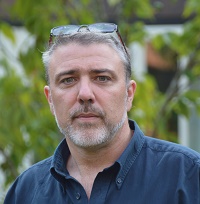
Have you considered whether or not you could improve your multilayer yields by better use of your base materials? Perhaps the following could give you a few ideas of how this could help you.
Not long after I had taken a job as production engineer in a large backplane factory I found myself investigating a batch of circuits with 30% fall-out at electrical test, most of which had been diagnosed as short circuits due to innerlayer mis-registration. I had been given a free hand to find and fix any problems I saw fit so this product seemed like a good place to start. When I looked at data for previous batches I noted that this product always had a high failure for registration—30% was a common failure level at test.
The PCB was a 12-layer panel and around 4.5 mm thick with a single circuit on each production panel. The active area of each circuit was around 450 mm by 500 mm. The design was a mixture of ground plane and tracked layers. Looking from one side to the other, the build involved three cores of 0.8 mm and one piece each of 0.36 mm and 0.25 mm. I did check with the design team if there was any option to change the build-up but the core thicknesses and separations had to remain for technical and product qualification reasons.
Off to the lab! I cut out the areas that I identified as the most likely place of short circuit (based on locating them with a tone ohm). I then ground them down on an abrasive disk until I found the short. The result was that the material was not moving in a uniform way. In particular, the 0.25 mm core seemed to be unstable. The tooling for these panels during the bonding process was based on four slotted pins. After further investigations (more sections and lots of grinding), I had demonstrated that all layer positions were pretty close to the tooling pins and right along the centre lines of the panel so I was pretty confident that the bonding tooling system was not directly at fault.
After many hours of cutting and grinding I had no fingerprints left on the ends of several fingers and data which suggested that in any one panel only one of the four corners had excess material movement substantial enough to start to give problems with layer-to-layer line-up. Usually the largest movement was found on the 0.25 and 0.36 mm cores. I would expect the thin cores to be less stable but the wild card in the data was, why does only one corner move and why was it not always the same corner?
It was not unusual for me to get occasional visits from the technical sales representatives for various materials suppliers. We used a substantial amount of material and for a UK company we were an attractive account. Over a coffee, I discussed my results with the rep for the largest of the European suppliers at that time. He sowed the seeds of an idea when we talked about what was happening to the panel during the bonding process. I realised that the base material was being manufactured by a very similar process and my idea was that the corners of the manufacturing sheet were probably subject to higher internal stress—and therefore movement—than the centre of the same panel.
The first experiment I made was a small scale. I cut the innerlayers carefully from the centre of each sheet of base material but otherwise manufactured the circuits as normal. I think I made 10 panels like this. All 10 of them passed electrical test but no matter—they were destined for more cutting and grinding. The results were dramatically different to the failures from the previous batch. The layer-to-layer alignment was much better, pretty close to perfect!
On to experiment 2. I added some coupons to the panel layout to allow me to non-destructively assess the layer-to-layer movement inside the panels. This time I cut up the complete panel but marked which position the core came from in the manufacturing sheet. This time when the panels were bonded, each PCB was made from matched cores which all came from the same part of the full sheet. The results were not as good as the previous 10 panels but they were still pretty consistent. This time I was able to note that the highest levels of movement came from the corners of the original sheets.
I tried the same test on materials from a few different manufacturers and the results were interesting. All of the materials were standard FR-4 type materials but some were a lot less stable than others and the layer movement was much larger. Always the corners of the full sheets moved the most and always in a predictable direction.
At this point I started to get my production material from the supplier who performed best in the tests. We could not afford to make all our panels from the centre of the full sheets but I did use this tactic occasionally on some very high value products with a high level of success.
My next technical rep coffee meeting was a discussion of why the thin materials move so much. There was talk about the glass type and thickness and the way that dissimilar glass cloths don’t always work well together. The 0.8 mm material was a 7628 style but the 0.36 and 0.25 mm materials were not. At this stage I had got the supplier interested enough to offer to make me some base material with the 0.36 and 0.25 mm material also using the more stable 7628 glass cloth. The 0.25 mm material was difficult as the natural thickness of 7628 was 0.18mm when pressed—they did their best to raise the thickness and we managed to keep all cores within the allowed tolerance. I also manged to change all the prepreg at stack-up to 7628 style and still stay within the separation tolerance. The results were dramatically better. I still matched the cores at the build-up stage and we made several production batches with yields between 97 and 100%. The losses were all at innerlayer stage before bonding. I am pretty sure that when the weave of the glass cloth matches it helps stabilise the position throughout the stack. There is an interlocking effect, a little like Lego bricks, which greatly helps stability.
More modern welded or riveted tooling methods may reduce some of the issues involved in manufacture of this type of product. The possible advantage of material matching still applies though. Potentially you can remove a lot of the internal stress and improve the reliability of layer-to-layer alignment by careful use of your base materials.
I put a lot of effort into my investigation but it paid back again and again. I asked our design department to consider the glass style and to match it throughout the product wherever possible. When your back is to the wall with a tough design, it may be enough to get you to the finish line.
Marc Ladle is director at Viking Test Ltd.
Suggested Items
From DuPont to Qnity: A Bold Move in Electronics Materials
05/14/2025 | Marcy LaRont, I-Connect007DuPont has announced the intended spinoff of a public independent electronics company, Qnity, which will serve as a solutions provider to the semiconductor and electronics industries to enhance competitiveness and innovation in advanced computing, smart technologies, and connectivity. In this interview, Jon Kemp, Qnity CEO-elect and current president of DuPont’s Electronics business, shares his insights on the strategic separation from DuPont.
SMC Korea 2025 to Spotlight Next-Generation Memory and Materials Innovation amid AI Boom
05/13/2025 | SEMIThe Strategic Materials Conference (SMC) Korea 2025 is set to convene on May 14 at the Suwon Convention Center in Gyeonggi-do, South Korea, bringing together leading experts and innovators to highlight the critical role of materials innovation in addressing the performance, efficiency, and scalability requirements of AI-enabled semiconductor devices.
SEMI Applauds New Bill to Clarify Tax Credit Eligibility for Critical Semiconductor Suppliers Under U.S. CHIPS Act
05/12/2025 | SEMISEMI, the industry association serving the global semiconductor and electronics design and manufacturing supply chain, announced support of the Strengthening Essential Manufacturing and Industrial Investment Act (SEMI Investment Act), which clarifies that critical materials suppliers to semiconductor manufacturers are eligible for the Advanced Manufacturing Investment Tax Credit (“Section 48D”) created by the United States CHIPS and Science Act.
Taiwan's PCB Industry Chain Is Expected to Grow Steadily by 5.8% Annually in 2025
05/05/2025 | TPCAAccording to an analysis report jointly released by the Taiwan Printed Circuit Association (TPCA) and the Industrial Technology Research Institute's International Industrial Science Institute, the total output value of Taiwan's printed circuit (PCB) industry chain will reach NT$1.22 trillion in 2024, with an annual growth rate of 8.1%.
New Database of Materials Accelerates Electronics Innovation
05/05/2025 | ACN NewswireIn a collaboration between Murata Manufacturing Co., Ltd., and the National Institute for Materials Science (NIMS), researchers have built a comprehensive new database of dielectric material properties curated from thousands of scientific papers.