Building a Better Microbial Fuel Cell—Using Paper
February 6, 2017 | University of RochesterEstimated reading time: 1 minute
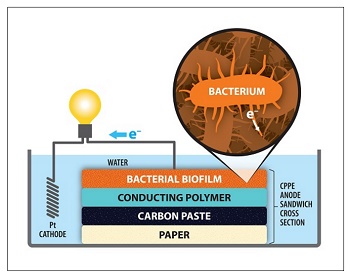
The concept behind microbial fuel cells, which rely on bacteria to generate an electrical current, is more than a century old. But turning that concept into a usable tool has been a long process. Microbial fuel cells, or MFCs, are more promising today than ever, but before their adoption can become widespread, they need to be both cheaper and more efficient.
A schematic illustration of a bioelectrochemical cell incorporating carbon paste paper electrodes. (University illustration / Michael Osadciw)
Researchers at the University of Rochester have made significant progress toward those ends. In a fuel cell that relies on bacteria found in wastewater, Kara Bren, a professor of chemistry, and Peter Lamberg, a postdoctoral fellow, have developed an electrode using a common household material: paper.
Until now, most electrodes used in wastewater have consisted of metal (which rapidly corrodes) or carbon felt. While the latter is the less expensive alternative, carbon felt is porous and prone to clogging.
Their solution was to replace the carbon felt with paper coated with carbon paste, which is a simple mixture of graphite and mineral oil. The carbon paste-paper electrode is not only cost-effective and easy to prepare; it also outperforms carbon felt.
“The paper electrode has more than twice the current density than the felt model,” says Bren.
Carbon paste is an essential ingredient due to its role in attracting electrons emitted by the bacteria. The specific bacterium used in Bren’s project was Shewanella oneidensis MR-1, which consumes toxic heavy metal ions in the wastewater and ejects electrons. Those electrons are attracted to the carbon coating on the positive electrode—the anode. From there, they flow to the platinum cathode, which needs electrons to carry out its own electrochemical reactions.
In making their electrode, Bren and Lamberg created a layered sandwich of paper, carbon paste, a conducting polymer, and a film of the bacteria. This easily constructed electrode, surprisingly, had an average output of the circuit of 2.24 A m-2 (amps per unit area), compared to 0.94 A m-2 with the felt anode.
“We’ve come up with an electrode that’s simple, inexpensive, and more efficient,” says Lamberg. “As a result, it will be easy to modify it for further study and applications in the future.”
Suggested Items
Intervala Hosts Employee Car and Motorcycle Show, Benefit Nonprofits
08/27/2024 | IntervalaIntervala hosted an employee car and motorcycle show, aptly named the Vala-Cruise and it was a roaring success! Employees had the chance to show off their prized wheels, and it was incredible to see the variety and passion on display.
KIC Honored with IPC Recognition for 25 Years of Membership and Contributions to Electronics Manufacturing Industry
06/24/2024 | KICKIC, a renowned pioneer in thermal process and temperature measurement solutions for electronics manufacturing, is proud to announce that it has been recognized by IPC for 25 years of membership and significant contributions to electronics manufacturing.
Boeing Starliner Spacecraft Completes Successful Crewed Docking with International Space Station
06/07/2024 | BoeingNASA astronauts Barry "Butch" Wilmore and Sunita "Suni" Williams successfully docked Boeing's Starliner spacecraft to the International Space Station (ISS), about 26 hours after launching from Cape Canaveral Space Force Station.
KIC’s Miles Moreau to Present Profiling Basics and Best Practices at SMTA Wisconsin Chapter PCBA Profile Workshop
01/25/2024 | KICKIC, a renowned pioneer in thermal process and temperature measurement solutions for electronics manufacturing, announces that Miles Moreau, General Manager, will be a featured speaker at the SMTA Wisconsin Chapter In-Person PCBA Profile Workshop.
The Drive Toward UHDI and Substrates
09/20/2023 | I-Connect007 Editorial TeamPanasonic’s Darren Hitchcock spoke with the I-Connect007 Editorial Team on the complexities of moving toward ultra HDI manufacturing. As we learn in this conversation, the number of shifting constraints relative to traditional PCB fabrication is quite large and can sometimes conflict with each other.