Weiner’s World—January 2017
February 9, 2017 | Gene Weiner, Weiner International Inc.Estimated reading time: 7 minutes
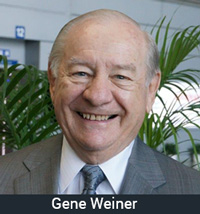
Editor’s note: This blog was originally published in January 2017 (click here) and is being reprinted here with special permission from the author.
This month’s column is a bit shorter than usual as we prepare for next month’s IPC APEX EXPO and its Executive Forum for PCB fabricators and their supply chain.
This month also marks the 65th anniversary of Epec LLC in New Bedford, Massachusetts. The company, founded in 1952, is the oldest printed circuit fabricator in North America. Half of its $50 million in sales is reported to be with printed circuits. I well remember as a rookie technical salesman for Shipley Company Inc. calling on Dick Zens, the company’s president, in 1956-7. Dick went on to become one of the founders of IPC in 1957 along with other former friends and customers of yore: Al Hughes, Bill McGinley, and Bob Swiggett.
I am reminded by this anniversary of other iconic pioneers of our industry's beginnings. Starting with the late Dieter Bergman they include Bob Rennie, Dale Messerschmidt, Hy Almond, Pete & Sandy Pellegrino, Jim Penney, Ross Sibley, Tad Navoy, Peter Sarmanian, Charlie Shipley, George Hart, Rufus Benton, Spence Glaspell, Dr. Harold Narcus, Herb Pollack, Jim Donaghy, Foster Gray, Paul Goldman, Bob Rennie, Rolly Mettler, Dick Douglas, Bert Krasnow, Bill Jacobi, Marv Larson, Denny Stalzer, George Morse, Sam Altschuler, George Messner, Howard Manko, Bert Isaacson, Irv Ireland, Dimitry Grabbe, Jerry Shore, Al Weiss, Jim Carlson, Larry Velie, Jerry Siegmund, Ivan Jones, Dave Radovsky, Gerry Lordi, Dr. J. Lee Parker, Werner Engelmeier, Don Dinella, Gerry Ginsberg, Bill DeForest, Bill Rothschild, Bernie Alzua, Arnold Fleury, Joe Canizero, Lincoln Low, Clyde Combes, Jerry Henrikson, Bill Parker, Stark Roberts, Hugh Medford and scores of others—to name a few....and do not forget Ray Pritchard! How many do you recall?
I still communicate frequently with the first chairman of the IPC's TAEC committee. Can you guess who he is? I'll give you a hint. He is a member of IPC's Raymond E. Pritchard Hall of Fame. Still don't know? He is the most senior of the IPC Ambassadors. Still wondering? Here's another hint: He is one of the first recipients of the Dieter Bergman Fellowship Awards—an IPC Fellow! Give up? It is Bernie Kessler! Come say hello to him at the San Diego event!
Dept. of Commerce to Make Special Presentation at IPC’s PCB Executive Forum at IPC APEX EXPO
Experts from the U.S. Department of Commerce—Office of Technology Evaluation with the Bureau of Industry and Security—will present a report at the PCB Executive Forum in San Diego on February 13. The presentation is an analysis of industrial sectors supporting U.S. defense programs and critical infrastructure: Can they meet our economic and national security requirements? This study includes interesting information that will provide perspective for your business forecasting. It is expected to also include some interesting information on “trusted sources.”
We are also watching what changes or support our industry will get from the new administration. How will our government support rebuilding or solidifying our remaining printed circuit industry? Does it recognize its position in national defense? Do our members of Congress maintain members on their staffs that can understand the industry and its role in the defense, health, and the automotive industries?
Will the diverse agencies and laboratories of Army, Air Force and Navy cooperate, share information, find common areas of need, and share common successes and data? Will they share their information with the Department of Commerce? Will the DOC reciprocate? Are they looking too far ahead (e.g., to electronic systems for 2030 and 2040) to pay attention to issues with today’s PCB platforms? Do they think that there is no problem in securing domestic PCBs? Have they drilled down deeply enough to recognize that a common but critical material—copper foil—is no longer produced in the U.S. except for one facility that is owned by a Japanese company?
One industry icon says, “On advancing PCB technology and performance per se, I think the shortest linkage from the industry to the government agencies is NIST.”
IPC President and CEO John Mitchell has been elected to serve on the National Association of Manufacturers’ (NAM) Council of Manufacturing Associations (CMA) Board of Directors. The Council of Manufacturing Associations is made up of more than 260 manufacturing trade associations that work together on behalf of manufacturing in the United States.
TTM Technologies celebrated the grand opening of its RF (radio frequency) Center of Excellence in Stafford Springs, CT with government officials, TTM leaders, employees and guests participating in a ribbon cutting ceremony. This RF center of excellence in Stafford Springs specializes in RF-related PCB products to better support Aerospace & Defense as well as other customers.
Taiwan Makers Ship More Than 61 million Large-size TFT-LCD Panels in 4Q16
Taiwan-based makers shipped a total of 61.37 million large-size (9-inch and above) TFT-LCD panels during the fourth quarter of 2016, decreasing 1.5% on quarter but increasing 2% on year, according to Digitimes Research. TV panels accounted for 30% of shipments, notebook-use units for 31.6%, LCD monitor-use units 21.1% and tablet-use units 14.3%.
Innolux shipped 11.18 million TV panels, 10.25 million notebook-use units, 5.99 million monitor-use units and 2.49 million tablet-use units. AU Optronics shipped 7.21 million TV panels, 9.17 million notebook-use units, 6.97 million monitor-use units and 3.37 million tablet-use units. Chunghwa Picture Tubes and HannStar Display shipped 2.51 million and 380,000 tablet-use panels.
Taiwan's large size TFT-LCD display shipments in 2016 declined 2.3% for the year (Digitimes Research).
Toshiba to Sell Most of its Chip Operations
Toshiba has decided to sell most of its semiconductor chip operations to focus on its flash memory business. The operations to be put up for sale include the division that handles system large-scale integrated circuits, which are used in a wide range of products including automobiles and home appliances. Toshiba hopes to rebuild its image by concentrating on flash memory, which has been a cash cow for the struggling company. A tender has already started for some of the chip operations it plans to sell, according to sources.
Toshiba plans to build a new flash memory plant with the U.S. chipmaker SanDisk on a site next to its existing plant in Yokkaichi, Mie Prefecture. The cost, to be split between the firms, will exceed $3.4 billion. The company has already announced plans to stop making white LEDs and CMOS image sensors, with the latter business to be sold to Sony (Japan Times).
Guess Who?
In case you missed this last month, it seems that a "very populous country" with half the circuit board manufacturing capacity in the world has vowed to spend up to $200 billion to buy their way into world semiconductor leadership.
China’s state-backed National IC Investment Fund is to shift its investment focus to the Chinese chip designing sector from the chip manufacturing sector. The fund has committed to investing about $10B in China’s semiconductor industry since its creation first year. About 60% of the investments have been allocated to building semiconductor wafer fabs.
Thus, China’s 12-inch wafer capacity is expected to surge from 373,000 wafers per year to 620,000 wafers per year over the next three years. The fund is to shift its focus to China’s fabless chip design and chip packaging and testing sectors from chip manufacturing, and would also inject capital into Chinese design houses to improve their innovative capabilities and to help them clinch overseas merger-and-acquisition deals (Taipei Times).
China’s economic growth for 2016 was 6.7%, the target range of between 6.5% and 7%.
Apple is said to be considering moving some of its iPhone production to the United States. Taiwanese iPhone producer Foxconn is considering a $7 billion joint investment in a display production facility, the company’s chairman told reporters. Apple has a “ton” of offshore money that could be repatriated for new facility investment if tax rates are lowered. According to the Nikkei Asian Review, Foxconn Chairman Terry Gou said “Apple is willing to invest in the facility together…” with his company because it needs display panels for its products. The plant could create 30,000 to 50,000 jobs.
But Gou said U.S.-made iPhones would likely cost more than those produced at Foxconn’s Zhengzhou, China facility, which churns out more than 100 million iPhones per year. “In the future, they may be paying some $500 more for U.S. products, but those do not necessarily work better than a $300 phone,” Gou told reporters.
Note: This last statement by Gou, coupled with past performance of not going forward with a number of announced facilities in various parts of the world, is why I have a “wait and see” attitude about future Foxconn plants.
Suggested Items
RF PCB Design Tips and Tricks
05/08/2025 | Cherie Litson, EPTAC MIT CID/CID+There are many great books, videos, and information online about designing PCBs for RF circuits. A few of my favorite RF sources are Hans Rosenberg, Stephen Chavez, and Rick Hartley, but there are many more. These PCB design engineers have a very good perspective on what it takes to take an RF design from schematic concept to PCB layout.
Trouble in Your Tank: Causes of Plating Voids, Pre-electroless Copper
05/09/2025 | Michael Carano -- Column: Trouble in Your TankIn the business of printed circuit fabrication, yield-reducing and costly defects can easily catch even the most seasoned engineers and production personnel off guard. In this month’s column, I’ll investigate copper plating voids with their genesis in the pre-plating process steps.
Elephantech: For a Greener Tomorrow
04/16/2025 | Marcy LaRont, PCB007 MagazineNobuhiko Okamoto is the global sales and marketing manager for Elephantech Inc., a Japanese startup with a vision to make electronics more sustainable. The company is developing a metal inkjet technology that can print directly on the substrate and then give it a copper thickness by plating. In this interview, he discusses this novel technology's environmental advantages, as well as its potential benefits for the PCB manufacturing and semiconductor packaging segments.
Trouble in Your Tank: Organic Addition Agents in Electrolytic Copper Plating
04/15/2025 | Michael Carano -- Column: Trouble in Your TankThere are numerous factors at play in the science of electroplating or, as most often called, electrolytic plating. One critical element is the use of organic addition agents and their role in copper plating. The function and use of these chemical compounds will be explored in more detail.
IDTechEx Highlights Recyclable Materials for PCBs
04/10/2025 | IDTechExConventional printed circuit board (PCB) manufacturing is wasteful, harmful to the environment and energy intensive. This can be mitigated by the implementation of new recyclable materials and technologies, which have the potential to revolutionize electronics manufacturing.