Secure Wireless Chargers
February 9, 2017 | MITEstimated reading time: 4 minutes
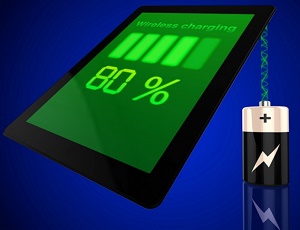
Counterfeit chargers for portable electronics are a major problem. At the end of 2016, Apple claimed that of 100 Apple-branded charging accessories it bought on Amazon, 90 were counterfeits. Around the same time, Britain’s Chartered Trading Standards Institute reported that of 400 counterfeit chargers it bought from a range of online retailers, 397 failed a basic safety test.
In the last few years, portable electronics that can be recharged wirelessly have started coming to market. In an effort to get ahead of the problem of counterfeit wireless chargers — which could cause power surges that fry a device’s circuitry — researchers from MIT’s Microsystems Technology Laboratories have built a chip that blocks attempts to wirelessly charge a device’s battery unless the charger first provides cryptographic authentication.
The same technology also solves another problem with wireless chargers. When two devices share a single charger, if they are different distances from the charger’s electrical coil, their charging rates can vary enormously, to the extent that one device might charge fully while the other remains virtually uncharged. In the same way that the researchers’ chip can block power transfer from an unauthorized charger, it can slow the power transfer to a device nearer the charging coil, ensuring more equitable charge rates.
“Security is one of the most critical issues in the ‘internet of things [IoT],’” says Anantha Chandrakasan, the Vannevar Bush Professor of Electrical Engineering and Computer Science, referring to the popular idea that vehicles, appliances, civil-engineering structures, manufacturing equipment, and even livestock will soon have sensors that report information directly to networked servers. “We will see security functionality embedded into virtually every function and component of an IoT node.”
The researchers presented the new chip this week at the International Solid-State Circuits Conference. Chandrakasan is the senior author on the conference paper, and the first author is Nachiket Desai, who was an MIT graduate student in electrical engineering and computer science (EECS) when the work was done. They’re joined by Chiraag Juvekar, also an EECS graduate student at MIT, and Shubham Chandak, a graduate student in electrical engineering at Stanford University.
Switched out
In a wireless charging system, both the charger and the target device contain metal coils. An alternating current — an electrical current that changes direction at a regular rate — passing through the charger’s coil produces a magnetic field, which induces a current in the device’s coil. The rate at which the current in the charger alternates defines a frequency, much like the frequency of a radio transmission. The device’s coil must be “tuned” to the transmission frequency in order to receive power.
The MIT researchers’ chief innovation is a more compact and efficient circuit for tuning the frequency of the receiving coil. A standard tuning circuit connects the coil to a series of capacitors, electronic components that can store charge. Between each pair of capacitors is a switch, and switching capacitors on and off changes the receiver’s frequency.
“Those switches have very severe requirements,” Juvekar says. “They either have to block a very large voltage when they’re off, or they have to carry a very large current when they’re on, or in some cases both. If a switch needs to block a very big voltage, then it’s very hard to put that on the chip. So it has to be a discrete component on the [circuit] board, outside the chip. Or if it’s on the chip, it requires a specialized [manufacturing] process that might be very expensive.”
Instead of a single coil attached to a bank of capacitors, the MIT researchers’ design uses a pair of coils attached to one capacitor each — no switches required. “The fact that those switches aren’t there anymore is a big advantage,” Juvekar says.
Tuned in
In the researchers’ chip, one of the coils — the main coil — is much larger than the other — the auxiliary coil. The main coil carries the chief responsibility for charging a device’s battery. When a current is flowing through the auxiliary coil, it produces a magnetic field that changes the tuning frequency of the main coil.
In the circuit connected to the auxiliary coil, the resistance — the efficiency with which it conducts electricity — can be continuously varied. When the resistance is low, the auxiliary coil produces a strong magnetic field, which changes the main coil’s tuning frequency so drastically that charging is impossible.
When the resistance in the auxiliary coil’s circuit is higher, the magnetic field is weaker, and the detuning is less drastic. Some power transfer will still occur, but the charge rate is lower. That permits other, more distant devices to harvest more of the power transmitted by the charger coil.
The chip uses an authentication technique called elliptic curve cryptography, which is a “public-key” cryptographic technique. Using publicly available information, the chip can generate — and verify the response to — a question that only a charger with valid private information can answer. The chip doesn’t need to store a secret key of its own.
Elliptic curve cryptography is a well-established technique. But Chandrakasan’s group has developed a battery of methods for reducing chips’ power consumption, and the researchers found a way to simplify the encryption circuit so that it takes up less space on the chip and consumes less power.
“This paper describes an innovative approach to accurately and securely managing more than one wireless charging load,” says Baher Haroun, director of signal-path research at Texas Instruments’ Kilby Labs. “The need for security in wireless energy distribution is critical to ensure authorized and efficient use of the energy delivered. This work could have benefits for safety but also for [determining] ‘Who is a legitimate user for this delivered energy?’”
Suggested Items
Alternative Manufacturing Inc. (AMI) Appoints Gregory Picard New Business Development Manager
05/01/2025 | Alternative Manufacturing, Inc.Alternative Manufacturing Inc. (AMI) is pleased to announce the appointment of Mr. Gregory Picard as our new Business Development Manager. Picard brings a wealth of experience in Sales and Business Development, having worked with some of the most prominent names in the industry.
Elephantech, Logitech Together Drive Disruptive Electronics Innovation
05/01/2025 | ElephantechElephantech Inc. announced a groundbreaking collaboration with Logitech International to revolutionize peripherals manufacturing and the printed circuit board (PCB) industry.
A Visit With ‘Flexperts’ Mark Finstad and Nick Koop
05/01/2025 | Joe Fjelstad, Verdant ElectronicsAt IPC APEX EXPO 2025, I chatted with seasoned flex experts Mark Finstad and Nick Koop about "Flexperts" and their roles as leading educators and in the realm of standards development for this increasingly indispensable electronic interconnection technology. They have been teaching about lessons learned and how to successfully navigate the “seas” of flexible circuits to help their students avoid the hazards that have taken down many of their predecessors in the past.
Ensuring a Strong and Reliable Supply Chain
04/30/2025 | Marcy LaRont, PCB007 MagazineKelly Davidson, vice president of NCAB Group USA, discusses the company's stable performance in 2024 and positive outlook for 2025. She highlights NCAB's strategy of organic growth and strategic acquisitions amidst tariff concerns and global political uncertainty. Kelly emphasizes the importance of supply chain diversification, strong supplier relationships, and customer education, and notes NCAB's focus on defense production and maintaining a reliable supply chain.
Choosing the Right Strategic Path
04/29/2025 | Marcy LaRont, PCB007 MagazineTom Yang, CEO of CEE PCB, discusses the current economic challenges, noting reduced purchasing power post-pandemic. He highlights the growing demand for HDI in consumer electronics due to AI growth. Tom also expresses concerns about tariffs under the new U.S. administration, prompting CEE to diversify production locations, including new plants in Southeast Asia. He emphasizes the need for PCB manufacturers to adapt strategically amidst rising costs and fierce competition, particularly for mid-sized shops facing unique challenges in the industry.