-
- News
- Books
Featured Books
- pcb007 Magazine
Latest Issues
Current IssueInventing the Future with SEL
Two years after launching its state-of-the-art PCB facility, SEL shares lessons in vision, execution, and innovation, plus insights from industry icons and technology leaders shaping the future of PCB fabrication.
Sales: From Pitch to PO
From the first cold call to finally receiving that first purchase order, the July PCB007 Magazine breaks down some critical parts of the sales stack. To up your sales game, read on!
The Hole Truth: Via Integrity in an HDI World
From the drilled hole to registration across multiple sequential lamination cycles, to the quality of your copper plating, via reliability in an HDI world is becoming an ever-greater challenge. This month we look at “The Hole Truth,” from creating the “perfect” via to how you can assure via quality and reliability, the first time, every time.
- Articles
- Columns
- Links
- Media kit
||| MENU - pcb007 Magazine
Estimated reading time: 4 minutes
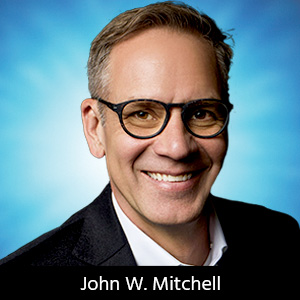
One World, One Industry: Emerging Technology, Training for the Future, and the Next Industrial Revolution
Technology isn’t just a tangible entity. It moves beyond what we can see, feel, and touch. It is ideas and theories. It includes philosophy and risks. In a way, technology itself is like the stock market. Different industries hedge their bets on emerging trends. These trends develop into useful products that change our world. It isn’t just enough to simply guess where a new technology may fit, or how emerging technologies will advance the industry. You must understand how the ebbs and flows will impact your business, and how new technologies will leverage against existing systems.
So, to be successful, we need to do our best to first spot trends in the industry, and understand how these trends point to a paradigm shift in the way we operate. You see, every few years, technology finds a way to revolutionize the entire manufacturing process. Dating back to the first Industrial Revolution, when manufacturing started to move from hand production to steam power, there was a great shift in how manufacturing impacted the economy. From there, the utilization of electric power to create mass production, and then the usage of electronics to automate has opened the door for where we are today.
We are on the doorstep of the fourth great revolution in manufacturing, which has put an emphasis on connecting the factory, the workforce, and the end-user. It is this connected factory and the Industrial Internet of Things (IIOT) that has created never-before-seen opportunities to include new technologies ranging from robotics to 3D printing.
But as technologies continue to advance so quickly, some may find it difficult to anticipate what comes next. Just because there are new technologies doesn’t mean you should be complacent with new improvements. Even the best-connected factory today will experience shifts in production down the road. Adjusting is more than a single upgrade. It is creating a dynamic environment that can adapt to fluctuations today, while adjusting to include emerging technologies tomorrow.
And one of the best ways to ensure that we are adaptable to all coming technologies is to make sure our workforce is competitive. As during previous Industrial Revolutions, the economy is expected to grow. This indicates a growth in jobs as well. But to truly grow, manufacturers need to reinvest not only in innovation, but in employees. Now is the time to focus on training employees on new technologies. A report on advanced manufacturing[1] released in 2016 by the Subcommittee for Advanced Manufacturing of the National Science and Technology Council stated that, “Over the next decade, we will need to fill nearly 3.5 million manufacturing jobs, although two million of these positions may remain unfilled due to a skills gap. In fact, at this moment, 80% of manufacturers currently report a moderate or serious shortage of qualified applicants for skilled and highly-skilled production positions.”
Much like when Henry Ford rolled out the assembly line, there is a push for workers to further hone and specialize their skills. The result of this is reduced waste, and a higher quality end-product. Investing in new technologies may require funds up front, but this is worth it when you consider the reduction in assembly time and the increase in production rate. So, it isn’t enough to simply adopt these technologies, but rather adopt a shift that includes training and preparing a workforce that can handle current technologies and be adaptable to adjust to whatever may come down the road.
In the end, the technology we have today comes as the result of hardworking individuals. Sure, Ford made great strides to advance the way factories produced goods in 1914. But he also put an emphasis on his employees, ensuring they knew how to operate the machines that would change the world. Thus, he produced quality automobiles and revolutionized the American class of blue collar workers.
While the digitization of our factories is a great example of improving production while decreasing waste, there needs to be a focus on ensuring the employees can operate machines across the entire connected factory floor and train others to do the same. Much like IPC’s Connected Factory Initiative states, it is important to establish a baseline of communication to achieve Industry 4.0 benefits. For “plug and play interoperability” of devices to succeed, employees need to be able to understand and utilize the technology.
Until the fifth Industrial Revolution comes, we will need to innovate our processes and uncover new ways to make today’s systems work better. Manufacturing will continue to grow in the United States and across the globe, but it will require a concerted effort to learn, adapt, integrate, and evolve.
References
1. Advanced Manufacturing: A Snapshot of Priority Technology Areas
John Mitchell is president and CEO of IPC—Association Connecting Electronics Industries. To read past columns or to contact Mitchell, click here.
Editor's Note: This article originally appeared in the February 2017 issue of The PCB Magazine.
More Columns from One World, One Industry
One World, One Industry: IPC APEX EXPO 2025 Marks a Special Anniversary YearOne World, One Industry: Mapping the Future of the Electronics Workforce
One World, One Industry: Mastering Technology Prognostication
One World, One Industry: To Thrive, Surround Yourself with Good People
One World, One Industry: Sustainability Challenges—A Collaborative Approach
One World, One Industry: What’s Next Becomes Now at IPC APEX EXPO 2024
One World, One Industry: ‘Blocking and Tackling’ During Tough Economic Times
One World, One Industry: Developing Your Team to Become Great Implementors