Patty's Perspective: New Technology Heading our Way— Faster than Ever!
February 21, 2017 | Patty Goldman, I-Connect007Estimated reading time: 5 minutes
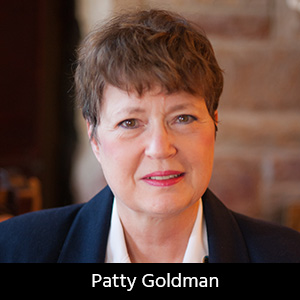
Way back when, in the early 1980s, I worked for a small PCB manufacturer in Danbury, Connecticut. We all loved new stuff, as in nobody wanted to make normal PCBs—just crazy impossible stuff. We did full panel soft gold (for wire bonding); we made about 90% of the first circuits (all gold-plated) that went in the early digital watches (for TI and Timex); we worked with Ohmega material and embedded resistors; we were making 5-mil line/space innerlayers in volume for IBM and even prototyped a 2-mil line/space multilayer (this was more than 30 years ago, mind you); we made the first (or darn close to the first) polyimide gold-plated chip-on-board multilayers to which something like 42 chips were gold wire-bonded (HP). Talk about new technology—we were deep into it!
And now, have we seen or done it all? Not even close! As technology moves faster and faster, so do our equipment, materials and chemistry suppliers to help us to enable that next greatest invention. We are all at the forefront of IoT, the fifth industrial revolution, autonomous and connected—everything, all those things that were unimaginable even 10 years ago. It’s hard work, there is no sitting back or relaxing, and those looking for an easy 9-to-5 job, forget about it. Are you ready for the next thing, to keep pushing forward?
As an excellent introduction to this issue, IPC’s John Mitchell gives us a wonderful overview of what emerging technology is and what we need to do to keep up. One thing he emphasizes is a trained and competitive workforce. Indeed, in our recent hiring survey we learned that an overwhelming percentage of you are concerned about a shortage of skilled and qualified people. John’s column is a great call to action.
Next, we have a very intriguing interview with Joan Tourné of NextGIn Technology BV, conducted by I-Connect007’s Pete Starkey. Joan talks about a new interconnect technology he calls “vertical conductive structures” or VeCS.
With VeCS one can achieve much higher interconnect density using existing equipment and processes. He talks of cost reductions associated with reduced material usage and provides an interesting illustration of this novel technique.
Apparently one of the most significant new technologies these days is jet printing solder mask. You may say, “Inkjet? Not new. Soldermask? Not new.” But put them together and the challenges are huge and the technology is right on the cutting edge. As such, we bring you several articles and interviews on this very subject.
Henk Goossens of Meyer Burger BV in The Netherlands provides a wonderful introduction to the thorny subject of direct digital inkjetting of soldermask. Removing steps like artwork generation, developing, and waste treatment, and reducing materials and process time, all equals to cost savings…of course we want to inkjet. Henk gives us a great view of the subject from the equipment perspective.
We have two interviews conducted by Publisher Barry Matties that explore the material/equipment partnership between Taiyo and Schmoll to develop an inkjet soldermask that is compatible with the inkjet machine. Dick Crowe of Burkle (U.S. distributor for Schmoll) contributed an excellent introduction. The first interview is with Taiyo’s John Fix, with Walt Custer of Custer Consulting, contributing. The second is an interview with Schmoll’s Thomas Kunz, who discusses not just the partnership but the technology, working with OEMs, and more.
Barry Matties and Pete Starkey bring us an interview with Agfa’s Frank Louwet, who explains Agfa’s partnerhsip with Electro Polymers to develop a nanoparticle ink. One can learn a great deal about the soldermask inks and the inkjet process from these interviews.
EIPC’s Alun Morgan gives us a great report on their recent workshop on PCB BioMEMS—aka PCB-on-a-chip. With a CAGR of greater than 25%, BioMEMS devices are a definite market of interest. This detailed article provides a wealth of information on the subject and certainly should be required reading for anyone involved in PCB fabrication.
Steve Williams of Right Approach Consulting takes us far away from soldermask to a look at the new Trump administration and what its promises may mean to our industry and business in general. He even includes a “Top Ten” on deregulation. Read on!
Back to some technical content with Michael Carano, of RBP Chemical Technology, as he delves into the metallizing difficult-to-plate substrates, in this case with electroless copper. Mike always includes some troubleshooting info as well as much practical advice in his columns.
Next, NTI’s Keith Sellers discusses various test methods to ensure that your incoming (or outgoing) PCBs perform as intended and that you “get what you pay for.” He proceeds from the basic incoming inspection through more in-depth analysis involving cross-sections, thermal stress testing and more, including some additional ones to determine basic laminate properties and suitability for the job at hand.
And finally, in his usual inimitable fashion is Barry Lee Cohen of Launch Communications. Each month Barry provides another piece to the marketing communications puzzle. This time his subject is e-newsletters and always worth a read, not to mention a commitment to followthrough.
And so you have it—our line-up for February. Lots of good new tech stuff to keep the wheels turning upstairs, plus some immediate things you can put into practice today or tomorrow at the latest. Next month our subject is “The Wide World of Flex.” Do tune in and read about all things flex—from the various types to the materials to the processing of same. We promise another issue of cover-to-cover value. If you haven’t yet subscribed, do so right now and be one of the first to get it in your e-mailbox.
Patricia Goldman is a 30+ year veteran of the PCB industry, with experience in a variety of areas, including R&D of imaging technologies, wet process engineering, and sales and marketing of PWB chemistry. Active with IPC since 1981, Goldman has chaired numerous committees and served as TAEC chairman, and is also the co-author of numerous technical papers. To contact Goldman, click here.
This article originally appeared in the February 2017 issue of The PCB Magazine.
Testimonial
"The I-Connect007 team is outstanding—kind, responsive, and a true marketing partner. Their design team created fresh, eye-catching ads, and their editorial support polished our content to let our brand shine. Thank you all! "
Sweeney Ng - CEE PCBSuggested Items
Indium Corporation Promotes Two Leaders in EMEA (Europe, Middle East, and Africa) Markets
08/05/2025 | Indium CorporationWith its commitment to innovation and growth through employee development, Indium Corporation today announced the promotions of Andy Seager to Associate Director, Continental Sales (EMEA), and Karthik Vijay to Senior Technical Manager (EMEA). These advancements reflect their contributions to the company’s continued innovative efforts with customers across Europe, the Middle East, and Africa (EMEA).
MacDermid Alpha Electronics Solutions Unveils Unified Global Website to Deepen Customer, Talent, and Stakeholder Engagement
07/31/2025 | MacDermid Alpha Electronics SolutionsMacDermid Alpha Electronics Solutions, the electronics business of Elements Solutions Inc, today launched macdermidalpha.com - a unified global website built to deepen digital engagement. The launch marks a significant milestone in the business’ ongoing commitment to delivering more meaningful, interactive, and impactful experiences for its customers, talent, and stakeholders worldwide.
KOKI to Showcase Analytical Services and New HF1200 Solder Paste at SMTA Guadalajara 2025
07/31/2025 | KOKIKOKI, a global leader in advanced soldering materials and process optimization services, will exhibit at the SMTA Guadalajara Expo & Tech Forum, taking place September 17 & 18, 2025 at Expo Guadalajara, Salón Jalisco Halls D & E in Guadalajara, Mexico.
Weller Tools Supports Future Talent with Exclusive Donation to SMTA Michigan Student Soldering Competition
07/23/2025 | Weller ToolsWeller Tools, the industry leader in hand soldering solutions, is proud to announce its support of the upcoming SMTA Michigan Expo & Tech Forum by donating a limited-edition 80th Anniversary Black Soldering Set to the event’s student soldering competition.
Koh Young Appoints Tom Hattori as President of Koh Young Japan
07/21/2025 | Koh YoungKoh Young Technology, the global leader in True 3D measurement-based inspection solutions, announced the appointment of Tom Hattori as President of Koh Young Japan (JKY).