-
- News
- Books
Featured Books
- pcb007 Magazine
Latest Issues
Current IssueInventing the Future with SEL
Two years after launching its state-of-the-art PCB facility, SEL shares lessons in vision, execution, and innovation, plus insights from industry icons and technology leaders shaping the future of PCB fabrication.
Sales: From Pitch to PO
From the first cold call to finally receiving that first purchase order, the July PCB007 Magazine breaks down some critical parts of the sales stack. To up your sales game, read on!
The Hole Truth: Via Integrity in an HDI World
From the drilled hole to registration across multiple sequential lamination cycles, to the quality of your copper plating, via reliability in an HDI world is becoming an ever-greater challenge. This month we look at “The Hole Truth,” from creating the “perfect” via to how you can assure via quality and reliability, the first time, every time.
- Articles
- Columns
- Links
- Media kit
||| MENU - pcb007 Magazine
Estimated reading time: 5 minutes
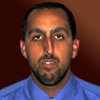
Let's Talk Testing: How Strong is Your Foundation?
In my December 2016 column, we discussed the idea of supplier surveillance and that one should put into place some type of doublecheck to ensure that you are getting exactly what you’ve asked for, designed, ordered, etc. To take that idea a step further and to circle it back to the main industry we are discussing here, let’s look at some of the testing that one might do under a supplier surveillance program as it relates to a standard printed circuit board—the foundation of most electronics in today’s world.
The most obvious and commonly performed first steps in testing on bare printed circuit boards are a combination of as-received visual examinations and cross-sectional evaluations via microsection analysis. From an equipment standpoint, the as-received visual examination needs only a simple stereomicroscope with magnification up to around 100x. In the as-received state, the printed circuit board can be inspected for various anomalies, such as those pertaining to conductor widths/spacings, plated through-hole/via hole construction, and surface contamination, just to name a few.
A more in-depth inspection can be accomplished through microsection analysis, whereas the printed circuit board will need to be diced, potted in an epoxy resin, and then ground and polished to specific vertical and/or horizontal planes of interest. For this inspection, internal board structures can be intimately inspected and measured to ensure that the board has been constructed as you’ve designed or specified. Potential anomalies that could affect reliability down the road could also be identified. Of course, the sample preparation and inspection techniques needed for this type of analysis are a bit more involved as microsection analysis is as much art as it is science and then some type of metallurgical scope will be needed for the actual inspection. For reference, to help guide you, documents such as IPC-A-600: Acceptability of Printed Boards[1] and IPC-6012: Qualification and Performance Specification for Rigid Printed Boards[2], are good guides for the good and the bad associated with printed circuit board constructions. Definitions of various industry terms are contained within, along with visual examples of acceptable and unacceptable structures.
A few additional tests that can be performed on incoming printed circuit board product include solderability and thermal stress analyses.
Solderability testing is just as it sounds and is performed to ensure that the metallic surfaces on a printed circuit board will wet with molten solder under standard test conditions. The test involves a commonly available soldering flux and a molten solder pot. A simple confirmation of whether the board can pass a solderability test, such as one called out in IPC-J-STD-003: Solderability Tests for Printed Boards[3], is a good place to start.
Thermal stress testing is also just as it sounds. A printed circuit board specimen is exposed to heat cycles via a molten solder pot to determine whether the board (and all its connections) can withstand the potential solder reflow cycles that the board might see during the assembly process yet to come. After exposure of the test sample to the solder reflow cycles, crosssectional samples are prepared, as described above when we discussed microsection analysis, for another evaluation of the internal board structures—this one after a stress event. For a guideline, IPC-TM-650, method 2.6.8: Thermal Stress, Plated-Through Holes[4] is a commonly utilized test for thermal stress analysis.
So far, the testing mentioned in this column has dealt mostly with the “structures” associated with printed circuit boards—traces, plated through-holes, via holes, etc. Although these aspects of printed circuit boards are clearly important and relevant, there is another aspect of the board’s construction that is equally as important, yet commonly overlooked. That aspect relates to the material which is used to physically construct the board, and its “structures”— the laminate. When designing and developing a printed circuit board, a laminate material is called out on the board’s drawing. The material is chosen for various reasons, such as glass transition temperature, thermal expansion capabilities, and delamination (or more specifically, lack-of-delamination) properties, just to name a few. To investigate these types of properties, one must call upon the use of thermal analysis test equipment. Of specific interest would be a differential scanning calorimeter (DSC) and a thermomechanical analyzer (TMA).
A DSC measures heat flow in or out of a test specimen as a function of time or temperature. Determining the glass transition temperature (Tg) of a board’s laminate material is a commonly monitored material parameter, as the Tg value is an important factor when selecting the laminate material for the board’s construction, due to the reflow profile that will be used during the board’s assembly process. At the same time, degree of cure—a property which sheds light on whether a printed circuit board was cured properly—is also commonly investigated as an incompletely cured board can lead to board population issues during the assembly process. As a guideline, one can use IPCTM-650, method 2.4.25: Glass Transition Temperature and Cure Factor by DSC[5] if interested in these properties.
A TMA measures distance change of a test specimen as a function of time or temperature. Although TMA can also be used to determine Tg, like DSC, it’s more generally used to measure thermal expansion-related properties. Like the DSC testing described above, board designers also use thermal expansion properties of the board when designing the board’s layout and when choosing the materials for the board’s construction. A commonly used test method for measuring these properties is IPC-TM-650, method 2.4.24: Glass Transition Temperature and Z-Axis Thermal Expansion by TMA[6]. In addition to measuring the specific thermal expansion values, obtaining information about the board’s ability to withstand delamination of its layers at elevated temperature can also be investigated via TMA. There is a group of test methods for this type of delamination testing, with IPC-TM-650, method 2.4.24.1: Time to Delamination (TMA Method)[7] the most commonly used.
Clearly, a variety of steps that can be taken to help ensure you’re getting what you paid for…and doing any testing is honestly better than doing none at all. PCB
References
1. IPC-A-600
2. IPC-6012
3. J-STD-003B
4. IPC-TM-650, method 2.6.8E
5. IPC-TM-650, method 2.4.25c
6. IPC-TM-650, method 2.4.24c
7. IPC-TM-650, 2.4.24.1
Keith M. Sellers is operations manager with NTS in Baltimore, Maryland. To read past columns or to contact Sellers, click here.
Editor's Note: This article originally appeared in the February 2017 issue of The PCB Magazzine.
More Columns from Let's Talk Testing
Let’s Talk Testing: Professor Plum in the Library with the Candlestick…Right?Random Thoughts on Employment, from Both Sides of the Table…
Let's Talk Testing: You’re in for a (Thermal) Shock!
Got Whiskers?
Let's Talk Testing: Are You Getting What You’ve Asked for?
Vias for Dummies
Don’t Reinvent the Wheel—Find an Expert!
Does your Product have a Military Application?