Rogers' John Ranieri Discusses 92ML Conductive Epoxy Materials for Power Electronics
March 10, 2017 | Real Time with...IPCEstimated reading time: 4 minutes
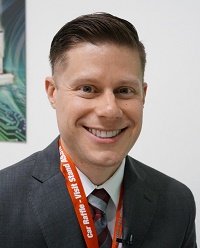
John Ranieri, Business Development Manager for Rogers Corporation, sat down for an interview with me at IPC APEX EXPO in San Diego. He discussed Rogers’ 92ML™ series of thermally conductive epoxy materials, and some of the challenges facing technologists in the power electronics market.
Judy Warner: John, very nice to see you again here at IPC APEX EXPO.
John Ranieri: Thank you, Judy.
Warner: For folks who don't know, just give us a quick overview of the laminate and circuit materials that Rogers manufactures.
Ranieri: Rogers is a global specialty materials manufacturer. We focus on engineered solutions for specific applications. I represent Rogers’ Advanced Connectivity Solutions, and we really focus on printed circuit board materials. That's laminate and prepreg materials that make up the substrate of the PCB. We've been a leader in the RF market space, and we're now working on moving into the power electronics market space as well.
Warner: Tell us what you're highlighting at this year’s show.
Ranieri: We're highlighting the 92ML series of thermally conductive epoxy materials. In the power electronics market, what's really important is a little bit different than RF. We're talking about routing and converting power rather than RF signals.
One of the primary challenges is thermal management. These boards get very hot because the ICs involved are handling a lot of power. Designers use a variety of different techniques to manage the thermal performance. The techniques involved are heat sinks, heat pipes, different types of thermal spreaders like graphite spreaders, for example. In some situations, they actually use active cooling. That would be like putting a fan across the circuit board or maybe using some sort of liquid cooling with a heat exchanger.
The issue with all of these different types of thermal management techniques is that, first of all, they're costly, of course. Also, they add a lot of weight and a lot of bulk to the circuit. You have a regular circuit, and then you're putting something else on it in order to manage the thermal performance. Our solution is 92ML thermally conductive PCB material. This material actually has a high thermal conductivity. It's about two W/m-K in the Z-axis, and 3.5 W/m-K in the X- and Y-axes.
What that does is conduct the heat through the circuit board, and then it actually spreads the heat out over the surface of the circuit board. That allows you to keep the junction temperature very cool without adding any additional cost or weight or taking up any addition space.
Warner: In the power electronics market, I'm thinking of automotive boards, but what other applications have those high-power applications?
Ranieri: Yeah. Well, you definitely hit on one general market, which is the automotive market. Automotive has challenges with weight and space, of course, and cost, so all three, and then you throw in reliability as well. Reliability is extremely critical. The issue is that everything that you put into a car has to be driven around for hundreds of thousands of miles. Every little bit of weight or space is critical.
Within automotive, we see a lot of activity with electric vehicles and hybrid electric vehicles. The number one application there would be power converters. This requires, for example, a DC converter to take the 12-volt power and change it to 48 volts. The other area in automotive is electronic control units (ECUs). These are the computers that essentially run cars, as well as routing power to various powertrain or other components.
Those are the two applications there. The third is LEDs. LED lamps all generate quite a bit of heat. Typically, in LEDs, what's used is what's called IMS, an insulated metal substrate. It’s just a one-layer circuit board that has a dielectric, and then it has aluminum underneath, a plate of aluminum that acts as a heat spreader.
The last application is consumer electronics. In handhelds and wearable devices, the outside case temperature must be close to the temperature of your skin, about 37–40°C. When the CPU is running very heavily, you're playing a game or you're maybe using the camera, the temperature of the ICs inside increases, so you have to dissipate that heat. That's another application that we see.
Warner: Sounds like a very broad market and timely.
Ranieri: It is, yes.
Warner: Good luck at the show. Where can people go to find out more information about 92ML materials and the things that you're rolling out here at the show?
Ranieri: I'd suggest starting at our Technology Support Hub. That's where you can find articles and videos, white papers, data sheets, and all the information that you need to learn more about the product. Through the Tech Hub, you can also contact your local Sales Engineer, who can help you with the design of your product, as well as your local Technical Service Engineer, who can help your PCB shop build your design successfully the first time.
Warner: Well, thank you very much. It's been great to catch up with you, and good luck at your booth and with 92ML materials.
Ranieri: Thank you very much.
For more information, please visit Rogers’ Technology Support Hub.
Connect with Rogers online:
Testimonial
"Advertising in PCB007 Magazine has been a great way to showcase our bare board testers to the right audience. The I-Connect007 team makes the process smooth and professional. We’re proud to be featured in such a trusted publication."
Klaus Koziol - atgSuggested Items
Flexible Circuit Technologies to Host Free Flex Heater Webinar
08/18/2025 | Flexible Circuit TechnologiesGlobal Supplier of flexible circuits, flex design services, and assembly/box-build services, Flexible Circuit Technology will host their latest webinar, "Thermal Precision Meets Flexibility: The Technology Behind Heater Circuits" on Tuesday, August 26th, 2025 at 11 AM EDT.
A.R.T. Ltd. Nominated in Four Categories at 2025 Instrumentation and Electronics Industry Awards
08/11/2025 | A.R.T. Ltd.Advanced Rework Technology Ltd. (A.R.T. Ltd.), a leading provider of electronics training and consultancy, has been shortlisted in four categories at the 2025 Instrumentation and Electronics Industry Awards, including Industry Personality, Academic Support, Rising Star, and Best Customer Service.
EMC Taiwan Receives IPC-4101 Qualified Products Listing Certification
08/08/2025 | Global Electronics AssociationIPC’s Validation Services Program has awarded an IPC-4101 Qualified Products Listing (QPL) to Elite Materials Co. (EMC), an electronics base material manufacturing company headquartered in Taoyuan City, Taiwan.
Global Excellence in PCB Design: The Global Electronics Association Expands to Italy
08/07/2025 | Global Electronics AssociationIn today's rapidly evolving electronics industry, printed circuit boards (PCBs) serve as the critical backbone influencing the success, reliability, and time-to-market of countless products. Recognizing this essential role, the Global Electronics Association (formerly IPC), a worldwide leader in electronics standards, certification, and education, is now expanding its internationally acclaimed PCB design training to Italy.
Dana on Data: Best Practices in Interpreting Drawing Notes—‘Use Latest Revision’
08/07/2025 | Dana Korf -- Column: Dana on DataThe global nature of electronics manufacturing requires clear, consistent, and precise communication, particularly in technical documentation. An area where miscommunication often arises is in interpreting drawing notes—small lines of text with the potential to dramatically impact product quality, manufacturing efficiency, and customer satisfaction.