Making Use of Flat Surfaces for Catalysis
April 4, 2017 | KAUSTEstimated reading time: 2 minutes
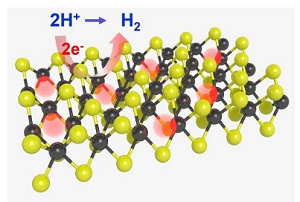
A novel way of increasing the chemical reactivity of a two-dimensional material has been used to produce a cheap and effective catalyst that can extract hydrogen from water—an important step in the quest for clean energy supplies. This technique developed by KAUST researchers may also have potential benefits for other manufacturing industries1.
Treating molybdenum disulfide in a hydrogen plasma creates active sites on its planar surface and makes the surface reactive for reducing water to hydrogen.
Hydrogen stores an enormous amount of energy that can be released by electrochemically combining hydrogen and oxygen in a fuel cell. Despite being the lightest element in the periodic table, gaseous hydrogen doesn’t occur naturally on Earth, so the race is on to find an efficient process to produce it.
One route to hydrogen generation is by electrolysis: passing an electrical current through water via two electrodes to cause a chemical reaction that breaks the water molecule into its component hydrogen and oxygen atoms. The speed of this so-called hydrogen evolution reaction can be increased using a catalyst on the electrodes.
Platinum is a perfect material for the job, but is it very expensive.
Lain-Jong Li, Professor of Material Science and Engineering at KAUST, with colleagues from the National Chiao Tung University and the National Applied Research Laboratories in Taiwan have demonstrated a method for increasing the catalytic activity of molybdenum disulfide, a much cheaper alternative.
Molybdenum disulfide is a two-dimensional material very similar to graphene. Previous experimental and theoretical results have verified its excellent catalytic potential and indicated that the hydrogen evolution reaction takes place at its jagged edges, while its flat surface planes remain chemically inert.
“A monolayer of molybdenum disulfide is only reactive for reducing water to hydrogen at its edge,” explained Li. “But we discovered an efficient way to create active sites on its planar surface, largely activating surface reactivity.”
Li and team created their molybdenum disulfide using a process called chemical vapor deposition. A sample was then transferred to a graphite substrate and placed in a vacuum chamber in which the researchers created a hydrogen plasma. This process removed some of the sulfur atoms from the surface of the sample. By adjusting the sample’s time in the plasma, the team could control the density of these sulfur vacancies.
The researchers confirmed the changes in catalytic activity and also found a useful offshoot of this process. Controlling the atomic composition of molybdenum disulfide could also lead to the development of electrical, optical and magnetic devices.
“Next we hope to move beyond the beaker and put the catalysts in practical flow cell tests,” said Li.
Suggested Items
KYZEN to Spotlight Stencil Cleaning Solutions at SMTA Oregon
05/02/2025 | KYZEN'KYZEN, the global leader in innovative environmentally friendly cleaning chemistries, will exhibit at the SMTA Oregon Expo & Tech Forum, scheduled to take place on Tuesday, May 20 at the Wingspan Event and Conference Center in Hillsboro, OR. KYZEN’s cleaning expert Jeff Deering will be on-site at the expo providing information about stencil cleaning chemistries, including KYZEN E5631J.
LG Innotek to Build FC-BGA into 700 Million USD Business with State-of-the-art Dream Factory
05/01/2025 | PR NewswireLG unveiled the Dream Factory, a hub for the production of FC-BGAs (Flip Chip Ball Grid Arrays), the company's next-generation growth engine, to the media for the first time and announced it on the 30th April.
Siemens, Intel Foundry Advance Collaboration
04/30/2025 | Siemens Digital Industries SoftwareSiemens Digital Industries Software announced that its continued collaboration with Intel Foundry has resulted in multiple product certifications, updated foundry reference flows, and additional technology enablement leveraging the foundry’s leading-edge technologies for next-generation integrated circuits (IC) and advanced packaging.
The Knowledge Base: Unlocking the Invisible—The Critical Role of X-ray Technology
04/29/2025 | Mike Konrad -- Column: The Knowledge BaseFrom detecting voids under BGAs to solder defects in high-reliability applications, X-ray inspection has become an indispensable tool in modern manufacturing. But how is the technology evolving? What challenges do experts face in deploying X-ray inspection effectively and what does the future hold for this critical quality assurance method?
KOKI Expands U.S. Sales Coverage with Multiple New Representatives
04/29/2025 | KOKIKOKI, a global leader in advanced soldering materials and process optimization services, is pleased to announce the expansion of its U.S. sales network with the addition of three new manufacturers’ representative firms: Assembled Product Specialists, Diversitech Reps Inc., and Eagle Electronics.