Dry Storage Cabinets' Role in Industry 4.0
April 11, 2017 | Andy Shaughnessy, I-Connect007Estimated reading time: 5 minutes
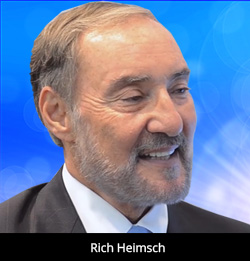
During IPC APEX EXPO 2017, Rich Heimsch, Super Dry’s Director of the Americas, sat down with Managing Editor Andy Shaughnessy to discuss the electronics manufacturing industry’s different versions of Industry 4.0, and Super Dry's strategies for dealing with all of them.
Andy Shaughnessy: Rich, we were talking earlier about how you guys plan to deal with other people’s versions of Industry 4.0 and traceability. Tell us about that.
Rich Heimsch: Industry 4.0 is certainly the buzz term of the day. It's clearly the next generation of manufacturing and promises to enable the concept of mass customization. To have the flexibility and the responsiveness of custom manufactured goods with the cost lowering associated with mass production. And 4.0 goes a long way to making that concept a reality. Between where we are today and that thought in the future, there are a lot of different approaches, and so there’s a lot of different companies with different goals towards reaching what is important to them in 4.0 today.
Smartening up the factory, the Internet of Machines, has all trickled down, if you will, even to the dry storage cabinet for MSL devices. It's been an intro to a part of those high-end automated warehouses that I was explaining to you in a previous conversation, where 50,000 reels and trays are all traced and the exposure tracked, floor life reset available, and safe storage of each device is provided. They might even be in different buildings. Actually, the idea of the warehouse is to centralize storage and then feed lines that are in different buildings, but the purposes include some concepts that have been important to many manufacturers for a long time, like traceability. Traceability has been of greater importance to some than others. The moisture damage, as we talked about many times before, tends to be a field failure, a latent defect. It's not necessarily an end-of-line defect.
It's the difference between a warranty issue and a serious product liability issue. The difference between an intermittent on my hand phone as opposed to my pacemaker or my ABS is a world of difference. All of those can be caused by the results of moisture damage. Knowing what condition the particular component was in, how much floor life had expired, where it was, and what the temperature and the humidity was on Christmas Day 2010 when asked on March 3, 2019…this is what more and more people are aggressively moving towards providing. Industries like automotive and medical have taken traceability to quite serious lengths already, pushing that out further into the supply chain. As supply chains have been reshaped over past years, now they need to force this out further from home base.
The same software, brains and networking that we developed for the robotically controlled warehouses is available to the manufacturer that either is not that big yet or doesn't intend ever to get that big and make that size of an investment. He's got five dry cabinets in three buildings, and he wants to know where the components are and what condition they're in, and that can be done. All of our equipment is immediately networkable and provides different levels of traceability, whether it’s down at the component level, the condition of the cabinet or the condition of the storage or floor life reset chamber. We can also offer the networking for existing cabinets, not just brand new ones, as well as for any other manufacturer’s.
So that's been a quickly evolving facet of this. At the same time, the floor life reset cabinet is replacing traditional Nitrogen ovens. I know I’m at an IPC show and we’re celebrating the 60th anniversary, but the standard used for moisture devices is 25 years old and the most recent revision I think is 10. So, lots of the technology that exists today isn't directly incorporated into that standard because it wasn't yet invented. It's the floor life reset and then the traceability and the ability to combine safe storage with floor life reset of expired or close-to-expired devices. And being able to do it more than once, because the oxidation and the intermetallic build up doesn't occur at lower and gentler temperatures.
Shaughnessy: Tell us about some of Super Dry’s latest storage developments.
Heimsch: One of the newest developments, which is driven by some of the original industries to focus on low humidity safe storage, is long-term storage. Military people, automotive people, and in Europe the train industry have 10–20 year requirements of replacements. Among other vehicles at home, my favorite is a 20-year-old Ford Explorer. It spent most of its life in a garage. It’s never been in the Northeast, never exposed to road salt and I can still get parts, many of which were already electronic. They don’t necessarily have it in stock locally, but they'll get it within 48 hours. The vehicle is 20 years old, but these automotive guys have been dealing with this as a fact of life, and the military as well. The devices are going obsolete even faster than ever. With shortened product life cycles, self-buying forward is a critical part of some people’s procurement challenge.
What they have discovered having experience at this is that the oxidation of course can be controlled, and there are a lot of studies done to determine what happens storing simple components for extended period of times. With the oxidation build up, a lot of people thought, “Well, I can use a more aggressive flux and get away with it.” But the thing that you can't get away with and can't be dealt with is the intermetallic build-up that has been seen occurring, and it has also been replicated in studies that long-term storage induces intermetallics. So, much like some of the other things that our European customers discovered before we saw the need here—things about lead-free and about moisture management—they came to us to address their need to deal with this intermetallic build-up.
We have cabinets out now that will measurably inhibit the growth of intermetallic. We talked about how high-temperature baking is bad for both oxidation and intermetallic build-up, but long-term storage, even in a safe below 5% atmosphere, which is safe storage according to the standards that exist, doesn't control the intermetallic. The way you control the intermetallic is with a product that's now being delivered, and that involves lowering the temperature. The worry about lowering the temperatures is that very low temperature exacerbates the growth of tin whiskers. So, just like there is a balance between oxidation and speed in the floor life reset, the balance between tin whiskers and stopping the intermetallic is an issue that faces the long-term storage people. Several of them believe they can solve this by reducing it below ambient, but not like a refrigerator, and so they mitigate that tin whisker risk and solve the intermetallic build-up. Those are the newest things we’ve been delivering and refining.
Shaughnessy: Okay, great. Thanks for speaking with us today, Rich.
Heimsch: Always a pleasure, Andy.
Suggested Items
The Global Electronics Association Releases IPC-8911: First-Ever Conductive Yarn Standard for E-Textile Application
07/02/2025 | Global Electronics AssociationThe Global Electronics Association announces the release of IPC-8911, Requirements for Conductive Yarns for E-Textiles Applications. This first-of-its-kind global standard establishes a clear framework for classifying, designating, and qualifying conductive yarns—helping to address longstanding challenges in supply chain communication, product testing, and material selection within the growing e-textiles industry.
IPC-CFX, 2.0: How to Use the QPL Effectively
07/02/2025 | Chris Jorgensen, Global Electronics AssociationIn part one of this series, we discussed the new features in CFX Version 2.0 and their implications for improved inter-machine communication. But what about bringing this new functionality to the shop floor? The IPC-CFX-2591 QPL is a powerful technical resource for manufacturers seeking CFX-enabled equipment. The Qualified Product List (QPL) helps streamline equipment selection by listing models verified for CFX compliance through a robust third-party virtual qualification process.
Advancing Aerospace Excellence: Emerald’s Medford Team Earns Space Addendum Certification
06/30/2025 | Emerald TechnologiesWe’re thrilled to announce a major achievement from our Medford, Oregon facility. Andy Abrigo has officially earned her credentials as a Certified IPC Trainer (CIT) under the IPC J-STD-001 Space Addendum, the leading industry standard for space and military-grade electronics manufacturing.
Magnalytix and Foresite to Host Technical Webinar on SIR Testing and Functional Reliability
06/26/2025 | MAGNALYTIXMagnalytix, in collaboration with Foresite Inc., is pleased to announce an upcoming one-hour Webinar Workshop titled “Comparing SIR IPC B-52 to Umpire 41 Functional & SIR Test Method.” This session will be held on July 24, 2025, and is open to professionals in electronics manufacturing, reliability engineering, and process development seeking insights into new testing standards for climatic reliability.
IPC Rebrands as Global Electronics Association: Interview With Dr. John W. Mitchell
06/22/2025 | Marcy LaRont, I-Connect007Today, following a major announcement, IPC is embracing the rapid advancement of technology with a bold decision to change its name to the Global Electronics Association. This name more accurately reflects the full breadth of its work and the modern realities of electronics manufacturing. In this exclusive interview, Global Electronics Association President and CEO Dr. John W. Mitchell shares the story behind the rebrand: Why now, what it means for the industry, and how it aligns with the organization’s mission.