Fabricators Speak Out on High-Speed Materials
April 18, 2017 | Barry Matties and Patty Goldman, I-Connect007Estimated reading time: 2 minutes
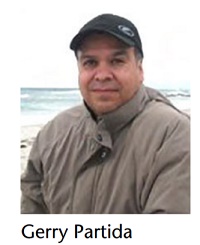
Recently, I-Connect007 Publisher Barry Matties and his editorial team joined with two PCB fabricators to discuss the state of advanced materials. The meeting included Gerry Partida, director of engineering at Summit Interconnect and Joe Menning, program manager at All Flex Flexible Circuits. The discussion centered on the processes, challenges, and procurement of high-speed materials, as well as need to work with customers during the design stage.
Patty Goldman: We are here to talk about high performance and high-speed materials. We’ve spoken with a few laminate suppliers, but we also wanted to get the viewpoint of the guys making the boards. We asked you to join us so we can find out how fabricators are dealing with these materials, what you need from suppliers, what you think our readers should know about advanced materials.
Barry Matties: When we start talking about highspeed materials, what are the greatest challenges you face with high-speed materials, from procurement to processing and delivery? Maybe even from OEMs specifying materials or not? Gerry, why don’t we start with you.
Gerry Partida: Thank you for allowing us to share this. This is very important stuff. A lot of the RF materials are very hard to register when you laminate or process the materials. There are many RF materials that are not glass-reinforced or very loosely glass-reinforced. When we planarize the material for epoxy fill, or blind via lamination structures and we epoxy fill, the material stretches out. We call some of it bubble gum because you can just distort the material as you planarize an epoxy-filled via. Also, the material just moves a lot, in some cases three times greater than standard glass-reinforced epoxy materials.
That’s one of the biggest challenges—maintaining registration and controlling it, knowing where it’s going to end up. The material is very expensive. I like to use the analogy with people that building FR-4 boards, regular, digital or something that’s straightforward versus an RF board is like playing craps. The difference between FR-4 boards and RF boards is that the FR-4 boards are like playing craps Saturday night in Laughlin, Nevada, which is a $5 minimum bet, where RF is like playing the Bellagio at 9 o’clock on Saturday night where the minimum bet is $25. Same rules, same game, but the buyin is huge because of the registration and the other fun stuff that goes with it. You can lose fast or you can win a lot.
That’s one of the greatest challenges—the material itself, its softness, its registration, as well as processing. One of the things is holding registration and the material. The other parts that are a challenge for the materials are the ability to deposit electroless and maintaining peel strength. A lot of them have low peel strength. Many RF materials can have smear.
We call it flat, but it’s smear when you drill and you cover the inner face of an innerlayer pad; it violates the IPC-6012 rigid PCB performance spec. It’s allowed somewhat in IPC-6018, the performance spec for high-frequency/microwave PCBs—but smear is always a concern on a lot of high-speed materials.
Some of the other challenges with materials are Teflon or PTFE surfaces, where you have to do special treatment to get the solder mask or legend to stick to it.
To read the full version of this interview which appeared in the April 2017 issue of The PCB Magazine, click here.
Suggested Items
Indium’s Karthik Vijay to Present on Dual Alloy Solder Paste Systems at SMTA’s Electronics in Harsh Environments Conference
05/06/2025 | Indium CorporationIndium Corporation Technical Manager, Europe, Africa, and the Middle East Karthik Vijay will deliver a technical presentation on dual alloy solder paste systems at SMTA’s Electronics in Harsh Environments Conference, May 20-22 in Amsterdam, Netherlands.
SolderKing Achieves the Prestigious King’s Award for Enterprise in International Trade
05/06/2025 | SolderKingSolderKing Assembly Materials Ltd, a leading British manufacturer of high-performance soldering materials and consumables, has been honoured with a King’s Award for Enterprise, one of the UK’s most respected business honours.
Knocking Down the Bone Pile: Gold Mitigation for Class 2 Electronics
05/07/2025 | Nash Bell -- Column: Knocking Down the Bone PileIn electronic assemblies, the integrity of connections between components is paramount for ensuring reliability and performance. Gold embrittlement and dissolution are two critical phenomena that can compromise this integrity. Gold embrittlement occurs when gold diffuses into solder joints or alloys, resulting in mechanical brittleness and an increased susceptibility to cracking. Conversely, gold dissolution involves the melting away of gold into solder or metal matrices, potentially altering the electrical and mechanical properties of the joint.
'Chill Out' with TopLine’s President Martin Hart to Discuss Cold Electronics at SPWG 2025
05/02/2025 | TopLineBraided Solder Columns can withstand the rigors of deep space cold and cryogenic environments, and represent a robust new solution to challenges facing next generation large packages in electronics assembly.
BEST Inc. Reports Record Demand for EZReball BGA Reballing Process
05/01/2025 | BEST Inc.BEST Inc., a leader in electronic component services, is pleased to announce they are experiencing record demand for their EZReball™ BGA reballing process which greatly simplifies the reballing of ball grid array (BGA) and chip scale package (CSP) devices.