-
- News
- Books
Featured Books
- pcb007 Magazine
Latest Issues
Current IssueInventing the Future with SEL
Two years after launching its state-of-the-art PCB facility, SEL shares lessons in vision, execution, and innovation, plus insights from industry icons and technology leaders shaping the future of PCB fabrication.
Sales: From Pitch to PO
From the first cold call to finally receiving that first purchase order, the July PCB007 Magazine breaks down some critical parts of the sales stack. To up your sales game, read on!
The Hole Truth: Via Integrity in an HDI World
From the drilled hole to registration across multiple sequential lamination cycles, to the quality of your copper plating, via reliability in an HDI world is becoming an ever-greater challenge. This month we look at “The Hole Truth,” from creating the “perfect” via to how you can assure via quality and reliability, the first time, every time.
- Articles
- Columns
- Links
- Media kit
||| MENU - pcb007 Magazine
Estimated reading time: 4 minutes
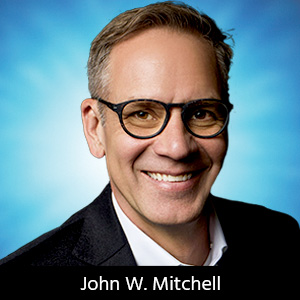
One World, One Industry: Three Ways to Close the Skills Gap in U.S. Manufacturing
The skills gap is a chronic problem in the manufacturing sector. Most manufacturing companies have a hard time aligning the talent needed to run their businesses with the talent that is available to work locally. And as new innovations emerge, new skills requirements emerge as well.
A new report[1] from the National Academies of Sciences, Engineering, and Medicine cites employer surveys and numerous industry and government reports in reaching the conclusion that the nation has an inadequate supply of skilled technical workers to achieve its competitiveness and economic growth objectives.
In our sector, according to a 2015 study[2] by the Manufacturing Institute, nearly 3.5 million manufacturing jobs are expected to become available in the United States over the next decade as current workers retire and the economy grows. Unfortunately, the skills gap is expected to leave 2 million of these jobs unfilled.
As an association that represents thousands of member facilities across the electronics industry supply chain, we decided to survey[3] our U.S. members [EMS companies] to gain insight into how the skills gap affects them. The results indicate that most of our member companies have trouble finding applicants with the necessary experience and technical skills.
Among production jobs, general assembler and hand solderer are the most difficult to fill. On the professional side, quality control, process and entry-level electrical engineers have been hardest to find. Insufficient experience is the most common reason that applicants do not qualify for most positions. However, for many technical professional positions, the leading reason jobs went unfilled was that there were no applicants at all.
Respondents cite many essential skills that are in short supply, but the most common ones are soldering for production jobs, and engineers with industry experience, especially in process, test, and quality control. Two-thirds of our member companies reported they would expand their operations if they knew that finding qualified workers would be no problem. Thus, finding solutions to the skills gap is a high priority if America wants to expand its manufacturing sector.
First, we need to do a better job of engaging kids in science, technology, engineering, and math (STEM) topics in elementary and middle school. Unfortunately, the Common Core standards[4] adopted by 44 states typically cover only language and math, with nothing on science and technology. Rather than attacking those standards, as some have done, policymakers should expand them and incentivize STEM teaching from kindergarten through 12th grade.
And America’s educational standards should be tougher. Other nations set a high bar, pushing their youth to the top of the world rankings. Only by building U.S. students’ skills and confidence in STEM subjects in their youth can the United States compete globally and build a solid pipeline of future engineers.
Second, we need to get rid of the notion that the only successful education is a liberal arts degree from college. Many noble and lucrative careers can be had by those who learn trades and technical specialties. In Germany, companies like Siemens and Bosch use apprenticeships to train their workers in advanced engineering and manufacturing. The model is used in professions like hospitality and banking as well. Such apprenticeship programs exist in the United States, but on a much smaller scale. Rather than cutting government funding for these programs, leaders in education and business should work together to build them up. IPC supports the bipartisan Strengthening Career and Technical Education for the 21st Century Act, H.R. 2353[5], which is making its way through Congress and would provide federal support for career education programs.
These steps are urgently needed, along with a broader strategy to ensure that continuous training is a high priority in our industry. And third, there is much that we, the companies in our industry, can do on our own. We can host site visits or tours of our facilities and open our doors to local schools and the surrounding community to illustrate the importance of the electronics industry for the global economy. We can also develop a program or presentation to engage students and interest them in engineering careers. Companies may also offer intern programs for high school and college students. Additionally, IPC offers dozens of courses online and in-person, providing knowledge and certifications that can take current workers to the next level in their careers.
Only by raising the educational bar and building a stronger network of technical training programs can the United States hope to develop the workforce that it needs to compete in the global economy.
References
1. Building America’s Skilled Technical Workforce, the National Academies Press.
2. The skills gap in U.S. manufacturing: 2015 and beyond, the Manufacturing Institute.
3. IPC survey: Findings on the Skills Gap in U.S. Electronics Manufacturing—2017D1 (available for purchase).
4. Common Core Standards—About the Standards
5. H.R.2353—Strengthening Career and Technical Education for the 21st Century Act
John Mitchell is president and CEO of IPC—Association Connecting Electronics Industries. To read past columns or to contact Mitchell, click here.
Editor's Note: This column originally appeared in the July 2017 issue of The PCB Magazine, click here.
More Columns from One World, One Industry
One World, One Industry: IPC APEX EXPO 2025 Marks a Special Anniversary YearOne World, One Industry: Mapping the Future of the Electronics Workforce
One World, One Industry: Mastering Technology Prognostication
One World, One Industry: To Thrive, Surround Yourself with Good People
One World, One Industry: Sustainability Challenges—A Collaborative Approach
One World, One Industry: What’s Next Becomes Now at IPC APEX EXPO 2024
One World, One Industry: ‘Blocking and Tackling’ During Tough Economic Times
One World, One Industry: Developing Your Team to Become Great Implementors