Counterfeit Electronic Components Identification: A Case Study
July 26, 2017 | Martin Goetz and Ramesh Varma, Northrop Grumman Corp.Estimated reading time: 6 minutes
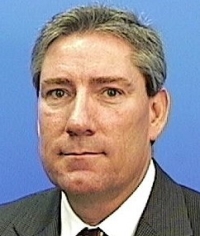
Abstract
Counterfeit electronic components are finding their way into today's defense electronics. The problem gets even more complex when procuring DMS (diminishing manufacturing source) parts. This paper will provide a brief introduction to counterfeit prevention and detection standards, particularly as they relate to the aerospace and defense sector. An analysis of industry information on the types and nature of counterfeit components will be discussed to illustrate those most likely to be counterfeited, followed by a specific case at a major defense contractor.
The case involved two circuit card assemblies failing at test, whereby their root cause for failure was identified as "unable to write specific addresses at system speeds." The error was traced to a 4MB SRAM received from an approved supplier. Fifteen other suspect parts were compared with one authentic part directly purchased from a supplier approved by the part manufacturer. Defects or anomalies were identified but not enough to unequivocally reject these parts as counterfeit as the defects could have also happened in the pre-tinning process, which is a program-specific requirement if the parts were stored for more than three years. Through the subsequent analysis, subtle differences between the authentic and suspect parts were identified and isolated. The methodologies and process chosen to identify counterfeit parts will be reviewed and an assessment of the results will be presented along with the defects found in relation to the defect types reported in relevant test standards.
Introduction
The Defense Federal Acquisition Regulations DFARS 252.246-7007 Contractor Counterfeit Electronic Part Detection and Avoidance System defines a counterfeit part as:
An unlawful or unauthorized reproduction, substitution, or alteration that has been knowingly mismarked, misidentified, or otherwise misrepresented to be an authentic, unmodified electronic part from the original manufacturer, or a source with the express written authority of the original manufacturer or current design activity, including an authorized aftermarket manufacturer. Unlawful or unauthorized substitution includes used electronic parts represented as new, or the false identification of grade, serial number, lot number, date code, or performance characteristics.
Highlights for the DFARS Case 2012-D055 final rule include:
• Applying requirements to the acquisition of electronic parts and assemblies containing electronic parts, including commercial items (COTS)
• Defining “Counterfeit” and “Suspect counterfeit”, is limited to electronics, including embedded software and firmware
• The costs of counterfeit electronic parts or suspect counterfeit electronic parts and the cost of rework or corrective action that may be required to remedy the use of inclusion of such parts are unallowable (unless electronic parts were provided as GFE and timely notice of discovery was provided by contractor)
Based on the highlights for the ruling and the impact that counterfeit parts could have on the performance of fielded systems, it should be obvious in terms of the importance of understanding, identifying and addressing suspect counterfeit parts in the aerospace and defense industry. Although the current definition and ruling applies to electronics, the expectation is the definition will eventually broaden to include nonelectronics (i.e. optics, mechanics, MEMs, and materials). Therefore, a robust process to ensure parts that are received and used in systems to support the aerospace and defense industry is paramount to not only the business and industry, but to the users of the products that rely on these systems, especially the warfighter.
Counterfeit Parts Business is a Multibillion Dollar Industry
The discussion of recognizing that counterfeit parts have been introduced into the supply chain is not new, with various companies, and technical journals publishing as early in 2002.
In a 2006 article published by Pecht and Tiku and noted in the UK Electronics Alliance (UKEA) position paper, “UKEA Position on Counterfeit Electronic Components”:
Alliance for Grey Market and Counterfeit Abatement (AGMA), based in the USA, estimates that, in 2006, up to 10% of technology products sold worldwide are counterfeit, which amounts to $100 billion of sales revenues. However, this does not take into account consequential losses. In 2007, the US Patent and Trademark Office estimated that total ‘counterfeiting and piracy (activity) drains about $250 billion out of the US economy each year and 75,000 jobs’.
A primary driver of counterfeit parts has been part scarcity, or diminishing manufacturing source and material supply (DMSMS). Realizing that as the consumer market began to grow exponentially in the 1980s and 1990s, the supply base for manufacturing parts rated for military and high-reliability applications was having a difficult time keeping up with demand, and part availability was becoming more difficult. These market forces drove the opportunity to introduce counterfeit parts into the supply chain through ‘gray market electronics brokers’. According to a 2001 article on fake parts, “One U.S. independent distributor, which asked to remain anonymous, said it paid a broker in China $70,000 for 1206 case-size ceramic capacitors about three months ago. The 90-cent parts, which under less-constrained market conditions would have cost 20 cents, slipped through two quality inspections before arriving on the OEM's production floor".
Bad Parts are not Always Counterfeit
It is important to recognize that, just because there are anomalies identified on electronic parts, it does not signify that the parts are counterfeit. It does, however, require the incoming inspection organization to assume the responsibility to make initial determination as to whether there is enough evidence to suggest the parts from a lot or shipment should be evaluated for additional anomalies. Three important points to consider when creating a system to screen for counterfeit parts are:
• They are not easy to identify, even with sophisticated analytical methods
• They are in the supply chain, even with authorized distributors
• They are more of an issue with obsolete parts
Page 1 of 2
Suggested Items
'Chill Out' with TopLine’s President Martin Hart to Discuss Cold Electronics at SPWG 2025
05/02/2025 | TopLineBraided Solder Columns can withstand the rigors of deep space cold and cryogenic environments, and represent a robust new solution to challenges facing next generation large packages in electronics assembly.
Kitron: Q1 2025 - Strong Start to the Year
04/25/2025 | KitronKitron reported first-quarter results characterised by continued momentum in the Defence & Aerospace market sector and a growing order backlog.
RTX's Collins Aerospace Enhances Capabilities to Speed Marine Corps Decision-making in Battle
04/22/2025 | RTXCollins Aerospace, an RTX business, successfully demonstrated new technology that helps the military gather and use information from a wider range of sources at Project Convergence Capstone 5, a large-scale military exercise.
AdvancedPCB Appoints Gary Stoffer as Chief Commercial Officer
04/18/2025 | PRNewswireAdvancedPCB is proud to announce the appointment of Gary Stoffer as its new Chief Commercial Officer (CCO). In this role, Stoffer will lead all sales, marketing, and commercial strategy initiatives as the company continues its mission to deliver cutting-edge PCB solutions to industries worldwide.
Real Time with... IPC APEX EXPO 2025: GreenSource's Growth and Future Developments
04/15/2025 | Real Time with...IPC APEX EXPOThings are looking bright for GreenSource. Michael Gleason shares an update on GreenSource's recent growth and upcoming changes. A recipient of a Defense Production Act Investment Program award, GreenSource is planning for new substrate capabilities. Current investments continue to enhance equipment and sustainability initiatives such as water quality. And their unique collaboration with the University of New Hampshire continues to aid their workforce development, despite recruitment challenges.