The Speed of Nouya: Interview with Bao Xinyang of Shanghai Nanya
July 31, 2017 | Tulip Gu, I-Connect007Estimated reading time: 4 minutes
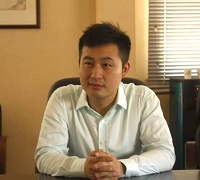
The theme of the June issue of PCB007 China Magazine is "High-Speed Materials." As is becoming more widely understood, expanding our domestic material supply is the only way for China’s high-frequency, high-speed circuit board industry to grow. To tell us more about this, we interviewed Bao Xinyang, the marketing director of Shanghai Nanya Copper Clad Laminate Co., Ltd., a well-known CCL manufacturer in China.
Shanghai Nanya Copper Clad Laminate Co. Ltd. (known as Nouya in China) was established in 2000 and it took them just seven months to construct and finish the first batch of product. This is well-known in the industry, and became known as "The Speed of Nouya." In the next 17 years, revenue grew rapidly, from 120 million RMB in 2003 to almost 1.2 billion RMB in 2016.
Shanghai Nanya's target market strategic planning has included three major upgrades. The initial application was for home appliances and general consumer electronics; then they focused on PCs and peripheral hardware, IT-related equipment, and 2G/3G mobile communication product. Today, they are focusing on 4G mobile communication and base station, Internet hardware equipment, automotive electronics and high-end consumer electronics.
The Phase 3-2 project is yet another upgrade to toward the higher end in technology, product and market application level for Shanghai Nanya. When this phase is complete, only a small amount of its production capacity will be used to meet the demand of high-end customers; the majority of the capacity will go to automotive, Internet of Things, aerospace, healthcare hardware equipment, robotics and industrial 4.0 hardware equipment, 5G mobile communication, and artificial intelligence. These are the upgraded Shanghai Nanya target markets.
Tulip Gu: As CCL suppliers, what is the biggest challenge you have encountered in high-speed material production and R&D?
Bao Xinyang: First of all, we have been able to provide a series of high-speed CCL, and we are speeding up our R&D on our high-end high-speed product line. Today, the high-end high-speed product is dominated by U.S. and Japanese companies; they have a lot of IP and patents for new material. Secondly, high-speed materials such as RTF/HVLP copper foil, low-Dk/Df glass, high-performance resin, etc., are also mainly rely on imported products. These will be our main challenges in the high-end high-speed material development.
Gu: Can you tell us about your products?
Bao: At this year's CPCA Show in March, we took our three latest product series: NY series for automotive electronics; Nouya series for high-speed circuits; and NYHP series for 5G, microwave (mainly millimeter wave) communications and other high-frequency circuits. Nouya series high-speed board has five models of CCL products, in which the mid-loss and low-loss series have passed the qualifications of Huawei, ZTE and other end customers. Also, we have developed PTFE CCL in our NYHP series high-frequency board; the end-product qualifications are in progress.
Gu: How do you see the trends of China's high-frequency high-speed PCB market in recent years, with regard to product applications, technology updates, and process improvement?
Bao: The high-frequency, high-speed PCB market is growing very rapidly and, with the extensive application of 4G products and the arrival of 5G, the demand for high-frequency, high-speed materials will be growing too. Product performance requirements are also being upgraded, from very-low-loss to low-loss, to the current ultra-low-loss. This is a challenge for us, but is also a very good opportunity.
Gu: In this area, what is the main advantage of Chinese companies, and will this advantage provide global competitiveness?
Bao: I think China will be leading the world in the 5G era. Government policy and market are providing the greatest support. According to "The 13th Five-Year Plan" road map, the technology of high-frequency, high-speed CCL, electronic copper foil will be researched and upgraded, while government policy provides solid support and concession. China's PCB output value is US$27.104 billion in 2016, which is more than 50% of global output, and it is still growing. Driven by policy and market, Chinese enterprises will invest more in R&D and production, to maintain global competitiveness.
Gu: Do you think there will be a better way for PCB manufacturers and material suppliers to work together?
Bao: Advanced high-speed, high-frequency material will not only improve material properties, but will be also more demanding for PCB manufacturers to process. This needs to be addressed by both material suppliers and PCB manufacturers working together more closely. In order to achieve a win-win situation, Shanghai Nanya is committed to building a strong strategic partnership with the supply chain to enhance technical capability, increase R&D investment, and make material and PCB processing smoother.
For instance, we passed the qualification of Huawei, Sony and other well-known companies. In the meantime, we have built long-term business relationships with CMK and Alps Electric of Japan, Daedeok and DAP of South Korea, and Shennan Circuits, Wuzhu Technology, Aoshikong Technology and Tripod Technology in China. High-quality Japanese and domestic high-end customers will help us to better understand customer needs and product technology, to make our product fit customer needs better. Also, it will promote companies to improve their management capabilities. China will be leading in the 5G era; as a material supplier, we are willing to work deeper and more extensively with PCB manufacturers and OEMs.
Tulip Gu is executive editor for I-Connect007 China.
Suggested Items
RF PCB Design Tips and Tricks
05/08/2025 | Cherie Litson, EPTAC MIT CID/CID+There are many great books, videos, and information online about designing PCBs for RF circuits. A few of my favorite RF sources are Hans Rosenberg, Stephen Chavez, and Rick Hartley, but there are many more. These PCB design engineers have a very good perspective on what it takes to take an RF design from schematic concept to PCB layout.
Trouble in Your Tank: Causes of Plating Voids, Pre-electroless Copper
05/09/2025 | Michael Carano -- Column: Trouble in Your TankIn the business of printed circuit fabrication, yield-reducing and costly defects can easily catch even the most seasoned engineers and production personnel off guard. In this month’s column, I’ll investigate copper plating voids with their genesis in the pre-plating process steps.
Elephantech: For a Greener Tomorrow
04/16/2025 | Marcy LaRont, PCB007 MagazineNobuhiko Okamoto is the global sales and marketing manager for Elephantech Inc., a Japanese startup with a vision to make electronics more sustainable. The company is developing a metal inkjet technology that can print directly on the substrate and then give it a copper thickness by plating. In this interview, he discusses this novel technology's environmental advantages, as well as its potential benefits for the PCB manufacturing and semiconductor packaging segments.
Trouble in Your Tank: Organic Addition Agents in Electrolytic Copper Plating
04/15/2025 | Michael Carano -- Column: Trouble in Your TankThere are numerous factors at play in the science of electroplating or, as most often called, electrolytic plating. One critical element is the use of organic addition agents and their role in copper plating. The function and use of these chemical compounds will be explored in more detail.
IDTechEx Highlights Recyclable Materials for PCBs
04/10/2025 | IDTechExConventional printed circuit board (PCB) manufacturing is wasteful, harmful to the environment and energy intensive. This can be mitigated by the implementation of new recyclable materials and technologies, which have the potential to revolutionize electronics manufacturing.