Smart Bandage Could Promote Better, Faster Healing
October 6, 2017 | University of Nebraska-LincolnEstimated reading time: 3 minutes
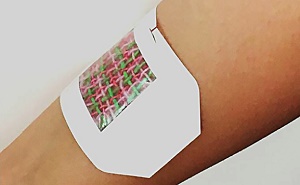
Researchers from the University of Nebraska-Lincoln, Harvard Medical School and MIT have designed a smart bandage that could eventually heal chronic wounds or battlefield injuries with every fiber of its being.
Advanced Functional Materials
The bandage consists of electrically conductive fibers coated in a gel that can be individually loaded with infection-fighting antibiotics, tissue-regenerating growth factors, painkillers or other medications.
A microcontroller no larger than a postage stamp, which could be triggered by a smartphone or other wireless device, sends small amounts of voltage through a chosen fiber. That voltage heats the fiber and its hydrogel, releasing whatever cargo it contains.
Smart Bandage
A single bandage could accommodate multiple medications tailored to a specific type of wound, the researchers said, while offering the ability to precisely control the dose and delivery schedule of those medications. That combination of customization and control could substantially improve or accelerate the healing process, said Ali Tamayol, assistant professor of mechanical and materials engineering at Nebraska.
“This is the first bandage that is capable of dose-dependent drug release,” Tamayol said. “You can release multiple drugs with different release profiles. That’s a big advantage in comparison with other systems. What we did here was come up with a strategy for building a bandage from the bottom up.
“This is a platform that can be applied to many different areas of biomedical engineering and medicine.”
The team envisions its smart bandage being used initially to treat chronic skin wounds that stem from diabetes. More than 25 million Americans – and more than 25 percent of U.S. adults 65 and older – could suffer from such wounds. The Centers for Disease Control and Prevention has estimated that diabetes cases will double or triple by the year 2050.
“The medical cost associated with these types of wounds is tremendous,” Tamayol said. “So there is a big need to find solutions for that.”
Those wounded in combat might also benefit from the bandage’s versatility and customizability, Tamayol said, whether to stimulate faster healing of bullet and shrapnel wounds or prevent the onset of infection in remote environments.
“Soldiers on the battlefield may be suffering from a number of different injuries or infections,” he said. “They might be dealing with a number of different pathogens. Imagine that you have a variable patch that has antidotes or drugs targeted toward specific hazards in the environment.”
Bandage aid
Existing bandages range from basic dry patches to more advanced designs that can passively release an embedded medication over time. To evaluate the potential advantages of their smart bandage, Tamayol and his colleagues at Harvard ran a series of experiments.
In one, the researchers applied a smart bandage loaded with growth factor to wounded mice. When compared with a dry bandage, the team’s version regrew three times as much of the blood-rich tissue critical to the healing process.
Another experiment showed that an antibiotic-loaded version of the bandage could eradicate infection-causing bacteria. Collectively, Tamayol said, the experiments also demonstrated that the heat needed to release the medications did not affect their potency.
Advanced Functional Materials
Though the researchers have patented their design, it will need to undergo further animal and then human testing before going to market. That could take several years, though the fact that most of the design’s components are already approved by the Food and Drug Administration should streamline the process, Tamayol said.
In the meantime, he said, the researchers are also working to incorporate thread-based sensors that can measure glucose, pH and other health-related indicators of skin tissue. Integrating that capability would allow the team to create a bandage that could autonomously deliver proper treatments.
The authors detailed their design and findings in the journal Advanced Functional Materials. Tamayol authored the study with Harvard’s Ali Khademhosseini, Pooria Mostafalu, Gita Kiaee, Giorgio Giatsidis, Akbar Khalilpour, Mahboobeh Nabavinia, Mehmet Dokmeci and Dennis Orgill, along with Sameer Sonkusale of Tufts University.
Suggested Items
Intervala Hosts Employee Car and Motorcycle Show, Benefit Nonprofits
08/27/2024 | IntervalaIntervala hosted an employee car and motorcycle show, aptly named the Vala-Cruise and it was a roaring success! Employees had the chance to show off their prized wheels, and it was incredible to see the variety and passion on display.
KIC Honored with IPC Recognition for 25 Years of Membership and Contributions to Electronics Manufacturing Industry
06/24/2024 | KICKIC, a renowned pioneer in thermal process and temperature measurement solutions for electronics manufacturing, is proud to announce that it has been recognized by IPC for 25 years of membership and significant contributions to electronics manufacturing.
Boeing Starliner Spacecraft Completes Successful Crewed Docking with International Space Station
06/07/2024 | BoeingNASA astronauts Barry "Butch" Wilmore and Sunita "Suni" Williams successfully docked Boeing's Starliner spacecraft to the International Space Station (ISS), about 26 hours after launching from Cape Canaveral Space Force Station.
KIC’s Miles Moreau to Present Profiling Basics and Best Practices at SMTA Wisconsin Chapter PCBA Profile Workshop
01/25/2024 | KICKIC, a renowned pioneer in thermal process and temperature measurement solutions for electronics manufacturing, announces that Miles Moreau, General Manager, will be a featured speaker at the SMTA Wisconsin Chapter In-Person PCBA Profile Workshop.
The Drive Toward UHDI and Substrates
09/20/2023 | I-Connect007 Editorial TeamPanasonic’s Darren Hitchcock spoke with the I-Connect007 Editorial Team on the complexities of moving toward ultra HDI manufacturing. As we learn in this conversation, the number of shifting constraints relative to traditional PCB fabrication is quite large and can sometimes conflict with each other.