-
- News
- Books
Featured Books
- pcb007 Magazine
Latest Issues
Current IssueThe Hole Truth: Via Integrity in an HDI World
From the drilled hole to registration across multiple sequential lamination cycles, to the quality of your copper plating, via reliability in an HDI world is becoming an ever-greater challenge. This month we look at “The Hole Truth,” from creating the “perfect” via to how you can assure via quality and reliability, the first time, every time.
In Pursuit of Perfection: Defect Reduction
For bare PCB board fabrication, defect reduction is a critical aspect of a company's bottom line profitability. In this issue, we examine how imaging, etching, and plating processes can provide information and insight into reducing defects and increasing yields.
Voices of the Industry
We take the pulse of the PCB industry by sharing insights from leading fabricators and suppliers in this month's issue. We've gathered their thoughts on the new U.S. administration, spending, the war in Ukraine, and their most pressing needs. It’s an eye-opening and enlightening look behind the curtain.
- Articles
- Columns
- Links
- Media kit
||| MENU - pcb007 Magazine
Process Engineering & Defect Prevention
October 6, 2017 | Michael Carano, RBP Chemical TechnologyEstimated reading time: 1 minute
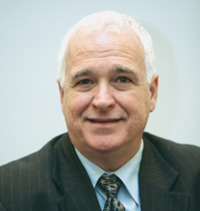
As of this writing, I have explored many topics related to specific defects that plague printed circuit board fabricators. A key underlying theme of these writings underscores the critical need of the skilled troubleshooter to get to the underlying cause or causes of the defects. Defects may “manifest” or be detected in or after a specific operation within the printed circuit board manufacturing process, but the underlying root cause may have occurred earlier (perhaps much earlier) in the process. As I have written in prior columns, I chose to present the anomaly or defect where it is most likely to be detected, then subsequently presented the most likely root causes wherever they might have been introduced. It should be noted that these examples are presented as likely starting places for the investigation of anomalies or defects presented, or the kinds of causes that might be investigated.
The troubleshooter’s task is complicated by the fact that there are many possible ways to combine or sequence the individual process steps available to achieve the desired end structure. As an example, a simple, single-lamination multilayer printed wiring board may involve 30 to 50 process steps, while a complex, multiple lamination (sequential lamination) printed wiring board, with pre- and post-machining and other mechanical operations, and selective plating processes, could involve several hundred process steps. In an ideal world, each step could be verified correct immediately during or after the process, but in practice the effect of many processes cannot be readily evaluated until the completion of many subsequent steps make latent errors visible. Much effort is and has been expended in attempts to improve this, with limited success. Thus, it remains a troublesome issue. The concern then is the defect may not manifest itself until several downstream process steps. One may refer to this as the latent defect. The impact of these latent defects is four-fold:
1. First, the detection and verification of the defect may require real time and the diversion of skilled resources—already in short supply in most lean-running modern operations.
2. Second, there is a schedule impact in today’s just-in-time operating mode, both of the process flow disruption inherent in the detection and in the verification of the defect.
To read the full version of this article which appeared in the October 2017 issue of The PCB Magazine, click here.
Suggested Items
Knocking Down the Bone Pile: Addressing End-of-life Component Solderability Issues, Part 4
07/16/2025 | Nash Bell -- Column: Knocking Down the Bone PileIn 1983, the Department of Defense identified that over 40% of military electronic system failures in the field were electrical, with approximately 50% attributed to poor solder connections. Investigations revealed that plated finishes, typically nickel or tin, were porous and non-intermetallic.
Digital Twin Concept in Copper Electroplating Process Performance
07/11/2025 | Aga Franczak, Robrecht Belis, Elsyca N.V.PCB manufacturing involves transforming a design into a physical board while meeting specific requirements. Understanding these design specifications is crucial, as they directly impact the PCB's fabrication process, performance, and yield rate. One key design specification is copper thieving—the addition of “dummy” pads across the surface that are plated along with the features designed on the outer layers. The purpose of the process is to provide a uniform distribution of copper across the outer layers to make the plating current density and plating in the holes more uniform.
The Knowledge Base: A Conference for Cleaning and Coating of Mission-critical Electronics
07/08/2025 | Mike Konrad -- Column: The Knowledge BaseIn electronics manufacturing, there’s a dangerous misconception that cleaning and coating are standalone options, that they operate in different lanes, and that one can compensate for the other. Let’s clear that up now. Cleaning and conformal coating are not separate decisions. They are two chapters in the same story—the story of reliability.
SMT007 Magazine July—What’s Your Competitive Sweet Spot?
07/01/2025 | I-Connect007 Editorial TeamAre you in a niche that’s growing or shrinking? Is it time to reassess and refocus? We spotlight companies thriving by redefining or reinforcing their niche—what are their insights? In the July 2025 issue of SMT007 Magazine, we spotlight companies thriving by redefining or reinforcing their niche and offer insights to help you evaluate your own.
Smarter Machines Use AOI to Transform PCB Inspections
06/30/2025 | Marcy LaRont, PCB007 MagazineAs automated optical inspection (AOI) evolves from traditional end-of-process inspections to proactive, in-line solutions, the integration of AI and machine learning is revolutionizing defect reduction and enhancing yields, marking a pivotal shift in how quality is managed in manufacturing.