Nanotube Fiber Antennas as Capable as Copper
October 23, 2017 | Rice UniversityEstimated reading time: 2 minutes
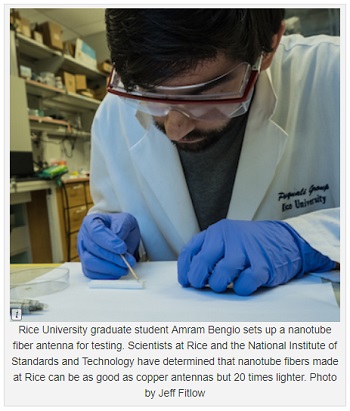
Fibers made of carbon nanotubes configured as wireless antennas can be as good as copper antennas but 20 times lighter, according to Rice University researchers. The antennas may offer practical advantages for aerospace applications and wearable electronics where weight and flexibility are factors.
The discovery offers more potential applications for the strong, lightweight nanotube fibers developed by the Rice lab of chemist and chemical engineer Matteo Pasquali. The lab introduced the first practical method for making high-conductivity carbon nanotube fibers in 2013 and has since tested them for use as brain implants and in heart surgeries, among other applications.
The research could help engineers who seek to streamline materials for airplanes and spacecraft where weight equals cost. Increased interest in wearables like wrist-worn health monitors and clothing with embedded electronics could benefit from strong, flexible and conductive fiber antennas that send and receive signals, Pasquali said.
The Rice team and colleagues at the National Institute of Standards and Technology (NIST) developed a metric they called “specific radiation efficiency” to judge how well nanotube fibers radiated signals at the common wireless communication frequencies of 1 and 2.4 gigahertz and compared their results with standard copper antennas. They made thread comprising from eight to 128 fibers that are about as thin as a human hair and cut to the same length to test on a custom rig that made straightforward comparisons with copper practical.
“Antennas typically have a specific shape, and you have to design them very carefully,” said Rice graduate student Amram Bengio, the paper’s lead author. “Once they’re in that shape, you want them to stay that way. So one of the first experimental challenges was getting our flexible material to stay put.”
Contrary to earlier results by other labs (which used different carbon nanotube fiber sources), the Rice researchers found the fiber antennas matched copper for radiation efficiency at the same frequencies and diameters. Their results support theories that predicted the performance of nanotube antennas would scale with the density and conductivity of the fiber.
“Not only did we find that we got the same performance as copper for the same diameter and cross-sectional area, but once we took the weight into account, we found we’re basically doing this for 1/20th the weight of copper wire,” Bengio said.
“Applications for this material are a big selling point, but from a scientific perspective, at these frequencies carbon nanotube macro-materials behave like a typical conductor,” he said. Even fibers considered “moderately conductive” showed superior performance, he said.
Although manufacturers could simply use thinner copper wires instead of the 30-gauge wires they currently use, those wires would be very fragile and difficult to handle, Pasquali said.
“Amram showed that if you do three things right — make the right fibers, fabricate the antenna correctly and design the antenna according to telecommunication protocols — then you get antennas that work fine,” he said. “As you go to very thin antennas at high frequencies, you get less of a disadvantage compared with copper because copper becomes difficult to handle at thin gauges, whereas nanotubes, with their textile-like behavior, hold up pretty well.”
Co-authors of the paper are, from Rice, graduate students Lauren Taylor and Peiyu Chen, alumnus Dmitri Tsentalovich and Aydin Babakhani, an associate professor of electrical and computer engineering, and, from NIST in Boulder, Colo., postdoctoral researcher Damir Senic, research engineer Christopher Holloway, physicist Christian Long, research scientists David Novotny and James Booth and physicist Nathan Orloff. Pasquali is a professor of chemical and biomolecular engineering, of materials science and nanoengineering and of chemistry.
The U.S. Air Force supported the research.
Suggested Items
RF PCB Design Tips and Tricks
05/08/2025 | Cherie Litson, EPTAC MIT CID/CID+There are many great books, videos, and information online about designing PCBs for RF circuits. A few of my favorite RF sources are Hans Rosenberg, Stephen Chavez, and Rick Hartley, but there are many more. These PCB design engineers have a very good perspective on what it takes to take an RF design from schematic concept to PCB layout.
Trouble in Your Tank: Causes of Plating Voids, Pre-electroless Copper
05/09/2025 | Michael Carano -- Column: Trouble in Your TankIn the business of printed circuit fabrication, yield-reducing and costly defects can easily catch even the most seasoned engineers and production personnel off guard. In this month’s column, I’ll investigate copper plating voids with their genesis in the pre-plating process steps.
Elephantech: For a Greener Tomorrow
04/16/2025 | Marcy LaRont, PCB007 MagazineNobuhiko Okamoto is the global sales and marketing manager for Elephantech Inc., a Japanese startup with a vision to make electronics more sustainable. The company is developing a metal inkjet technology that can print directly on the substrate and then give it a copper thickness by plating. In this interview, he discusses this novel technology's environmental advantages, as well as its potential benefits for the PCB manufacturing and semiconductor packaging segments.
Trouble in Your Tank: Organic Addition Agents in Electrolytic Copper Plating
04/15/2025 | Michael Carano -- Column: Trouble in Your TankThere are numerous factors at play in the science of electroplating or, as most often called, electrolytic plating. One critical element is the use of organic addition agents and their role in copper plating. The function and use of these chemical compounds will be explored in more detail.
IDTechEx Highlights Recyclable Materials for PCBs
04/10/2025 | IDTechExConventional printed circuit board (PCB) manufacturing is wasteful, harmful to the environment and energy intensive. This can be mitigated by the implementation of new recyclable materials and technologies, which have the potential to revolutionize electronics manufacturing.