New RoboBee Flies, Dives, Swims and Explodes out the of Water
October 27, 2017 | Harvard UniversityEstimated reading time: 4 minutes
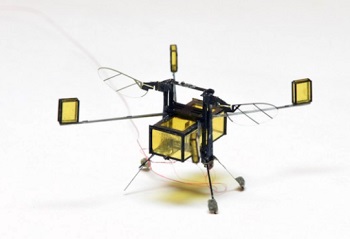
We’ve seen RoboBees that can fly, stick to walls, and dive into water. Now, get ready for a hybrid RoboBee that can fly, dive into water, swim, propel itself back out of water, and safely land.
New floating devices allow this multipurpose air-water microrobot to stabilize on the water’s surface before an internal combustion system ignites to propel it back into the air. This latest-generation RoboBee, which is 1,000 times lighter than any previous aerial-to-aquatic robot, could be used for numerous applications, from search-and-rescue operations to environmental monitoring and biological studies.
The research is described in Science Robotics. It was led by a team of scientists from the Harvard John A. Paulson School of Engineering and Applied Sciences (SEAS) and the Wyss Institute for Biologically-Inspired Engineering at Harvard.
“This is the first microrobot capable of repeatedly moving in and through complex environments,” said Yufeng Chen, who was a graduate student in the Microrobotics Lab at SEAS when the research was conducted and is first author of the paper. “We designed new mechanisms that allow the vehicle to directly transition from water to air, something that is beyond what nature can achieve in the insect world.”
Designing a millimeter-sized robot that moves in and out of water has numerous challenges. First, water is 1,000 times denser than air, so the wing flapping speed must vary widely between the two mediums. If the flapping frequency is too low, the RoboBee can’t fly. If it’s too high, the wing will snap off in water.
By combining theoretical modeling and experimental data, the researchers found the Goldilocks combination of wing size and flapping rate, scaling the design to allow the bee to operate repeatedly in both air and water. Using this multimodal locomotive strategy, the RoboBee flaps its wings at 220 to 300 hertz in air and nine to 13 hertz in water.
Another major challenge the team had to address: at the millimeter scale, the water’s surface might as well be a brick wall. Surface tension is more than 10 times the weight of the RoboBee and three times its maximum lift. Previous research demonstrated how impact and sharp edges can break surface tension on a RoboBee’s entry into water but the question remained: How does it get back out again?
To solve that problem, the researchers retrofitted the RoboBee with four buoyant outriggers—essentially robotic floaties—and a central gas collection chamber. Once the RoboBee swims to the surface, an electrolytic plate in the chamber converts water into oxyhydrogen, a combustible gas fuel.
“Because the RoboBee has a limited payload capacity, it cannot carry its own fuel, so we had to come up with a creative solution to exploit resources from the environment,” said Elizabeth Farrell Helbling, graduate student in the Microrobotics Lab and co-author of the paper. “Surface tension is something that we have to overcome to get out of the water, but is also a tool that we can utilize during the gas collection process.”
Air-water hybrid microrobot uses a tiny, novel sparker inside the chamber ignites the gas to propel the RoboBee out of the water. The robot is designed to passively stabilize in air, so that it always lands on its feet. (Video courtesy of Yufeng Chen/Harvard SEAS)
The gas increases the robot’s buoyancy, pushing the wings out of the water and the floaties stabilize the RoboBee on the water’s surface. From there, a tiny, novel sparker inside the chamber ignites the gas, propelling the RoboBee out of the water. The robot is designed to passively stabilize in air, so that it always lands on its feet.
“By modifying the vehicle design, we are now able to lift more than three times the payload of the previous RoboBee,” said Chen. “This additional payload capacity allowed us to carry the additional devices including the gas chamber, the electrolytic plates, sparker, and buoyant outriggers, bringing the total weight of the hybrid robot to 175 miligrams, about 90mg heavier than previous designs. We hope that our work investigating tradeoffs like weight and surface tension can inspire future multi-functional microrobots – ones that can move on complex terrains and perform a variety of tasks.”
Because of the lack of onboard sensors and limitations in the current motion-tracking system, the RoboBee cannot yet fly immediately upon propulsion out of water but the team hopes to change that in future research.
“The RoboBee represents a platform where forces are different than what we—at human scale—are used to experiencing,” said Robert Wood, Charles River Professor of Engineering and Applied Sciences at Harvard, Core Faculty Member of the Wyss Institute, and senior author of the paper. “While flying the robot feels as if it is treading water; while swimming it feels like it is surrounded by molasses. The force from surface tension feels like an impenetrable wall. These small robots give us the opportunity to explore these non-intuitive phenomena in a very rich way.”
The Harvard Office of Technology Development has filed a patent application and is exploring commercialization opportunities.
The paper was co-authored by Hongqiang Wang, Noah Jafferis, Raphael Zufferey, Aaron Ong, Kevin Ma, Nicholas Gravish, Pakpong Chirarattananon, and Mirko Kovac. It was supported by the National Science Foundation and the Wyss Institute for Biologically Inspired Engineering.
Related video:
Suggested Items
Moog Announces Acquisition of COTSWORKS
07/07/2025 | BUSINESS WIREMoog Inc., a worldwide designer, manufacturer and systems integrator of high-performance precision motion and fluid controls and control systems, announced the acquisition of COTSWORKS Inc., an aerospace and defense fiber optics transceiver component manufacturer, for a purchase price of $63 million.
S&K Aerospace Awarded Major Contract Under DLA Maritime Acquisition Advancement Program
07/02/2025 | BUSINESS WIRES&K Aerospace, LLC has been awarded a significant contract under the Defense Logistics Agency’s (DLA) Maritime Acquisition Advancement Program, managed by the U.S. Naval Supply Command - Weapon Systems Support (NAVSUP WSS) in Mechanicsburg, PA.
Green Circuits to Exhibit Full-Service Electronics Manufacturing Solutions at 2025 SMD Symposium
07/02/2025 | Green CircuitsGreen Circuits, a full-service Electronics Manufacturing Services (EMS) partner to leading OEMs, is pleased to announce its participation in the 2025 SMD Symposium, taking place August 5-7 at the Von Braun Center in Huntsville, Alabama.
I-Connect007 Editor’s Choice: Five Must-Reads for the Week
06/27/2025 | Nolan Johnson, I-Connect007While news outside our industry keeps our attention occupied, the big news inside the industry is the rechristening of IPC as the Global Electronics Association. My must-reads begins with Marcy LaRont’s exclusive and informative interview with Dr. John Mitchell, president and CEO of the Global Electronics Association. For designers, have we finally reached the point in time where autorouters will fulfill their potential?
Knocking Down the Bone Pile: Tin Whisker Mitigation in Aerospace Applications, Part 3
06/25/2025 | Nash Bell -- Column: Knocking Down the Bone PileTin whiskers are slender, hair-like metallic growths that can develop on the surface of tin-plated electronic components. Typically measuring a few micrometers in diameter and growing several millimeters in length, they form through an electrochemical process influenced by environmental factors such as temperature variations, mechanical or compressive stress, and the aging of solder alloys.