New I-Connect007 Team Members Tour American Standard Circuits
November 6, 2017 | Kiersten Rohde and Jonathan Zinski, I-Connect007Estimated reading time: 5 minutes
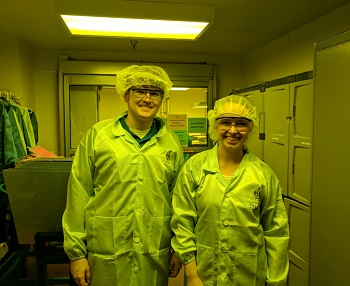
Being a new person in any industry comes with a sharp learning curve. Gaining the necessary knowledge, experience, and skill can come from a variety of sources, such as specific training, attending industry events and trade shows, and experiential learning.
Recently, Anaya Vardya, CEO of American Standard Circuits, invited two of I-Connect007’s newest team members, IT Coordinator Jonathan Zinski and Editor Kiersten Rohde, to tour his facility in West Chicago, Illinois. Happy Holden, resident PCB expert, also joined the newbies on their field trip to ASC.
In the following articles, Jonathan and Kiersten describe their experience touring ASC. Special thanks to Anaya for hosting the I-Connect007 team.
Only the Beginning
by Kiersten Rohde, I-Connect007
Most end-users don't consider the internal components of the devices they use every day. These household devices might include cellphones, computers, microwaves, or even toasters. As a millennial who is new to the industry (and in a non-technical role as an editor for I-Connect007), I have most often experienced the end-products. Little did I realize that inside many of these devices were PCBs—the detailed and fundamental part that serves as the foundation for electronic devices.
My appreciation for the PCB industry expanded when I had the opportunity to tour American Standard Circuits’ facility in West Chicago, Illinois. CEO Anaya Vardya guided me and Jonathan, another millennial coworker, through a number of different process steps involved in making a PCB. We learned more than we could have imagined about PCB construction, and at times were slightly overwhelmed with all the new information.
Throughout the tour, I learned that ASC produces PCBs for much more than typical household uses; they also handle PCB construction for other crucial areas, such as medical and military/aerospace. Further, seeing PCBs being built made some of the terms I’ve encountered “come to life” by connecting them to real materials, factors, components, processes, and applications.
Moving from the very early steps of creating a PCB, we explored various rooms, such as the warehouse, drill room, and yellow room where we wore bunny suits (no, not for Halloween) for entering the cleanroom. During the tour, it quickly became clear that there are numerous steps involved in constructing a PCB, and these steps must be meticulously executed. Employees often handle boards multiple times to successfully finish the PCBs and send them to customers without any errors.
Because I’m a detail-oriented person, I most enjoyed learning about the necessary quality inspection tests done to ensure the final PCBs meet IPC standards. Who would have guessed it, especially since I’m an editor! I was impressed by AOI technology used to identify anomalies on the inner layers and outer layers and correct them when possible. Additionally, seeing a cross-section of a board examined under a microscope to measure copper thickness in the vias using computer software also amazed me.
Overall, I didn’t know what to expect when we stepped out of our Lyft ride at the front doors of American Standard Circuits, but I left with an increased knowledge base that I can continue to build. What I experienced will help me to better understand the content I read and edit and to view the various technical components as less conceptual and more concrete. Although I'm only beginning to learn about how PCBs are made and how they operate, I now know how integral PCBs are to electronics of all kinds. I hope this is only the beginning of my growth in the industry.
Page 1 of 2
Testimonial
"Our marketing partnership with I-Connect007 is already delivering. Just a day after our press release went live, we received a direct inquiry about our updated products!"
Rachael Temple - AlltematedSuggested Items
Indium Corporation Promotes Two Leaders in EMEA (Europe, Middle East, and Africa) Markets
08/05/2025 | Indium CorporationWith its commitment to innovation and growth through employee development, Indium Corporation today announced the promotions of Andy Seager to Associate Director, Continental Sales (EMEA), and Karthik Vijay to Senior Technical Manager (EMEA). These advancements reflect their contributions to the company’s continued innovative efforts with customers across Europe, the Middle East, and Africa (EMEA).
MacDermid Alpha Electronics Solutions Unveils Unified Global Website to Deepen Customer, Talent, and Stakeholder Engagement
07/31/2025 | MacDermid Alpha Electronics SolutionsMacDermid Alpha Electronics Solutions, the electronics business of Elements Solutions Inc, today launched macdermidalpha.com - a unified global website built to deepen digital engagement. The launch marks a significant milestone in the business’ ongoing commitment to delivering more meaningful, interactive, and impactful experiences for its customers, talent, and stakeholders worldwide.
KOKI to Showcase Analytical Services and New HF1200 Solder Paste at SMTA Guadalajara 2025
07/31/2025 | KOKIKOKI, a global leader in advanced soldering materials and process optimization services, will exhibit at the SMTA Guadalajara Expo & Tech Forum, taking place September 17 & 18, 2025 at Expo Guadalajara, Salón Jalisco Halls D & E in Guadalajara, Mexico.
Weller Tools Supports Future Talent with Exclusive Donation to SMTA Michigan Student Soldering Competition
07/23/2025 | Weller ToolsWeller Tools, the industry leader in hand soldering solutions, is proud to announce its support of the upcoming SMTA Michigan Expo & Tech Forum by donating a limited-edition 80th Anniversary Black Soldering Set to the event’s student soldering competition.
Koh Young Appoints Tom Hattori as President of Koh Young Japan
07/21/2025 | Koh YoungKoh Young Technology, the global leader in True 3D measurement-based inspection solutions, announced the appointment of Tom Hattori as President of Koh Young Japan (JKY).