Tech Increases Microfluidic Research Data Output 100-fold
November 8, 2017 | NC State UniversityEstimated reading time: 2 minutes
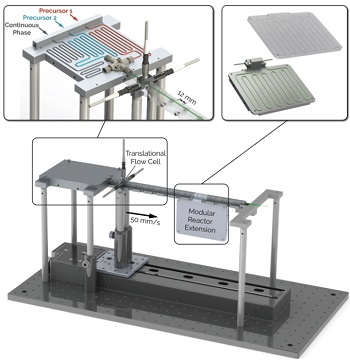
Researchers have developed a technique that allows users to collect 100 times more spectrographic information per day from microfluidic devices, as compared to the previous industry standard. The novel technology has already led to a new discovery: the speed of mixing ingredients for quantum dots used in LEDs changes the color of light they emit – even when all other variables are identical.
“Semiconductor nanocrystals are important structures used in a variety of applications, ranging from LED displays to solar cells. But producing nanocrystalline structures using chemical synthesis is tricky, because what works well on a small scale can’t be directly scaled up – the physics don’t work,” says Milad Abolhasani, an assistant professor of chemical and biomolecular engineering at North Carolina State University and corresponding author of a paper on the work.
“This challenge has led to an interest in continuous nanomanufacturing approaches that rely on precisely controlled microfluidic-based synthesis,” Abolhasani says. “But testing all of the relevant variables to find the best combination for manufacturing a given structure takes an extremely long time due to the limitations of the existing monitoring technologies – so we decided to build a completely new platform.”
Currently, microfluidic monitoring technologies are fixed in place, and monitor either absorption or fluorescence. Fluorescence data tells you what the crystal’s emission bandgap is – or what color of light it emits – which is important for LED applications. Absorption data tells you the crystal’s size and concentration, which is relevant for all applications, as well as its absorption bandgap – which is important for solar cell applications.
To monitor both fluorescence and absorption you’d need two separate monitoring points. And, being fixed in place, people would speed up or slow down the flow rate in the microfluidic channel to control the reaction time of the chemical synthesis: the faster the flow rate, the less reaction time a sample has before it hits the monitoring point. Working around the clock, this approach would allow a lab to collect about 300 data samples in 24 hours.
Abolhasani and his team developed an automated microfluidic technology called NanoRobo, in which a spectrographic monitoring module that collects both fluorescent and absorption data can move along the microfluidic channel, collecting data along the way. The system is capable of collecting 30,000 data samples in 24 hours – expediting the discovery, screening, and optimization of colloidal semiconductor nanocrystals, such as perovskite quantum dots, by two orders of magnitude.
And, because of the translational capability of the novel monitoring module, the system can study reaction time by moving along the microfluidic channel, rather than changing the flow rate – which, the researchers discovered, makes a big difference.
Because NanoRobo allowed researchers to monitor reaction time and flow rate as separate variables for the first time, Abolhasani was the first to note that the velocity of the samples in the microfluidic channel affected the size and emission color of the resulting nanocrystals. Even if all the ingredients were the same, and all of the other conditions were identical, samples that moved – and mixed – at a faster rate produced smaller nanocrystals. And that affects the color of light those crystals emit.
“This is just one more way to tune the emission wavelength of perovskite nanocrystals for use in LED devices,” Abolhasani says.
NC State has filed a provisional patent covering NanoRobo and is open to exploring potential market applications for the technology.
Suggested Items
AI Boom Drives Surge in Data Center Interconnect Demand; Global Market Value to Grow 14.3% in 2025
05/19/2025 | TrendForceTrendForce reports that leading global telecom providers such as SK Telecom and Deutsche Telekom are rolling out Agentic AI services for general users as generative AI becomes increasingly integrated into daily life in 2025.
FTG Achieves Major Milestone with TCCA Certification for Edge+ on Boeing 737NG Family
05/16/2025 | Globe NewswireFiran Technology Group Corporation (FTG) announced that its FLYHT subsidiary has been awarded a Supplemental Type Certificate (STC) by Transport Canada Civil Aviation (TCCA) for the AFIRS Edge+™ product on the Boeing 737NG family of aircraft.
Future-proofing Electronics: ChemFORWARD Works Toward Collaboration for Safer Chemistry
05/19/2025 | Rachel Simon, ChemFORWARDThe electronics industry is facing a critical juncture. As consumer demand for sustainable products rises and regulatory pressures intensify, companies must prioritize the safety of their products and processes. This means not only complying with evolving chemical restrictions but also proactively seeking safer alternatives.
Corning Collaborates with Broadcom to Accelerate AI Data Center Processing Capacity
05/14/2025 | BUSINESS WIRECorning Incorporated, a world leader in glass science and optical physics, today announced a collaboration with Broadcom Incorporated, a leading supplier in the semiconductor field, on a co-packaged optics (CPO) infrastructure that will significantly increase processing capacity within data centers.
Breaking Down Barriers: The Connectivity of Machines in SMT Production Lines
05/14/2025 | Bill Cardoso, Creative ElectronAs the world increasingly moves toward erecting trade barriers, we find ourselves in a paradox. Across the globe, the rise in tariffs and protectionist policies is creating a more fragmented global economy, with nations seeking to insulate themselves from external economic pressures. However, within the confines of the SMT production line, the trend is moving in precisely the opposite direction—toward greater connectivity, integration, and collaboration. Rather than isolating one machine from another, SMT production lines are increasingly interconnected, with data being shared across various stages of the process to improve quality, efficiency, and defect detection.