-
- News
- Books
Featured Books
- pcb007 Magazine
Latest Issues
Current IssueInventing the Future with SEL
Two years after launching its state-of-the-art PCB facility, SEL shares lessons in vision, execution, and innovation, plus insights from industry icons and technology leaders shaping the future of PCB fabrication.
Sales: From Pitch to PO
From the first cold call to finally receiving that first purchase order, the July PCB007 Magazine breaks down some critical parts of the sales stack. To up your sales game, read on!
The Hole Truth: Via Integrity in an HDI World
From the drilled hole to registration across multiple sequential lamination cycles, to the quality of your copper plating, via reliability in an HDI world is becoming an ever-greater challenge. This month we look at “The Hole Truth,” from creating the “perfect” via to how you can assure via quality and reliability, the first time, every time.
- Articles
- Columns
- Links
- Media kit
||| MENU - pcb007 Magazine
Estimated reading time: 2 minutes
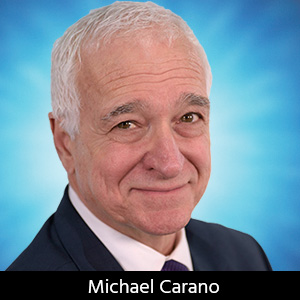
Contact Columnist Form
Trouble in Your Tank: The Critical Importance of Rinsing, Part 2
Introduction
In Part 1 of this series on the importance of rinsing, the author presented an overview of the critical aspects of rinsing as it applies to the overall quality of a printed circuit board, with considerable space devoted to water conservation. Thus, we now turn to how one can improve rinsing effectiveness without increasing water consumption and, by default, significant waste treatment costs.
Rinsing Protocols
The preferred rinsing method of design engineers is counterflow, or cascade rinsing. Still another theory widely held throughout our industry reasons that, if work is left in a rinse tank for longer periods of time, better rinsing will be the result. First, let’s explore the idea of leaving the circuit boards in the rinse for a longer period.
When a rack of PCBs is immersed in a rinse tank, the residual surface contamination is reduced to a practical minimum within 30 seconds as the solution carried in on the surface of the work disperses into the rinse waters. A typical rinse tank—100 gallons with a water flow of five gallons per minute—would decrease the concentration of the solution contaminants at a rate of only 5% for each minute that it remains in the rinse tank. Leaving the work in any longer would have virtually no effect. This demonstrates that rinsing time in a rinse station is a non-linear relationship with respect to removing contamination from the surface of the parts. Yes, this is counter intuitive. We often think that if two minutes in the rinse removes 50% of the residues, then doubling the time in the rinse will remove 100%! This is not the case. Basically, the law of diminishing returns applies. There are many factors in play here including the type of contaminants to be rinsed, affinity of those contaminants to adhere to the printed circuit board, etc.
It is more desirable to have brief exposure times in many (presumably cascade) rinse tanks, which will result in a better dilution rate of the contaminants, than a long exposure time in just a few rinse tanks.
There have been countless studies performed on rinsing mechanisms and how to improve rinsing efficiency. Most of the published studies related to rinsing are based upon multitudes of calculations of volume of water flow relative to number of rinse tanks in use.
To read the Part 1 of this article click here.
To read the full version of this article which appeared in the October 2017 issue of The PCB Magazine, click here.
More Columns from Trouble in Your Tank
Trouble in Your Tank: Metallizing Flexible Circuit Materials—Mitigating Deposit StressTrouble in Your Tank: Can You Drill the Perfect Hole?
Trouble in Your Tank: Yield Improvement and Reliability
Trouble in Your Tank: Causes of Plating Voids, Pre-electroless Copper
Trouble in Your Tank: Organic Addition Agents in Electrolytic Copper Plating
Trouble in Your Tank: Interconnect Defect—The Three Degrees of Separation
Trouble in Your Tank: Things You Can Do for Better Wet Process Control
Trouble in Your Tank: Processes to Support IC Substrates and Advanced Packaging, Part 5