9 Ways to Keep Up with Changes in Manufacturing Technology
December 11, 2017 | Russell Poppe, JJS ManufacturingEstimated reading time: 4 minutes
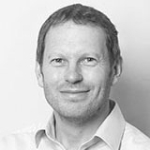
When looking to make a hotel reservation recently, it struck me that most if not all establishments were proudly boasting of bedrooms featuring a "flat screen TV." This got me thinking, since when were they not flat? Since the early 2000’s as it happens, which is quite a while ago.
Yesterday's flat screen TV has been spectacularly surpassed by today's 60" curved 4K OLED smart TV (though sadly not in hotels within my budget). The pace of technological change really is incredibly rapid, though it might not be obvious unless you take time to look back. Day-to-day it just creeps up on you.
The world of manufacturing technology might not be quite as fast to change as consumer electronics, but it is evolving, and faster than you think. Let us assume, from a business point of view, that you want to keep up. Much has been made of Industry 4.0 and 'digital Darwinism', survival of the fittest and all that, so let us take it a step further and say that you need to keep up. Recent evidence shows that companies are increasingly adopting 'servitized' business models and technology is a key enabler, so falling behind the times is not really an option.
When you start to look into this area, there is an amazing amount of development going on. It is essential then to concentrate on what is relevant to your industry, your customers, and your challenges. However, it is also a good idea to spend some time looking at other industries, where 'technology transfer' or 'horizontal innovation' might be appropriate, and give you a leading edge.
So where do you start? Well, here are 9 ideas to get you going:
1. No surprise here, top of the list, at the center of all we do. Make sure you understand what they are working on, and how you will be able to help them not just now, but in two to five years and beyond too.
2. What are their plans? What trends are they seeing in their industry? Can they help you and your customers with ideas and even training? You might be surprised at how willing and able your suppliers are to help.
3. Technology news sites. There are a lot of these, so go surfing (if that’s still a thing) and pick your favorites. Mashable Tech and HuffPost Tech might be good starting points.
4. Industry news sites. These will tell you what your customers, suppliers, and competitors are up to, so essential reading. The same goes for on-line magazines and, yes, the good old-fashioned paper ones that you can browse through over your afternoon coffee.
5. Trade shows and exhibitions. If you pick the right ones, these are possibly the best way to get loads of ideas and information in a short space of time. Most offer a seminar program alongside the trade stands so they are a great learning opportunity. Southern Manufacturing, Subcon, Engineering Design Show and Advanced Engineering all offer strong speaker sessions covering the latest technological advancements.
6. Trade associations. Joining an industry relevant association is another way of ensuring you are getting relevant information through newsletters, seminars, and networking if you are a member.
7. Professional bodies. These usually have both news sites and professional development training opportunities. These tend to be educational and cover a range of industries, so they are well worth a regular review.
8. Google alerts. If you have a particular topic that you are interested in, set up a Google alert. They will then do the hard work for you and scan the web for relevant content as it when it is published, sending you links to relevant articles in a handy email. Just be very specific about what you are looking for or you will get too much irrelevant information and don’t ask for the alerts to be sent too often otherwise it can get overwhelming and you’re less likely to read them.
9. Social media. In general, very handy for seeing what other people are up to but in particular the professional forums such as LinkedIn have special interest groups where ideas, challenges, and expertise can be shared.
You might think that all of this research takes a while, and you would be right. You might even feel just a little bit guilty spending all that time on the internet and chatting to people, as it’s not real work, is it? Well, just remind yourself (and your boss if necessary) just how fast things change, and how quickly you could fall behind your competitors if you don’t keep up.
It is important to keep it going too; something you dismiss today could become very relevant tomorrow. You don't have to be that old to remember first connecting to the internet and thinking 'yes, lovely, but what’s the point?' Things change.
Once you are enthused over all these new ideas, you will be keen to implement what you've learned. There might be pitfalls in being an 'early adopter' of new technology, but consider acting as quickly as you can to get the most benefit. Of course, something better will come along next year, but it might be too late by then.
Suggested Items
Real Time with... IPC APEX EXPO 2025: Aster—Enhancing Design for Effective Testing Strategies
04/18/2025 | Real Time with...IPC APEX EXPOWill Webb, technical director at Aster, stresses the importance of testability in design, emphasizing early engagement to identify testing issues. This discussion covers the integration of testing with Industry 4.0, the need for good test coverage, and adherence to industry standards. Innovations like boundary scan testing and new tools for cluster testing are introduced, highlighting advancements in optimizing testing workflows and collaboration with other tools.
Real Time with… IPC APEX EXPO 2025: Schmoll America Showcasing Four Advanced Machines
03/05/2025 | Real Time with...IPC APEX EXPOIn an expansive booth, Schmoll America is showcasing three advanced Schmoll machines and one from Impex, its partner company. Kurt emphasizes Schmoll's commitment to growth and excellence as Schmoll America approaches its first anniversary. Stop by booth 4123 to see the action.
Smart Factory Insights: The Costs of Legacy Thinking
12/01/2021 | Michael Ford -- Column: Smart Factory InsightsAs humans, we learn facts, gain impressions, create solutions, put practices into place, and move onto our next challenge. Over time, our intent is to create a legacy of value, but in many cases, we are creating legacies in a different sense. Our knowledge, experience, and creations age or become superseded, but there is resistance to replace or update. An increasing gap develops between perception and reality. Younger, more agile peers take advantage, get ahead, and we look away, thinking that they don’t know what they are doing. Though a natural human phenomenon, decision-makers in manufacturing today need to bear this mind more than ever.
Managing Cyber-Threats Within Electronics Manufacturing
11/16/2018 | Neil Sharp, JJS ManufacturingThe rise of the 4th Industrial Revolution (4IR) has brought with it digital interconnectivity that offers unprecedented opportunities for original equipment manufacturers (OEMs). But with that openness there also comes risk—the threat of the loss of data, the theft of capital or intellectual property, and the disruption of access to systems or operational technology—all of which can impede businesses and impact on trade.
IoT: Driving Change in Manufacturing
10/15/2018 | Stephen Las Marias, I-Connect007In the manufacturing world, the Internet of Things (IoT) can be seen as an element of Industry 4.0. The idea behind it is that factories would evolve to become smarter, to become a lot more flexible—to be able to make the products that customers want, basically at any time that they need.